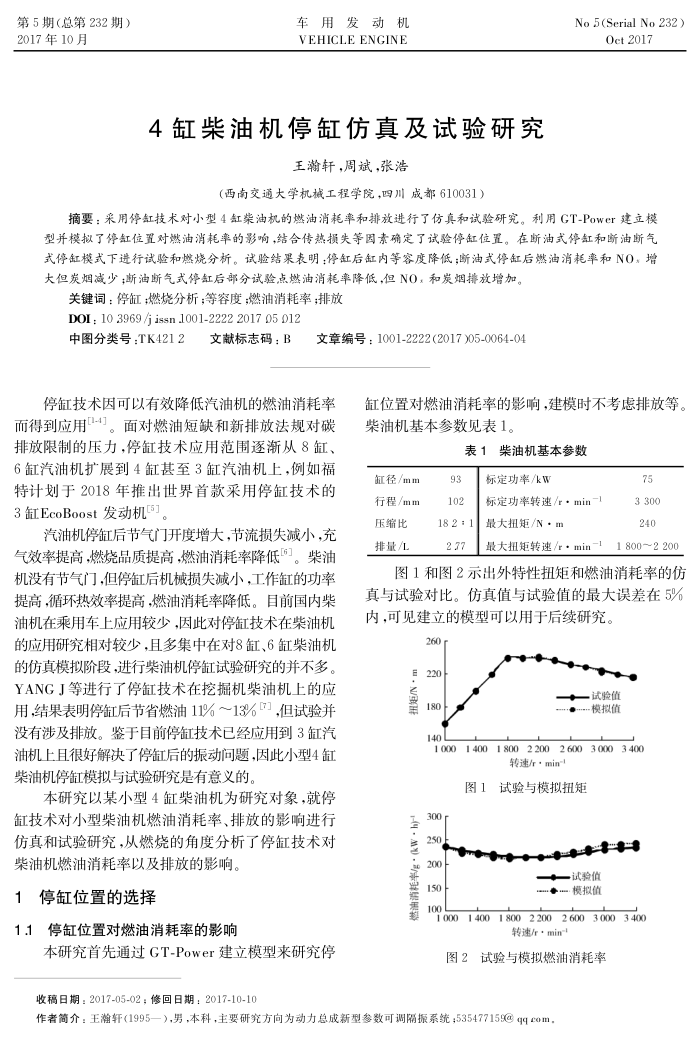
第5期(总第232期) 2017年10月
车用发动机 VEHICLE ENGINE
4缸柴油机停缸仿真及试验研究
王瀚轩周斌,张浩
(西南交通大学机械工程学院,四川成都610031)
No 5 (Serial No 232 )
Oct2017
摘要:采用停缸技术对小型4缸柴油机的燃油消耗率和排放进行了仿真和试验研究。利用GT-Power建立模型并模拟了停缸位置对燃油消耗率的影响,结合传热损失等因素确定了试验停缸位置。在断油式停缸和断油断气式停缸模式下进行试验和燃烧分析。试验结果表明停缸后缸内等容度降低:断油式停缸后燃油消耗率和NO增大但炭烟减少;断油断气式停缸后部分试验点燃油消耗率降低,但NO,和炭烟排放增加。
关键词:停缸燃烧分析:等容度:燃油消耗率;排放 DOI: 10 3969 /j issn 1001-2222 2017 05 012
中图分类号.TK4212
文献标志码:B
文章编号:1001-2222(2017)05-0064-04
停缸技术因可以有效降低汽油机的燃油消耗率而得到应用-4。面对燃油短缺和新排放法规对碳排放限制的压力,停缸技术应用范围逐渐从8缸、 6缸汽油机扩展到4缸甚至3缸汽油机上,例如福特计划于2018年推出世界首款采用停缸技术的 3缸EcoBoost发动机[5]
汽油机停缸后节气门开度增大,节流损失减小,充气效率提高,燃烧品质提高,燃油消耗率降低。柴油机没有节气,但停缸后机械损失减小,工作缸的功率提高,循环热效率提高,燃油消耗率降低。目前国内柴油机在乘用车上应用较少,因此对停缸技术在柴油机的应用研究相对较少,且多集中在对8缸、6缸柴油机的仿真模拟阶段,进行柴油机停缸试验研究的并不多 YANGJ等进行了停缸技术在挖掘机柴油机上的应用,结果表明停缸后节省燃油11%~13%7,但试验并没有涉及排放。鉴于目前停缸技术已经应用到3缸汽油机上且很好解决了停缸后的振动问题,因此小型4缸柴油机停缸模拟与试验研究是有意义的
本研究以某小型4缸柴油机为研究对象,就停缸技术对小型柴油机燃油消耗率、排放的影响进行仿真和试验研究,从燃烧的角度分析了停缸技术对柴油机燃油消耗率以及排放的影响。
停缸位置的选择 1
1.1停缸位置对燃然油消耗率的影响
本研究首先通过GT-Power建立模型来研究停收稿日期:2017-05-02;修回日期:2017-10-10
缸位置对燃油消耗率的影响,建模时不考虑排放等柴油机基本参数见表1。
表1
柴油机基本参数
缸径/mm 行程/mm 压缩比排量/L
93 102 18 2 : 1 2.77
标定功率/kw
标定功率转速/r·min-1 最大扭矩/N·m
最大扭矩转速/r·min-1
75 00% 240
1 800~2 200
图1和图2示出外特性扭矩和燃油消耗率的仿真与试验对比。仿真值与试验值的最大误差在5% 内,可见建立的模型可以用于后续研究。
260 r 220
N/
(4
180 Y 140
试验值模拟值
1 0001 4001 800 2 2002 600 3 0003 400
转速/r·min-
图1试验与模拟扭矩
300
( 250
,8/ 200
150 100
+试验值模拟
00090080 1000
转速/r·min-
图2试验与模拟燃油消耗率
作者简介:王瀚轩(1995—),男,本科,主要研究方向为动力总成新型参数可调隔振系统;535477159@qeom,