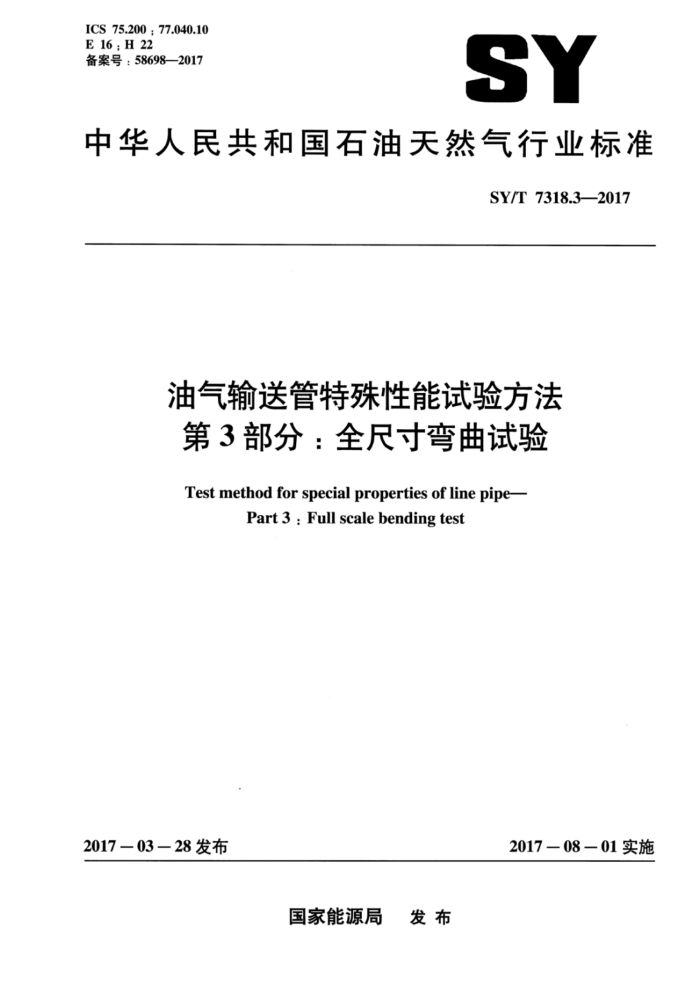
ICS 75.200; 77.040.10 E16:H22 备案号:58698—2017
SY
中华人民共和国石油天然气行业标准
SY/T7318.32017
油气输送管特殊性能试验方法第3部分:全尺寸弯曲试验 Test method for special properties of line pipe-
Part 3 : Full scale bending test
2017—03—28发布
2017-08-01实施
国家能源局 发布
SY/T7318.3—2017
目 次
前言 1 范围 2 规范性引用文件 3 术语和定义
-
符号和代号试验钢管 5.1 试验钢管规格 5.2 试验钢管加工试验装置 6.1 一般要求 6.2 加载系统 6.3 测量装置试验方法 7.1 - 般要求 7.2 试验钢管准备 7.3 试验钢管测量 7.4 试验温度 7.5 试验钢管定位 7.6 试验流程数据处理及试验报告 8.1 数据处理 8.2 试验记录与试验报告附录A(资料性附录)试验结果
4
5
6
N
SY/T7318.3—2017
前言
SY/T7318《油气输送管特殊性能试验方法》分为以下几部分:
第1部分:宽板拉伸试验第2部分:单边缺口拉伸试验第3部分:全尺寸弯曲试验
-
一第4部分:全尺寸气体爆破试验; . 本部分为SY/T7318的第3部分。 本部分按照GB/T1.1一2009《标准化工作导则第1部分:标准的结构和编写》给出的规则起草。 请注意本文件的某些内容可能涉及专利。本文件的发布机构不承担识别这些专利的责任。 本部分由石油管材专业标准化技术委员会提出并归口。 本部分起草单位:中国石油集团石油管工程技术研究院、石油管材及装备材料服役行为与结构安
全国家重点实验室、北京隆盛泰科石油管科技有限公司、西安三环科技开发总公司。
本部分主要起草人:陈宏远、王鹏、池强、李炎华、杨坤、张继明、吉玲康、李鹤、张伟卫、徐婷、杨专钊、姚欢。
II
SY/T7318.3—2017
油气输送管特殊性能试验方法第3部分:全尺寸弯曲试验
1范围
SY/T7318的本部分规定了油气输送用管线钢管全尺寸弯曲试验的试验钢管形状及尺寸、试验装置、试验方法及数据处理等。
本部分适用于采用力臂加载方法测量钢管(包括带环焊缝钢管)在静态单调加载条件下的弯曲行为。其他类似钢结构在准静态加载下的整体弯曲试验,也可参照本部分。
2规范性引用文件
下列文件对于本文件的应用是必不可少的。凡是注日期的引用文件,仅注日期的版本适用于本文件。凡是不注日期的引用文件,其最新版本(包括所有的修改单)适用于本文件。
GB/T132832008工业过程测量和控制用检测仪表和显示仪表精确度等级 GB/T13992—2010金属粘贴式电阻应变计 ASTME4测试仪力验正标准规程(Standardpracticesforforceverificationoftestingmachines) ASTME1237安装抗粘着应变仪指南(Standardguideforinstallingbondedresistancestraingages)
3术语和定义
下列术语和定义适用于本文件。
3.1
试验钢管samplepipe 用于全尺寸弯曲试验的油气输送用钢管。
3.2
