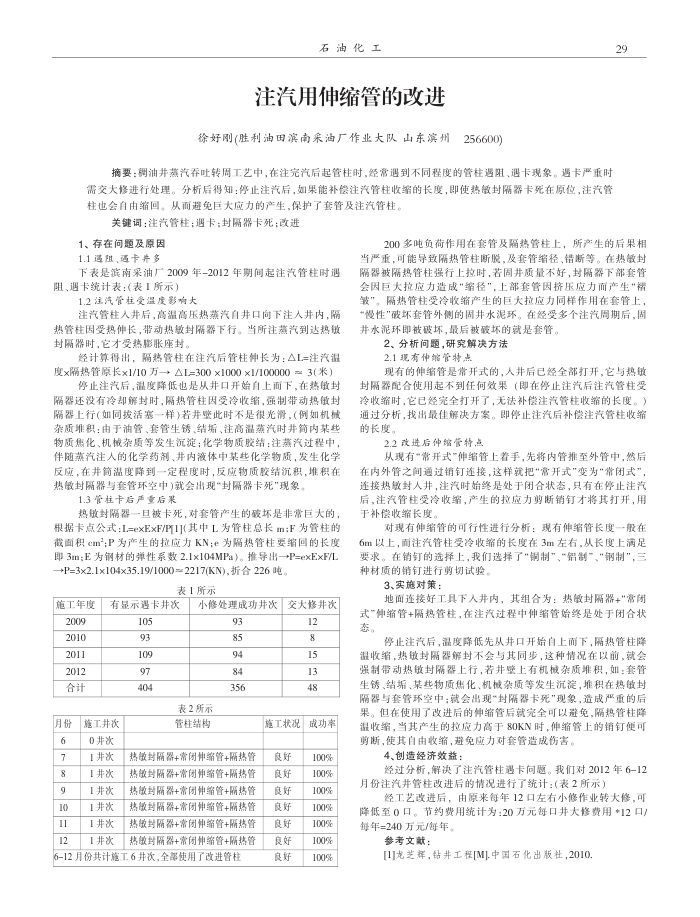
石油化工
注汽用伸缩管的改进
徐好刚(胜利油田滨南采油厂作业大队山东滨州
256600)
摘要:调油井燕汽吞吐转周工艺中,在注完汽后起管柱时,经常遇到不同程度的管柱遇阻、遇卡现象。遇卡严重时需交大修进行处理。分析后得知:停止注汽后,如果能补偿注汽管柱收缩的长度,即使热敏封隔器卡死在原位,注汽管柱也会自由缩回。从而避免巨大应力的产生,保护了套管及注汽管柱。
关键词:注汽管柱;遇卡;封隔器卡死;改进
1、存在问题及原因 1.1避组,遇卡并多
下表是滨南采油厂2009年-2012年期间起注汽管柱时遇阻、遇卡统计表:(表1所示)
1.2注汽管柱受温度影响大
注汽管柱人并后,高温高压热燕汽自井口向下注人井内,隔
热管柱固受势伸长,带动热数封隔器下行。当所注燕汽到达势致封隔器时,它才受热影胀座封。
经计算得出,隔热管柱在注汽后管柱伸长为:△L=注汽温度×隔热管原长×1/10万→△L=300×1000×1/100000=3米)
停止注汽后,温度降低也是从并口开始自上而下,在热致封
隔器还没有冷却解封时,隔热管柱因受冷收缩,强制带动热敏封隔器上行(如同拨活塞一样)若并暨此时不是很光滑,(例如机械杂质维积:由于油管、套管生锈、结墙、注高温燕汽时井简内某些物质焦化、机械杂质等发生沉淀;化学物质胶结:注燕汽过程中,伴随燕汽注人的化学药剂、并内液体中某些化学物质,发生化学反应,在并简温度降到一定程度时,反应物质胶结沉积,堆积在热敏封隔器与套管环空中)就会出现"封隔器卡死"现象。
1.3管柱卡后严重后果
热敏封隔器一旦被卡死,对套管产生的酸坏是非常巨大的,根据卡点公式:L=exExF/P[1](其中L为管柱总长m;F为管柱的截面积cm’;P为产生的拉应力KN;e为隔热管柱要缩回的长度即3m;E为钢材的弹性系数2.1x104MPa)。推导出→P=exExF/L →P=3x2.1x×104x35.19/10002217(KN),折合 226 吨。
表1所示
施工年度 6000 2010 2011 2012 合计
月份 6 7 8 9 10
12
有显示遇卡井次
105 E6 601 97 404
施工井次 0井次 1井次 1井次 1井次 1井次 1井次 1井次
小修处理成功井次交大修井次
93 85 94 t8 356
表2所示管柱结构
热敏封隔器+常闭伸缩管+隔热管热敏封隔器+常闭伸缩管+隔热管热敏封隔器+常闭伸缩管+隔热管热敏封隔器+常闭伸缩管+隔热管热敏封隔器+常闭伸缩管+隔热管热敏封隔器+常闭伸缩管+隔热管
