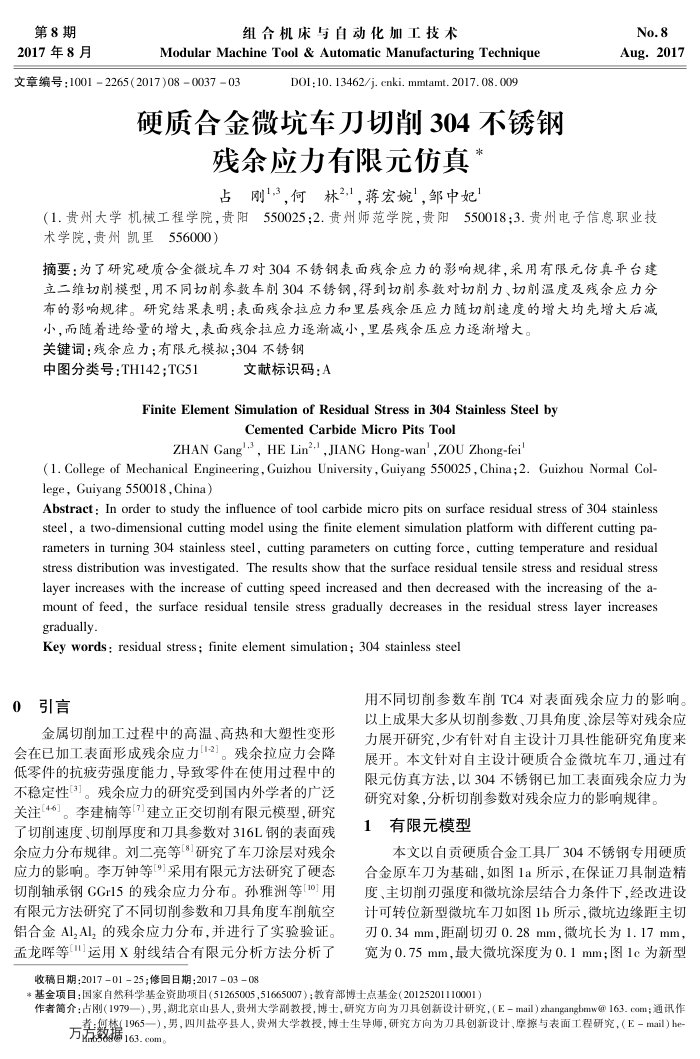
第8期 2017年8月
组合机床与自动化加工技术
Modular Machine Tool & Automatic Manufacturing Technique
文章编号:10012265(2017)08003703
D0I:10.13462/j. cnki. mmtamt.2017.08.009
硬质合金微坑车刀切削304不锈钢
残余应力有限元仿真占刚1,3,何林2,1,蒋宏婉,邹中妃
No.8 Aug.2017
(1.贵州大学机械工程学院,贵阳550025;2.贵州师范学院,贵阳550018;3.贵州电子信息职业技术学院,贵州凯里556000)
摘要:为了研究硬质合金微坑车刀对304不锈钢表面残余应力的影响规律,采用有限元仿真平台建立二维切削模型,用不同切削参数车削304不锈钢,得到切削参数对切削力、切削温度及残余应力分
小,而随着进给量的增大,表面残余拉应力逐渐减小,里层残余压应力逐渐增大。关键词:残余应力;有限元模拟;304不锈钢
中图分类号:TH142;TG51
文献标识码:A
Finite Element Simulation of Residual Stress in 304 Stainless Steel by
Cemented Carbide Micro Pits Tool
ZHAN Gang"3, HE Lin2.,JIANG Hong-wan',ZOU Zhong-fei'
(1. College of Mechanical Engineering, Guizhou University, Guiyang 550025, China;2. Guizhou Normal Col-lege,Guiyang 550018,China)
Abstract : In order to study the influence of tool carbide micro pits on surface residual stress of 304 stainless steel, a two-dimensional cutting model using the finite element simulation platform with different cutting pa-rameters in turning 304 stainless steel, cutting parameters on cutting force, cutting temperature and residual stress distribution was investigated. The results show that the surface residual tensile stress and residual stress layer increases with the increase of cutting speed increased and then decreased with the increasing of the a-mount of feed, the surface residual tensile stress gradually decreases in the residual stress layer increases gradually
Key words: residual stress; finite element simulation; 304 stainless stee
引言 0
金属切削加工过程中的高温、高热和大塑性变形会在已加工表面形成残余应力[1-2]。残余拉应力会降低零件的抗疲劳强度能力,导致零件在使用过程中的不稳定性[3]。残余应力的研究受到国内外学者的广泛关注46]。李建楠等[7建立正交切削有限元模型,研究广切削速度、切削厚度和力具参数对316L钢的表面残余应力分布规律。刘二亮等[8]研究了车刀涂层对残余应力的影响。李万钟等[9]采用有限元方法研究了硬态切削轴承钢GGr15的残余应力分布。孙雅洲等[10]用有限元方法研究了不同切削参数和刀具角度车削航空铝合金Al,Al的残余应力分布,并进行了实验验证。孟龙晖等运用X射线结合有限元分析方法分析了
收稿日期:2017-01-25;修回日期:2017-03-08
用不同切削参数车削TC4对表面残余应力的影响。以上成果大多从切削参数、刀具角度、涂层等对残余应力展并研究,少有针对自主设计力具性能研究角度来展并。本文针对自主设计硬质合金微坑车力,通过有限元仿真方法,以304不锈钢已加工表面残余应力为
研究对象,分析切削参数对残余应力的影响规律。 1有限元模型
本文以自贡硬质合金工具厂304不锈钢专用硬质合金原车刀为基础,如图1a所示,在保证刀具制造精度、主切削刃强度和微坑涂层结合力条件下,经改进设计可转位新型微坑车刀如图1b所示,微坑边缘距主切刃0.34mm,距副切刃0.28mm,微坑长为1.17mm,宽为0.75mm,最大微坑深度为0.1mm;图1c为新型
*基金项目:国家自然科学基金资助项目(51265005,51665007);教育部博士点基金(20125201110001)
作者简介:占刚(1979—),男,潮北京山县人,贵州大学副教授,博士,研究方向为刀具创新设计研究,(E-mail)zhanganghmw@163.com;通讯作
者:侧禁(1965一),男,四川盐亭县人,费州大学教授,博士生导师,研筑方向为刀其创新设计、摩擦与表面工程研究,(E-mail)he 万发数据163.com。