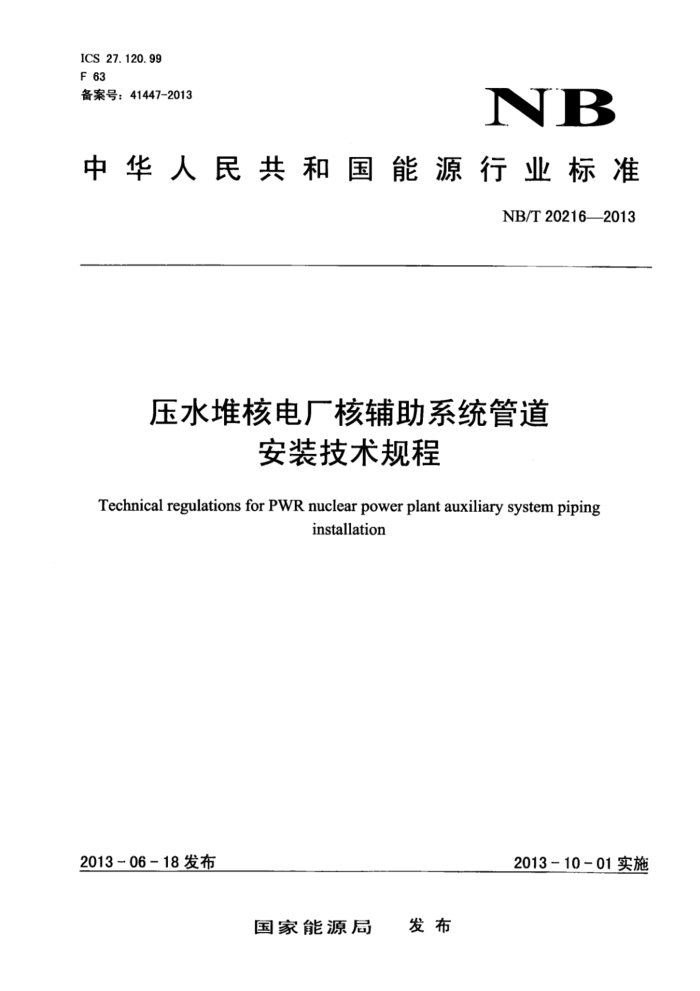
ICS 27.120.99
F 63
备案号:41447-2013
NB
中 华 人 民 共 和 国 能 源 行 业 标 准
NB/T20216—2013
压水堆核电厂核辅助系统管道
安装技术规程
Technical regulations for PWR nuclear power plant auxiliary system piping installation
2013-06-18发布 2013-10-01实施
国家能源局 发 布
NB/T 20216—2013
目 次
前言………………………………………………………………………………………………………………………………………………………………………………………………III
1 范围………………………………………………………………………………………………………………………………………………………………………………………………1
2 规范性引用文件………………………………………………………………………………………………………………………………………………………………………1
3 术语和定义…………………………………………………………………………………………………………………………………………………………………………………1
4 总则………………………………………………………………………………………………………………………………………………………………………………………………2
5 通用技术要求…………………………………………………………………………………………………………………………………………………………………………2
5.1 总要求………………………………………………………………………………………………………………………………………………………………………………2
5.2 施工材料的要求……………………………………………………………………………………………………………………………………………………………2
5.3 切割下料………………………………………………………………………………………………………………………………………………………………………………3
5.4 焊工……………………………………………………………………………………………………………………………………………………………………………………3
5.5 焊接填充材料…………………………………………………………………………………………………………………………………………………………………3
5.6 焊接相关要求……………………………………………………………………………………………………………………………………………………………3
5.7 焊接接头热处理…………………………………………………………………………………………………………………………………………………………………3
6 管道支架预制………………………………………………………………………………………………………………………………………………………………………4
6.1 支架部件的成形…………………………………………………………………………………………………………………………………………………………4
6.2 支架组装……………………………………………………………………………………………………………………………………………………………………………………4
6.3 架焊接………………………………………………………………………………………………………………………………………………………………………………4
6.4 支架检查、检验……………………………………………………………………………………………………………………………………………………………4
6.5 表面处理……………………………………………………………………………………………………………………………………………………………………………4
6.6 贮存……………………………………………………………………………………………………………………………………………………………………………………4
7 管道预制………………………………………………………………………………………………………………………………………………………………………………4
7.1 管道分级……………………………………………………………………………………………………………………………………………………………………………4
7.2 管道部件的加工……………………………………………………………………………………………………………………………………………………………5
7.3 管道的组对……………………………………………………………………………………………………………………………………………………………………5
7.4 管道焊接……………………………………………………………………………………………………………………………………………………………………………5
7.5 检查和检验………………………………………………………………………………………………………………………………………………………………………5
7.6 表面处理………………………………………………………………………………………………………………………………………………………………………………6
7.7 贮存……………………………………………………………………………………………………………………………………………………………………………………7
7.8 完工图……………………………………………………………………………………………………………………………………………………………………………7
8 支架安装……………………………………………………………………………………………………………………………………………………………………………………7
8.1 支架的安装偏差要求……………………………………………………………………………………………………………………………………………………7
