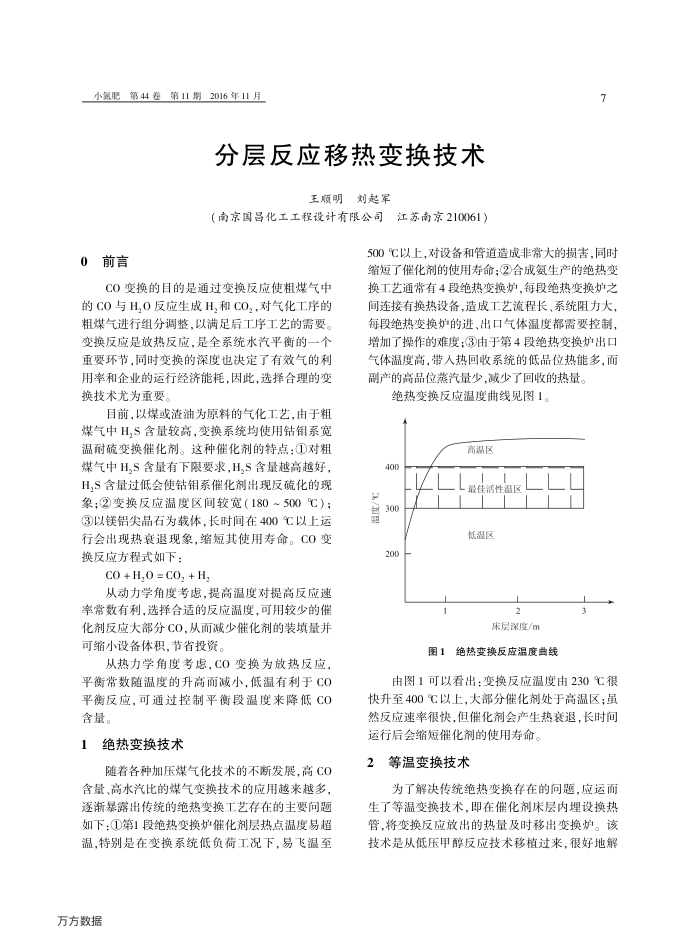
0前言
分层反应移热变换技术
王顺明刘起军
(南京国昌化工工程设计有限公司
江苏南京210061)
7
500%以上,对设备和管道造成非常大的损害,同时缩短了催化剂的使用寿命:②合成氢生产的绝热变
CO变换的目的是通过变换反应使粗煤气中的CO与H,O反应生成H,和CO,,对气化工序的租煤气进行组分调整,以满足后工序工艺的需要。变换反应是放热反应,是全系统水汽平衡的一个重要环节,同时变换的深度也决定了有效气的利用率和企业的运行经济能耗,因此,选择合理的变换技术尤为重要。
目前,以煤或渣油为原料的气化工艺,由于粗煤气中H,S含量较高,变换系统均使用钻钼系宽温耐硫变换催化剂。这种催化剂的特点:(1)对粗煤气中H,S含量有下限要求,H,S含量越高越好, H,S含量过低会使钻钼系催化剂出现反硫化的现象;②变换反应温度区间较宽(180~500℃); 3以镁铝尖晶石为载体,长时间在400C以上运行会出现热衰退现象,缩短其使用寿命。CO变换反应方程式如下:
CO + H,O = CO, + H,
从动力学角度考虑,提高温度对提高反应速率常数有利,选择合适的反应温度,可用较少的催化剂反应大部分CO,从而减少催化剂的装填量并可缩小设备体积,节省投资。
从热力学角度考虑,CO变换为放热反应,平衡常数随温度的升高而减小,低温有利于CO 平衡反应,可通过控制平衡段温度来降低CO 含量。
绝热变换技术 1
随着各种加压煤气化技术的不断发展,高CO 含量、高水汽比的煤气变换技术的应用越来越多逐渐暴露出传统的绝热变换工艺存在的主要问题如下:1第1段绝热变换炉催化剂层热点温度易超温,特别是在变换系统低负荷工况下,易飞温至
万方数据
换工艺通常有4段绝热变换炉,每段绝热变换炉之间连接有换热设备,造成工艺流程长、系统阻力大,每段绝热变换炉的进、出口气体温度都需要控制,增加了操作的难度:③由于第4段绝热变换炉出口气体温度高,带入热回收系统的低品位热能多,面副产的高品位蒸汽量少,减少了回收的热量。
绝热变换反应温度曲线见图1。
高温区
400
最佳活性温区
做300
低温区
200
1
2
床层深度/m
图1绝热变换反应温度曲线
3
由图1可以看出:变换反应温度由230℃很
快升至400℃以上,大部分催化剂处于高温区:量然反应速率很快,但催化剂会产生热衰退,长时间
运行后会缩短催化剂的使用寿命。 2等温变换技术
为了解决传统绝热变换存在的问题,应运而
生了等温变换技术,即在催化剂床层内埋设换执热管,将变换反应放出的热量及时移出变换炉。该技术是从低压甲醇反应技术移植过来,很好地解