屈曲buckling 试验钢管变形抗力开始下降时的变形行为。
4符号和代号
下列符号和代号适用于本文件。 D一试验钢管外径,单位为毫米(mm); E—弹性模量,单位为兆帕(MPa); K—系数,取值为0.99; M弯矩,单位为牛米(N·m);
试验钢管公称壁厚,单位为毫米(mm);
1
SY/T 7318.3—2017
V- 一泊松比,取值为0.3。
5试验钢管 5.1试验钢管规格 5.1.1根据设备的实验能力,试验钢管长度大于6倍外径。 5.1.2 2试验钢管最大壁厚的推荐值可根据其直径,结合试验装置的最大载荷能力,由公式(1)进行计算:
2M(1-v) EKD
(1)
5.1.3 3试验钢管的最大壁厚也可根据其直径,结合试验装置的最大载荷能力,由数值仿真计算获得。 5.2试验钢管加工 5.2.1 1试验准备前应清理试验钢管内外表面,确保试验钢管内部无任何残留物。 5.2.2 试验钢管两端宜用机械方式加工坡口,并与堵头以焊接方式连接。 5.2.3 试验钢管表面不应有非设计性的缺陷。
6试验装置
6.1一般要求 6.1.1 1试验装置应包括加载系统、测量装置和附件等。 6.1.2 2试验装置应至少满足以下参数可以在试验过程中持续测量:
施加载荷。 载荷方向上的位移。 试验钢管特定位置上的应变。
6.1.3载荷应根据ASTME4的规定校准。 6.2加载系统
加载系统的主要作用是施加内压和弯曲载荷,主要组成包括载荷施加装置、加载力臂、内压装置。图1所示为一种典型加载系统的结构原理图。
试验钢管
力臂
位移控制载荷。
图1一种典型加载系统的结构原理图
2
SY/T7318.3—2017
6.3 测量装置 6.3.1 应变测量装置 6.3.1.1 在试验过程中,可对管体表面的应变进行测量。 6.3.1.2 应变仪分辨率应优于0.1μs,采集频率大于10Hz,测量范围大于50000μe。 6.3.1.3 应变片应符合GB/T13992—2010A级应变片的要求。 6.3.1.4 应变片的粘贴符合ASTME1237的要求。 6.3.2 载荷测量装置 6.3.2.1 试验过程中,应对水压系统进行压力实时测量。 6.3.2.2 试验过程中,应对弯矩载荷进行实时测量,也可通过油缸压力推算获得载荷。 6.3.2.3 压力测量装置的精度要求为:压力传感器精度应不小于GB/T132832008规定的1.0级精度。 6.3.31 位移测量装置 6.3.3.1 试验过程中,应对载荷施加点的位移实时测量。 6.3.3.2 试验过程中,可对管体进行弯曲角度的实时测量。 6.3.3.3 位移传感器最大误差应不大于1mm。
7试验方法 7.1一般要求 7.1.1全尺寸弯曲试验宜采用位移控制载荷加载。 7.1.2全尺寸弯曲试验可采用连续进行的方式或步长进行的试验模式。 7.1.3试验过程中,应采集载荷、位移、应变等数据。 7.1.4可使用测量获得的载荷一位移曲线的载荷最高点作为试验钢管届曲判据。 7.1.5可使用加载过程中载荷最高点对应时刻的应变测量结果作为试验钢管屈曲应变。 7.2试验钢管准备 7.2.1J 应根据试验钢管外径连接相应规格的堵头,堵头端面、力臂应与试验钢管轴线垂直。 7.2.2 对于直缝焊管,如无特殊要求,宜保证试验钢管的直焊缝位于弯曲变形中承受尽可能小应变的位置。 7.2.3 试验钢管采用焊接方式连接时,所用焊材及焊接工艺应保证环焊接头强匹配于钢管管体。 7.3试验钢管测量 7.3.12 在试验之前,可完成以下数据的测量: 7.3.2试验钢管管体外表面的空间坐标。 7.3.3试验钢管管体对应7.3.2中测量点位置的壁厚。 7.4试验温度 7.4.1试验过程中的环境温度变化宜不超过20℃,且应保证不低于管体及焊缝韧脆转变曲线的上平台温度。