8.2 支架基板及锚固螺栓的安装……………………………………………………………………………………………………………………………………9
8.3 支架构件的安装……………………………………………………………………………………………………………………………………………………………………11
8.4 二阶段支架的安装………………………………………………………………………………………………………………………………………………………17
I
NB/T 20216—2013
9 管道安装……………………………………………………………………………………………………………………………………………………………………………………24
9.1 管道及附件的安装要求…………………………………………………………………………………………………………………………………………………24
9.2 法兰的安装要求……………………………………………………………………………………………………………………………………………………………25
9.3 阀门的安装要求……………………………………………………………………………………………………………………………………………………………26
9.4 管道及其部件的焊接…………………………………………………………………………………………………………………………………………………27
9.5 标识……………………………………………………………………………………………………………………………………………………………………………………30
9.6 清洁…………………………………………………………………………………………………………………………………………………………………………………30
9.7 无损检验…………………………………………………………………………………………………………………………………………………………………………32
9.8 现场补漆…………………………………………………………………………………………………………………………………………………………………………32
9.9 安装完工试验…………………………………………………………………………………………………………………………………………………………………32
10 管道绝热安装…………………………………………………………………………………………………………………………………………………………………………34
10.1 一般规定……………………………………………………………………………………………………………………………………………………………………………34
10.2 绝热安装技术要求……………………………………………………………………………………………………………………………………………………34
10.3 固定件、支承件的安装…………………………………………………………………………………………………………………………………………34
10.4 防潮层的施工……………………………………………………………………………………………………………………………………………………………34
10.5 保护层的施工……………………………………………………………………………………………………………………………………………………………35
10.6 单壁保温盒的施工……………………………………………………………………………………………………………………………………………………35
10.7 双壁保温盒的施工……………………………………………………………………………………………………………………………………………………35
11 竣工文件………………………………………………………………………………………………………………………………………………………………………………35
附录A(资料性附录) 推荐的支架焊缝接头类型…………………………………………………………………………………………………………37
附录B(规范性附录) 管道尺寸偏差………………………………………………………………………………………………………………………………41
附录C(资料性附录) 推荐的管道焊缝接头类型………………………………………………………………………………………………………45
附录D(资料性附录) 法兰紧固力矩……………………………………………………………………………………………………………………………47
附录E(规范性附录) 水质等级………………………………………………………………………………………………………………………………………51
II
NB/T 20216—2013
前 言
本标准按照GB/T 1.1——2009给出的规则起草。
本标准由能源行业核电标准化技术委员会提出。
本标准由核工业标准化研究所归口。
本标准起草单位:中国核工业二三建设有限公司。
本标准主要起草人:程璞、刘志琪、左刚。
III
NB/T 20216—2013
压水堆核电厂核辅助系统管道
安装技术规程
1 范围
本标准规定了压水堆核电厂核辅助系统管道及其支架的预制和安装通用技术要求。
本标准适用于二代改进型压水堆核电厂核辅助系统管道及其支架的预制和安装;其它类型压水堆核电厂可参考使用。
2 规范性引用文件
下列文件对于本标准的应用是必不可少的。凡是注日期的引用文件,仅所注日期的版本适用于本标准。凡是不注日期的引用文件,其最新版本(包括所有的修改单)适用于本标准。
GB/T 13452.2 色漆和清漆 漆膜厚度的测定
GB 50126 工业设备及管道绝热工程施工规范
NB/T 20002 压水堆核电厂焊接技术规范
NB/T 20003 核电厂核岛机械设备无损检测
3 术语和定义
下列术语和定义适用于本标准。
3.1
核辅助系统 nuclear auxiliary system
除核岛主系统(蒸汽产生系统)以外的核蒸汽供应系统(NSSS)设施和核岛其他配套设施(BNI).