6-12月份共计施工6并次,全部使用了改进管柱
施工状况良好良好良好良好良好良好良好
12 8 15 13 48
成功率 100% 100%%00m 100% 100% 100% 100%
29
200多吨负荷作用在套管及隔热管柱上,所产生的后果相当严重,可能导致隔热管柱断脱,及套管缩径、错断等。在热敏封隔器被隔热管柱强行上拉时,若固并质量不好,封隔器下部套管会因巨大拉应力造成“缩径”,上部套管因挤压应力而产生“裕皱"。隔热管柱受冷收缩产生的巨大拉应力同样作用在套管上,*慢性"破坏套管外侧的固井水泥环。在经受多个注汽周期后,固并水泥环即被破坏,最后被酸坏的就是套管。
2、分析问题,研究解决方法 2.1现有伸施管特点
现有的伸缩管是常开式的,人井后已经全部打开,它与热
封隔器配合使用起不到任何效果(即在停止注汽后注汽管柱受冷收缩时,它已经完全打开了,无法补偿注汽管柱收缩的长度。)通过分析,找出最律解决方累。即停止注汽后补偿注汽管柱收缩的长度,
2.2改进后伸缩管特点
从现有"常开式"伸缩管上着手,先将内管推至外管中,然后在内外管之间通过销钉连接,这样就把"常开式"变为"常闭式”,连接热数封人井,注汽时始终是处于闭合状态,只有在停止注汽后,注汽管柱受冷收缩,产生的拉应力剪断销钉才将其打开,用于补偿收缩长度
对现有伸缩管的可行性进行分析:现有伸缩管长度一般在 6m以上,面注汽管柱受冷收缩的长度在3m左右,从长度上满足要求。在销钉的选择上,我们选择了“铜制”、“铅制”、“钢制”,三种材质的销钉进行剪切试验。
3、实施对策:
地面连接好工具下人井内,其组合为:热敏封隔器+“常闭式"伸缩管+隔热管柱,在注汽过程中伸缩管始终是处于闭合状
态。
停止注汽后,温度降低先从井口开始自上而下,隔热管柱降
温收缩,热敏封隔器解封不会与其同步,这种情况在以前,就会强制带动热致封隔器上行,若并暨上有机械杂质摊积,如:套管生锈、结垢、某些物质焦化、机械杂质等发生沉淀,堆积在热做封隔器与套管环空中;就会出现"封隔器卡死"现象,造成严重的后果。但在使用了改进后的伸缩管后就完全可以避免,隔热管柱降
剪断,使其自由收缩,避免应力对套管造成伤害。
4、创造经济效益:
经过分析,解决了注汽管柱遇卡间题。我们对2012年6-12 月份注汽井管柱改进后的情况进行了统计:(表2所示)
经工艺改进后,由原来每年12口左右小修作业转大修,可降低至0口。节约费用统计为:20万元每口井大修费用*12口/ 每年=240万元/每年。
参考文献:
[1]龙芝辉,钻井工程[M]中国石化出版社,2010