3
SY/T7318.3—2017
7.4.2在试验过程中,试验钢管温度应保证稳定、均匀,变化应不超过土5℃。 7.5试验钢管定位 7.5.1试验钢管轴线应平行于试验装置的加载方向,并且与两侧力臂垂直。 7.5.2试验钢管应沿试验机的载荷轴线对中,以避免产生剪切和弯曲载荷。 7.6试验流程 7.6.1i 试验管加压 7.6.1.1试验钢管可施加至所需压力,如果需要采集加压过程中试验钢管的应变数据,可按1MPa的间隔进行升压操作,并在每增加1MPa后进行数据采集,直至所需的试验压力。 7.6.1.2试验钢管内压加压完成后,启动加载系统。 7.6.2加载 7.6.2.1 试验载荷可连续施加或分步长施加,试验加载速率应小于2mm/s。 7.6.2.2 载荷达到最大值后,如无特殊要求,下降至最大载荷90%时,可结束试验。 7.6.3测量 7.6.3.1 施加载荷之前,宜将位移、角度、应变等测量装置的读数置零。 7.6.3.2在连续施加载荷的模式下,数据测量也应按一定频率连续进行。 7.6.3.3分步长施加载荷的模式下,每步加载后应进行一次数据采集,记录载荷、位移、应变等数据,其中载荷数据应记录该步长加载过程中的最大载荷。 7.6.3.4试验结束后,可进行试验钢管外形、应变等数据的测量。
8数据处理及试验报告 8.1 数据处理 8.1.1 载荷位移曲线
载荷位移曲线为试验过程中施加的载荷值与特定位置(力臂或钢管末端)位移之间的关系。 8.1.2临界屈曲应变
可按图2定义临界屈曲应变,即达到最大载荷时,试验钢管弯曲内弧面上最大应变位置2倍外径长度范围内的压缩应变平均值。
2D
图22D长度平均应变示意图
4
SY/T7318.3—2017
8.2试验记录与试验报告 8.2.1 试验记录
试验记录可包含试验前和试验过程中的所有测试数据,试验数据记录参照附录A的规定填写。
8.2.2 试验报告
试验报告至少应包含(但不限于)以下内容: a)加载方式。 b)试验钢管信息(包括规格、钢级、管号等)。 c)试验钢管外形测量基本信息。 d)最大载荷(扭矩或力)。 e)载荷一位移曲线。 f)临界屈曲应变。 g)屈曲位置压缩应变。 表1为试验报告范例。
表1试验报告内容范例
试验钢管编号:原始测量结果: k
尺寸规格:测试参数:试验压力:
钢级:
长(mm)最大壁厚(mm)最小壁厚(mm)平均厚度(mm)厚度标准偏差(mm)
平均中部压缩应变计算参数:旋角测试结果:应变测试结果:
最大外径(mm)最小外径(mm)平均外径(mm)外径标准偏差(mm)
屈曲位置压缩应变计算参数:转角测试结果:应变测试结果:
弯曲测试结果:
最大椭圆度(%) 最小椭圆度(%) 平均椭圆度(%)
所在位置所在位置
最大加载扭矩(或推力):相关应变值:
kN·m(或kN)
中部平均压缩应变:一 _% 屈曲位置压缩应变: _%
5
ICS 75.200; 77.040.10 E16:H22 备案号:58698—2017