3.2
等轴图 isometric
按照等轴测投影的制图方法,以单线表示管道空间位置的轴测图。
3.3
质量跟踪文件 quality follow files
用于记录施工活动和质量是否达到适用的图纸、技术文件、质量要求的过程文件。按照施工活动的质保级别质量跟踪文件分为质量计划、工作计划和任务单三种。
3.4
焊接控制单 welding control sheets
记录管道焊缝的材料、部件、焊接工艺、焊接填充材料、焊工、操作工序、检验内容等信息的质量记录文件。焊接控制单是质量跟踪文件的主要组成部分。
3.5
环向接缝 annular juncture
垂直于管道轴线的接缝,也指方形绝热结构相对于管道轴线的横缝、纵缝。
3.6
1
NB/T 20216—2013
纵向接缝 longitudinal juncture
平行于管道轴线的接缝。
4 总则
4.1 从事施工的单位应按照中华人民共和国国务院令第500号《民用核安全设备监督管理条列》和国家环境保护总局令第43号《民用核安全设备设计制造安装和无损检验监督管理规定》(HAF601)的要求取得相应的制造、安装和无损检验许可证,并建立相关的管理制度。
4.2 从事核安全设备无损检验的人员应按照国家环境保护总局令第44号《民用核安全设备无损检验人员资格管理规定》 (HAF 602)的要求取得相应资格。
4.3 从事核安全设备焊接的焊工及焊接操作工(以下简称“焊工”)应按照中华人民共和国经济贸易委员会主任令第13号《特种作业安全技术培训考核管理办法》取得特种作业操作证,并按照国家环境保护总局令第45号《民用核安全设备焊工焊接操作工资格管理规定》 (HAF 603)的要求取得相应资格。
4.4 电工、起重工、起重设备操作工、脚手架工等特种作业人员应按照中华人民共和国经济贸易委员会主任令第13号《特种作业安全技术培训考核管理办法》取得特种作业操作证。
4.5 理化检验人员应按国家相关规定取得相应资格。
4.6 其他作业人员,如:焊接热处理、焊材烘干等人员应经过专业培训和授权。
5 通用技术要求
5.1 总要求
5.1.1 当设计文件或厂家提供的技术文件对检查和安装有本规程以外的要求时,应按其要求执行。
5.1.2 本规程应与GB 50126配套使用。
5.1.3 施工应按设计文件执行,当需要变更时,应征得原设计单位同意。
5.1.4 施工应编制相关施工程序、质量控制文件。
5.1.5 设备附带的需现场组装的管道,应按制造厂的技术文件执行。
5.1.6 在设备附近的管道及其支架的安装过程中,不应将设备作为临时或永久支架。
5.1.7 与不锈钢工件接触的物品,应符合清洁度和防污染的要求;用于操作不锈钢的工具应专用。
5.1.8 应按相关要求进行成型工艺评定,并形成报告,报告内容应包括:成型的类型、工件材料的材质、规格:加工设备的名称、型号及编号、成型工艺(加热和热处理温度等),材料、试验项目、有效范围等。
5.2 施工材料的要求
5.2.1 所使用的材料(包括成品、半成品等,下同。)应有装箱清单、说明书、质量合格证书和性能检测报告等文件。
5.2.2 材料在中转和储存过程中应妥善保管,满足其清洁度要求。
5.2.3 材料入场时,应按技术规格书的要求进行检查验收;检验内容应至少包括:质量证明文件、批次、包装、标识、尺寸数量和外观状况等,并按每个批次进行验收;验收结果应经建设单位或其授权单位和施工单位认可,并应形成相应的验收记录。
5.2.4 材料的标识应满足以下要求:
a) 应采用油漆、记号笔、挂牌、钢印等方式进行材料的标识,详见9 7:
b) 标识应清晰、不易被擦掉,尽可能使用实体标识,余料应做原标识移植;
2
NB/T 20216—2013
c) 材料在使用过程中其实体标识应与图纸、质量跟踪文件等保持一致。
5.3 切割下料
5.3.1 根据图纸选择经验收合格的材料,并应核实材料实体的物项编码材料选择过程中应能个重点、材料规格、材质和标识等与图纸一致。
