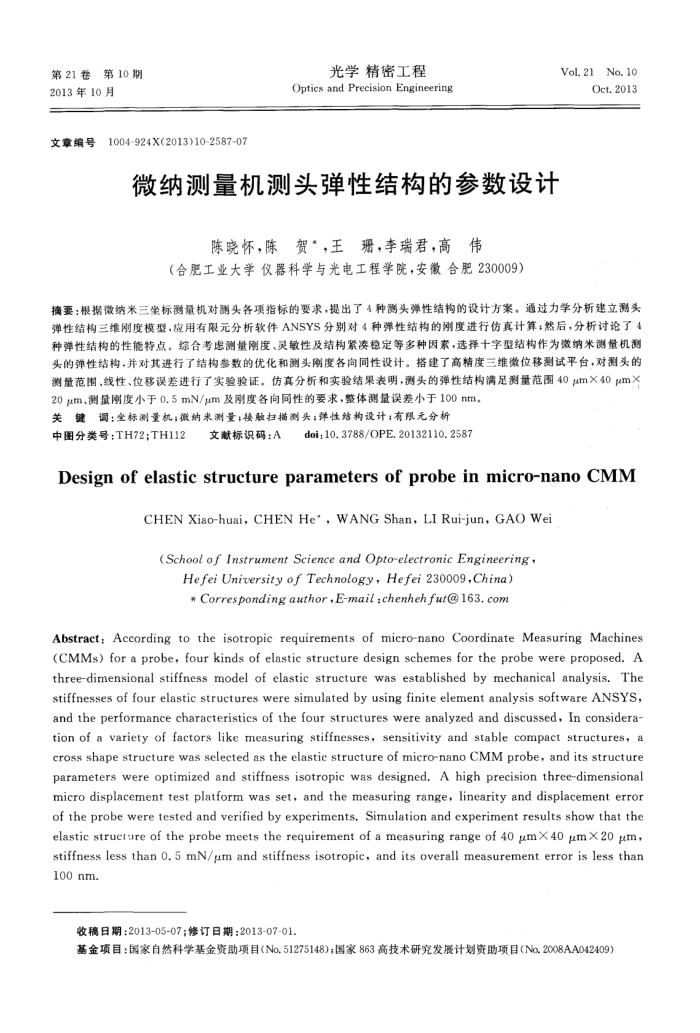
第21卷第10期 2013年10月
1004-924X(2013)102587-07
文章编号
光学精密工程
Optics and Precision Engineering
微纳测量机测头弹性结构的参数设计
陈晓怀,陈贺*,王珊,李瑞君,高伟
(合肥工业大学仪器科学与光电工程学院,安徽合肥230009)
Vol.21No.10
Oct.2013
摘要:根据微纳米三垒标测量机对测头各项指标的要求,提出了4种测头弹性结构的设计方案。通过力学分析建立测头弹性结构三维刚度模型,应用有限元分析软件ANSYS分别对4种弹性结构的刚度进行仿真计算;然后,分析讨论了4 种弹性结构的性能特点。综合考虑测量刚度、灵敏性及结构紧凑稳定等多种因索,选择十字型结构作为微纳米测量机测头的弹性结构,并对其进行了结构参数的优化和测头刚度各向同性设计。搭建了高精度三维微位移测试平台,对测头的测量范围、线性、位移误差进行了实验验证。仿真分析和实验结果表明,测头的弹性结构满足测量范围40um×40mX
20μm、测量刚度小于0.5mN/μm及刚度各向同性的要求,整体测量误差小于100nm。关键调:坐标测量机;微纳来测量;接触担描测头;弹性结构设计;有限元分析
中图分类号:TH72;TH112
文献标识码:A
doi;10. 3788/OPE. 20132110. 2587
Designofelasticstructureparametersofprobeinmicro-nanoCMM
CHEN Xiao-huai, CHEN He',WANG Shan,LI Rui-jun, GAO Wei(School of Instrument Science and Opto-electronicEngineering
Hefei University of Technology,Hefei230009,China Correspondingauthor,E-mail:chenhehfut163.com
Abstract: According to the isotropic requirements of micro-nano Coordinate Measuring Machines(CMMs) for a probe, four kinds of elastic structure design schemes for the probe were proposed. A three-dimensional stiffness model of elastic structure was established by mechanical analysis. The stiffnesses of four elastic structures were simulated by using finite element analysis software ANSYS and the performance characteristics of the four structures were analyzed and discussed, In considera-tion of a variety of factors like measuring stiffnesses, sensitivity and stable compact structures, a cross shape structure was selected as the elastic structure of micro-nano CMM probe, and its structure parameters were optimized and stiffness isotropic was designed. A high precision three-dimensional micro displacement test platform was set, and the measuring range, linearity and displacement error of the probe were tested and verified by experiments. Simulation and experiment results show that the elastic structure of the probe meets the requirement of a measuring range of 40 μmX 40 μmX 20 μm, stiffness less than o. 5 mN/μm and stiffness isotropic, and its overall measurement error is less than 100 nm.
收稿日期:2013-05-07;修订日期:2013-07-01
基金项目:国家自然科学基金资助项目(No.51275148);国家863高技术研究发展计划资助项目(Na.2008AA042409)