SY
中华人民共和国石油天然气行业标准
SY/T7318.32017
油气输送管特殊性能试验方法第3部分:全尺寸弯曲试验 Test method for special properties of line pipe-
Part 3 : Full scale bending test
2017—03—28发布
2017-08-01实施
国家能源局 发布
SY/T7318.3—2017
目 次
前言 1 范围 2 规范性引用文件 3 术语和定义
-
符号和代号试验钢管 5.1 试验钢管规格 5.2 试验钢管加工试验装置 6.1 一般要求 6.2 加载系统 6.3 测量装置试验方法 7.1 - 般要求 7.2 试验钢管准备 7.3 试验钢管测量 7.4 试验温度 7.5 试验钢管定位 7.6 试验流程数据处理及试验报告 8.1 数据处理 8.2 试验记录与试验报告附录A(资料性附录)试验结果
4
5
6
N
SY/T7318.3—2017
前言
SY/T7318《油气输送管特殊性能试验方法》分为以下几部分:
第1部分:宽板拉伸试验第2部分:单边缺口拉伸试验第3部分:全尺寸弯曲试验
-
一第4部分:全尺寸气体爆破试验; . 本部分为SY/T7318的第3部分。 本部分按照GB/T1.1一2009《标准化工作导则第1部分:标准的结构和编写》给出的规则起草。 请注意本文件的某些内容可能涉及专利。本文件的发布机构不承担识别这些专利的责任。 本部分由石油管材专业标准化技术委员会提出并归口。 本部分起草单位:中国石油集团石油管工程技术研究院、石油管材及装备材料服役行为与结构安
全国家重点实验室、北京隆盛泰科石油管科技有限公司、西安三环科技开发总公司。
本部分主要起草人:陈宏远、王鹏、池强、李炎华、杨坤、张继明、吉玲康、李鹤、张伟卫、徐婷、杨专钊、姚欢。
II
SY/T7318.3—2017
油气输送管特殊性能试验方法第3部分:全尺寸弯曲试验
1范围
SY/T7318的本部分规定了油气输送用管线钢管全尺寸弯曲试验的试验钢管形状及尺寸、试验装置、试验方法及数据处理等。
本部分适用于采用力臂加载方法测量钢管(包括带环焊缝钢管)在静态单调加载条件下的弯曲行为。其他类似钢结构在准静态加载下的整体弯曲试验,也可参照本部分。
2规范性引用文件
下列文件对于本文件的应用是必不可少的。凡是注日期的引用文件,仅注日期的版本适用于本文件。凡是不注日期的引用文件,其最新版本(包括所有的修改单)适用于本文件。
GB/T132832008工业过程测量和控制用检测仪表和显示仪表精确度等级 GB/T13992—2010金属粘贴式电阻应变计 ASTME4测试仪力验正标准规程(Standardpracticesforforceverificationoftestingmachines) ASTME1237安装抗粘着应变仪指南(Standardguideforinstallingbondedresistancestraingages)
3术语和定义
下列术语和定义适用于本文件。
3.1
试验钢管samplepipe 用于全尺寸弯曲试验的油气输送用钢管。
3.2
屈曲buckling 试验钢管变形抗力开始下降时的变形行为。
4符号和代号