5.3.2 对不锈钢材料加工过程中应采取防污染措施。
5.3.3 对于需进行热处理的奥氏体不锈钢和镍基合金材料工件,标识物不得污染工件表面;且在进行热处理后,标识应清晰。
5.3.4 工件应端头平整,无裂纹、重皮、毛刺、凸凹、缩口、熔渣、氧化物、铁屑等缺陷。
5.3.5应根据部件规格和焊接工艺要求选择机加工、磨削或热切割的方法制备焊接端头。用热切割或剪切方法加工时,则应通过机加工、磨削方法去除热影响区或硬化区。
5.4 焊工
应按照《民用核安全设备焊工焊接操作工资格管理规定》(HAF 603)进行焊工的资格管理。
5.5 焊接填充材料
5.5.1 药皮焊条、药芯焊丝的有效使用期为自本批次药皮焊条、药芯焊丝的验收试验报告批准之日起,有效期为5年或产品说明书规定。在使用期限到期前,如使用同批次焊材施焊的产品见证件的试验结果合格,则从该产品见证件报告批准之日起,可将该批次焊材的使用期延期5年,且应发布相应的焊材延期报告。实芯焊丝的有效期不受限制。
5.5.2 焊材贮存室和烘干室应配有经标定合格,且在有效期内的温度计和湿度计,贮存室的温度不得低于10℃,相对湿度不能高于60%(除非材料供应商另有规定)。焊材存放在贮存室或烘干室内时,应以原包装形式放置在货架上,货架离墙和地面的距离应大于300mm。不同批次的焊材之间应用隔板隔开或留有足够的分离间隔。
5.5.3 施工单位应编制焊材烘干指示书,其内容应包括:烘干温度、烘干时间和允许次数、保温温度和时间、允许暴露在空气中最长时间等。
5.5.4 通常烘干箱和保温箱在同一时间内只允许放入一种牌号的焊材。但当满足下述条件时,可在同一烘干箱内放入几种不同牌号的焊材:
a) 烘干条件完全相同;
b) 在不同牌号的焊材之间有实体间隔。
5.5.5 用于焊材评定的焊材只允许烘干一次。
5.6 焊接相关要求
5.6.1 车间评定按NB/T 20002.5相关要求执行。
5.6.2 焊接相关设备的仪表应经校验合格,校验周期不得超过6个月。
5.6.3 定位焊应使用与产品焊接时相同焊接工艺(如,填充材料,预热等)。
5.6.4 引弧应在焊缝坡口上进行,如坡口外有弧伤,应将其去除,并进行液体渗透或磁粉检验,弧伤部位应无裂纹。
5.6.5 焊接填充材料的验收/评定、焊接工艺评定、产品见证件、焊接数据包应按照NB/T20002的相关要求进行,设计文件、合同另有规定除外。
5.7 焊接接头热处理
5.7.1 按照NB/T 20002.6及设计文件的规定进行热处理。
3
NB/T 20216----2013
5.7.2 后热处理的温度应等于或高于预热温度,后热处理应连续进行。若工件焊接后在冷却到室温前立即进行消除应力热处理时,可取消后热处理。
5.7.3 热处理报告应包含消除应力热处理的温度记录曲线。
6 管道支架预制
6.1 支架部件的成形
应符合以下要求:
a) 热成形宜采用炉内加热,加热炉应配置温度记录装置。禁止使用丙烷火焰直接加热。
b) 成形过程中工件表面应进行润滑,避免工件表面刮伤。
6.2 支架组装
支架组装时应对组装后的支架进行标识,标识内容应能使实物与图纸及质量文件一致保持其可追溯性。
6.3 架焊接
应符合以下要求:
a) 为便于表面处理及满足碳钢和不锈钢部件各自的贮存要求,对碳钢支架上的不锈钢部件,宜在现场安装时焊接。
b) 工件材料厚度小于或等于3mm宜使用熔化极活性气体保护电弧焊(MAG)焊接方法:厚度大于3mm的宜使用MAG焊接方法进行根部焊接,有活性气体保护的药芯焊丝电弧焊(FCAW)方法进行填充和封面焊接。
附录A为推荐的支架焊缝类型。
6.4 支架检查、检验
应符合以下要求:
a) 根据图纸及设计标准对预制完成的支架尺寸、形状、标识及焊缝外观进行检查。
b) 对于支撑1级辅助管道的支架焊缝液体渗透或磁粉检验抽检比例为10%.
6.5 表面处理
应符合以下要求:
a) 与高温管道直接焊接或贴附的支架部件,其涂层系统应与管道相同。现场安装后不与外界接触的支架的内表面不需要进行涂装。
b) 工件的表面处理应符合7.6中的相关规定。
6.6 贮存
经表面处理后的管道支架及其附件的贮存应符合7.7中的相关规定。
7 管道预制
7.1 管道分级
管道分为1级、2级、3级和非核级(NC)四个等级。
4
NB/T 20216—2013
7.2 管道部件的加工
应符合以下要求:
a) 应按照焊接工艺和技术要求加工管道及其部件焊接端头。
b) 其它要求同5.3.
7.3 管道的组对
应符合以下要求:
a) 按照等轴图进行管道及其部件的组对。
b) 组对、装配偏差要求,见附录B.
c) 焊接接头类型,见附录C.
d) 错边量要求见9.4.4~9.4.6.
7.4 管道焊接
7.4.1 产品焊接应符合以下要求:
a) 管道焊接位置见 HAF 603附件1中的“1.5焊接位置”;
b) 产品焊接按照NB/T20002.6的规定执行:
c) 产品焊接时,应选择与焊接工艺评定同技术要求的焊材;
d) 施焊位置环境温度应不低于10℃,焊件温度应不低于5℃。坡口表面保持干燥,不得在潮湿面上施焊。
e) 气体保护焊时,工作区域应采取防护措施,防止对流风对电弧稳定的影响。
7.4.2 不应下列情况出现:
a) 主焊缝十字交叉:
b) 两纵向焊缝间距小于工件壁厚的2倍或40mm中的较小者:
c) 主焊缝边缘与开孔、主焊缝边缘与其它焊缝边缘之间的距离小于装配件壁厚的2倍或40mm中的较小者:
d) 管道插套焊:在组装时管端与插套底部的最小间隙<1.5mm.
7.4.3 管道弯制应符合以下要求:
a) 管道弯制应符合技术文件要求。冷弯采用机械方法,热弯宜采用感应加热弯制方法,焊接管弯制时纵焊缝位置应避开受拉(压)区。
b) 如需要,可在管子弯曲部位涂润滑油,对于奥氏体不锈钢应使用易于清除、对管子无污染的物品。
c) 管子弯曲前后表面不得有裂纹、气孔、重皮、毛刺或其它有害缺陷。
d) 弯曲完成后应检查弯管的几何尺寸、椭圆度、减薄量等,并形成检查记录。
e) 成型后管件的公差按NB/T 20001 相关要求执行。
7.5 检查和检验
7.5.1 检查和检验应符合设计及相关文件要求。
7.5.2 外观检查至少应包括:
a) 标识:
b) 组对及焊缝坡口:
c) 焊缝外观和尺寸:
d) 法兰垂直度:
5
NB/T 20216---2013
e) 管道符合性等。
7.5.3 无损检验应满足以下要求:
a) 施工单位应根据设计及相关文件等要求编制无损检验大纲,内容应包括检验的范围、比例、时机、方法等。
b) 无损检验评定标准按照NB/T 20003要求执行。
c) 若设计及相关文件对射线检验比例无要求时,每种焊接工艺,每个焊工完成的管道焊缝宣按以下要求执行:
1) 1级、2级管道的对接焊缝: 100%检验。
2) 3级管道的对接焊缝:抽样比例10%:
(1)对于自动焊,检验中发现有超过验收准则的缺陷,则应对该批焊缝进行100%的检验;
(2)对于手工焊,如发现一个不合格缺陷时,需对同一批的其他两条焊缝进行检验,如在这两条焊缝中发现一个及以上的不合格缺陷,则应对该批焊缝进行100%的检验:
(3)焊缝交叉点应进行100%的射线检验,但如满足表1所列条件之一的焊缝,则不要求对焊缝的交叉点进行100%的射线检验。
3) 非核级管道的对接焊缝:抽样比例5%;其他要求与上条2)相同。
4) 插套焊缝:
(1)1级管道的插套焊缝为100%检验。
(2)2级、3级和NC级管道的插套可分在同一组,抽样比例为3%;抽样检查的焊缝应进行100%检验,如发现超标缺陷则应对另外两条焊缝进行100%的检验,如在这两条焊缝的任一条中有超标缺陷,则应在该批焊缝中再取4条焊缝进行100%射线检验,如在这四条焊缝的任一条中有超标缺陷,则应对该批所有焊缝进行100%射线检验。
表1 焊缝交叉点不要求100%射线检验的条件
输送的流体 条 件
最高工作温度(℃) 最大工作压力(Mpa) 内径(mm)
热水、蒸汽 ≤120 ≤3 ≤110
液体,具有危害生理作用的化学或放射性物质 ≤120 ≤3 ≤80
7.6 表面处理
7.6.1 预制成品、半成品和零部件的表面处理应按7.6.2和7.6.3的要求进行,设计技术文件另有约定除外。
7.6.2 对于不锈钢部件,如发现表面污染,应进行表面处理。处理后如需进行酸洗、钝化,应符合以下要求:
a) 预制完成的不锈钢管道应进行酸洗、钝化; 工件表面应清洁,满足清洁度等级要求。
b) 应用丙酮或乙醇及经证明对除油工件表面无害的其他溶剂进行表面油污(油、油脂、切削液等)清除。
c) 允许使用尼龙刷或者不锈钢丝刷刷洗以提高酸洗效果。
d) 酸洗操作结束后,立即用除盐水冲洗不锈钢部件,冲洗后水的PH值应为6~8之间。
e) 酸液和除盐水应定期进行测量分析。
7.6.3 涂层应符合以下要求:
6
NB/T 20216-2013
a) 根据图纸设计信息(厂房、系统、系统温度等)和设计文件的规定确定涂料的种类、颜色,涂敷的层数等。
b) 涂层应在涂漆工件表面清洁后的8小时内进行。
c) 环境温度应在5℃~30℃之间,工件温度应高于露点温度3℃以上,相对湿度≤85%。若设计和供货商另有规定时,按其要求执行。
d) 对机加工表面、法兰密封面等不需要涂漆的表面应进行临时保护。
e) 漆膜应附着牢固,无剥落、皱纹、针孔。
f) 气泡缺陷每平方米直径不应大于2mm,每平方米的气泡不超过50个等缺陷,并按照GB/T 13452.2的规定进行检查。
g) 附着力测试应按下进行:
1) 每1000平方米检测一次:当实施困难时,可在见证板或试件上进行;
2) 当涂层面积不易计算时,每两周检测一次。
7.7 贮存
预制成品应分类、分区贮存:
a) 不锈钢部件室内贮存,使用木料作为支撑物或垫层,避免与铁素体及其它可污染物接触。
b) 碳钢部件室外贮存,但应有支撑物或垫层,贮存场地应避免积水。
c) 在贮存期间,管口及其它开孔的封堵应保持完好。
7.8 完工图
预制完工后,应编制预制完工状态图。
8 支架安装
8.1 支架的安装偏差要求
8.1.1 靠近设备的第一个支架的允许偏差应符合以下要求:
a)对于管道直径 DN ≥ 100:±20mm.
b) 对于管道直径 DN <100:±10mm.
8.1.2 一般支架位置允许偏差:相对于基准点或参考点允许偏差见图1 和表2.
支架理论位置尺寸
PE
A
A
图中:
PE——基准点或参考点:
A————位置偏差。
图1 相对于基准点或参考点允许偏差
7
NB/T 20216—2013
表2 一般支架位置允许偏差(A)
单位:mm
管线级别 直径
DN≤ 50 50< DN ≤ 150 150< DN ≤300 DN >300
1.2.3 级 50 100 150 200
非核 级 (NC) 100 150 200 250
8.1.3给水流量调节系统和主蒸汽系统管线的支架位置允许偏差应符合以下要求:
a) 支架位置允许偏差A,见图2:
1)对于DN>50 管线与1级支架(所有管径)±50mm;
2)对于DN ≤ 50 管线支架± 100mm.
b) 位置允许偏差B(单位mm),见图2和表3.
PE: 基准点或参考点
支架1
支架2
PE
mathbf{L pm A}
L±B
图2 给水流量调节系统和主蒸汽系统管线的支架位置允许偏差
NB/T 20216—2013
表3 给水流量调节系统和主蒸汽系统管线的支架位置允许偏差(B)
单位mm
管道直径DN 不保温管道 保温管道
弹簧箱支架 其他支架 弹簧箱支架 其他支架
8 50 33 15 11
15 65 40 30 19
25 80 50 45 30
50 105 65 75 45
80 120 75 80 50
100 125 80 95 60
150 140 90 115 75
200 155 95 115 75
250 165 105 150 95
300 175 110 160 100
350 175 110 160 100
400 185 115 175 110
500和550 205 130 175 110
600和700 215 135 175 110
800 215 135 175 110
8.1.4 耐磨垫处的支架定位及允许偏差,见图3,对于纵向导向、滑动功能的支架,允许偏差B为:≤ 20% A.
支架理论中心线
垫板的中心线
!B
耐磨垫
A
支 架
图3 耐磨垫处的支架定位及允许偏差
8.2支架基板及锚固螺栓的安装
8.2.1 支架基板上钻孔位置的允许偏差按设计文件执行。
8.2.2 膨胀螺栓的定位原则,膨胀螺栓的安装,有下列三种情况:
9
NB/T 20216——2013
a) 当基板的整个表面位于混凝土上,图纸中未说明支架之间、支架与部件之间或支架与混凝土边缘之间的距离,间距满足下述条件,见图4,在设计位置处且在允许偏差范围内安装的支架。
b) 在图纸上标注了支架离土建参考点的距离,但未规定最小值(即在混凝土梁上的基板),膨胀螺栓位置的允许偏差为±40mm。见图5.
c) 在图纸或相关文件中规定了最小间距,在这种情况下,钻孔时必须满足这一最小间距。
钻孔轴线
禁止钻孔区
钻孔轴线
禁止钻孔区域
R=15D
R=10D
混凝土边缘
R-15Q
混凝土边缘
a)膨胀螺栓位于混凝土一边情况
b)膨胀螺栓位于混凝土一角情况
说明:
D———膨胀螺栓外径:
R——最小距离。
图4 膨胀螺栓距混凝土--边和距混凝土一角情况
混凝土梁
基板
X pm 4 0 m m
膨胀螺栓的钻孔轴线
说明:
X———膨胀螺栓与混凝土梁边缘的理论值。
图5 位于混凝土梁上的基板
8.2.3 在混凝土上钻膨胀螺栓孔的要求及允许偏差应符合以下规定:
a) 膨胀螺栓的孔洞应避开钢筋。
b) 钻孔过程中如果碰到钢筋,应停止钻孔,并选择新的钻孔位置,两孔边缘的距离至少25mm,废孔应用配制好的特殊水泥砂浆堵死。
10
NB/T 20216——2013
c) 孔径允许偏差A^{ * 0 . 0 1}^{ * 1}.
d) 孔的垂直度允许偏差±5°.
8.2.4 膨胀螺栓的安装要求应符合以下规定:
a) 膨胀螺栓在混凝土中的长度应大于等于产品的技术要求的长度。
b) 膨胀螺栓外露长度要求,对于所有类型的膨胀螺栓,穿过镁紧螺母的螺栓外露长度“Z”至少为2道可见螺纹(目检),见图6.
混凝土
螺母
锁紧锁母
膨胀螺栓。
基板
Zmin.
图6 膨胀螺栓外露长度要求
8.3 支架构件的安装
8.3.1 直径大于DN50管线的支架梁的定位允许偏差
8.3.1.1 基板为预埋板时支架梁的定位允许偏差应符合以下要求:
a) 总允许偏差要求,对下列情况,支架梁中心与预埋板轴线的允许偏差为±40mm;
1) 1级支架。
2) 主蒸汽系统和给水流量调节系统管线支架。
3) 阻尼器、拉杆或它们的延伸梁。
b) 对300mm×600mm和600mm×600mm预埋板允许的适应性调整,此适应性调整不适用于上述“a)总允许偏差要求”的情况:此类预埋板板允许的适应性调整有下列两种情况:
1) 由≤100的单槽钢组成的支架梁,支架梁应位于阴影区内,见图7.
75
75
8
员
田
75
75
图7 情况1
11
NB/T 20216—2013
2) 由“H 型钢HEB100、HEB140和HEB200”, “双槽钢 UAP100”,“单或双槽钢 UAP150和UAP200”等型钢组成的支架梁,仅在一个方向上可以移出“本条列项a)总允许偏差要求”范围(±40mm)之外:同时,应满足下述要求:
(1)支架梁应安装在上述情况1规定的阴影区内:
(2)在其相反方向增加一个加强梁,见图8和本条列项c):
(3)加强梁移动的位置,见本条列项c):
(4) 限制情况:此调整不能应用到8.3.1.1 a).
75
75
梁中心线
LD
加强梁
梁中心线
加强梁。
E
40
40
40mm
40mm
a) 预埋板300×600
b)预埋板600×600
图8 情况2
c) 加强梁,型钢加强梁的最大长度为250mm;板式加强梁为10mm厚,其直角边长为200mm的等腰三角形:加强梁应在图13所示的阴影区内,超出阴影区的部分应切除。
1)情况1: 支架梁为H 型钢 HEB 100和HEB 200,双槽钢 UAP 100和UAP 200时,加强梁为单槽钢情况,见图9.
2) 情况2: 支架梁为H 型钢 HEB 140时,加强梁也为H型钢(HEB)情况,见图10.
3)情况 3: 支架梁为单槽钢 UAP 150,UAP 200 和双槽钢 UAP 150, 加强梁为单槽钢或支撑板时的情况,见图11.
熔透焊
单面角焊
单面角焊
熔透焊
A
A
A-A
图9 加强梁情况1
12
NB/T 20216—2013
溶通焊
单面角焊
单面角焊
熔通焊
N
20mm
如需要,按图,两
A.
-
A
影响分,可以切割
A-A
图10 加强梁情况2
解透焊
单面角焊
单面角焊
熔透焊
A
A
^^
熔透焊
双面角焊或全焊透
A
A
4 5 ^{circ}
A-A
图11 加强梁情况3
8.3.1.2基板为膨胀螺栓固定时,支架梁的定位允许偏差应符合以下要求:
a) 对于1级支架和主蒸汽系统和给水流量调节系统管线支架以及不在NE、NF标准基板上的其它支架,其支架梁相对于垂直和横向两理论中心线的允许偏差均为±10mm,见图12.
b) 对于2级支架且基板为NE、NF板时,支架梁的位置允许偏差见图13和表4.
c) 对于 NC级支架,且当基板为NE、NF时,支架的位置允许偏差如下:
1) NE1 型基板,支架梁相对于垂直于基板长度方向中心线的允许偏差为±40mm,垂直于基板宽度方向中心线的允许偏差为±25mm.
2) NF1 型基板,支架梁相对于基板纵向和横向中心线的允许偏差均为±40mm.
3) NE2、NE3 和 NE4 型基板,支架梁相对于基板纵向和横向中心线的允许偏差均为±50mm;但支架梁距基板边缘的距离不应小于 15 mm.
4) NF2、NF3 和 NF4 型基板,支架梁相对于基板纵向和横向理论中心线的允许偏差均为±50mm.
13
NB/T 20216---2013
d) 以上所列允许偏差是指支架梁从支架原始设计位置起的最大允许位移,但应对支架的安装及螺栓的拧紧没有影响。
支架梁中心线
2
2
10
10
允许偏差 mm
图12 支架梁相对于垂直和横向两理论中心线的允许偏差
允许偏差±A
允许偏差±A
图13 支架梁的位置允许偏差
表4 支架梁的位置允许偏差
板类型 允许偏差“A”(mm)
NE1/NF1 15
NE2/NF2 20
NE3/NF3 25
NE4/NF4 30
8.3.2 其他要求
其他要求如下:
a) 与螺栓头部接触的零件表面应垂直于螺栓轴线,其相对螺栓轴线的斜度应不大于5%.