下列符号和代号适用于本文件。 D一试验钢管外径,单位为毫米(mm); E—弹性模量,单位为兆帕(MPa); K—系数,取值为0.99; M弯矩,单位为牛米(N·m);
试验钢管公称壁厚,单位为毫米(mm);
1
SY/T 7318.3—2017
V- 一泊松比,取值为0.3。
5试验钢管 5.1试验钢管规格 5.1.1根据设备的实验能力,试验钢管长度大于6倍外径。 5.1.2 2试验钢管最大壁厚的推荐值可根据其直径,结合试验装置的最大载荷能力,由公式(1)进行计算:
2M(1-v) EKD
(1)
5.1.3 3试验钢管的最大壁厚也可根据其直径,结合试验装置的最大载荷能力,由数值仿真计算获得。 5.2试验钢管加工 5.2.1 1试验准备前应清理试验钢管内外表面,确保试验钢管内部无任何残留物。 5.2.2 试验钢管两端宜用机械方式加工坡口,并与堵头以焊接方式连接。 5.2.3 试验钢管表面不应有非设计性的缺陷。
6试验装置
6.1一般要求 6.1.1 1试验装置应包括加载系统、测量装置和附件等。 6.1.2 2试验装置应至少满足以下参数可以在试验过程中持续测量:
施加载荷。 载荷方向上的位移。 试验钢管特定位置上的应变。
6.1.3载荷应根据ASTME4的规定校准。 6.2加载系统
加载系统的主要作用是施加内压和弯曲载荷,主要组成包括载荷施加装置、加载力臂、内压装置。图1所示为一种典型加载系统的结构原理图。
试验钢管
力臂
位移控制载荷。
图1一种典型加载系统的结构原理图
2
SY/T7318.3—2017
6.3 测量装置 6.3.1 应变测量装置 6.3.1.1 在试验过程中,可对管体表面的应变进行测量。 6.3.1.2 应变仪分辨率应优于0.1μs,采集频率大于10Hz,测量范围大于50000μe。 6.3.1.3 应变片应符合GB/T13992—2010A级应变片的要求。 6.3.1.4 应变片的粘贴符合ASTME1237的要求。 6.3.2 载荷测量装置 6.3.2.1 试验过程中,应对水压系统进行压力实时测量。 6.3.2.2 试验过程中,应对弯矩载荷进行实时测量,也可通过油缸压力推算获得载荷。 6.3.2.3 压力测量装置的精度要求为:压力传感器精度应不小于GB/T132832008规定的1.0级精度。 6.3.31 位移测量装置 6.3.3.1 试验过程中,应对载荷施加点的位移实时测量。 6.3.3.2 试验过程中,可对管体进行弯曲角度的实时测量。 6.3.3.3 位移传感器最大误差应不大于1mm。
7试验方法 7.1一般要求 7.1.1全尺寸弯曲试验宜采用位移控制载荷加载。 7.1.2全尺寸弯曲试验可采用连续进行的方式或步长进行的试验模式。 7.1.3试验过程中,应采集载荷、位移、应变等数据。 7.1.4可使用测量获得的载荷一位移曲线的载荷最高点作为试验钢管届曲判据。 7.1.5可使用加载过程中载荷最高点对应时刻的应变测量结果作为试验钢管屈曲应变。 7.2试验钢管准备 7.2.1J 应根据试验钢管外径连接相应规格的堵头,堵头端面、力臂应与试验钢管轴线垂直。 7.2.2 对于直缝焊管,如无特殊要求,宜保证试验钢管的直焊缝位于弯曲变形中承受尽可能小应变的位置。 7.2.3 试验钢管采用焊接方式连接时,所用焊材及焊接工艺应保证环焊接头强匹配于钢管管体。 7.3试验钢管测量 7.3.12 在试验之前,可完成以下数据的测量: 7.3.2试验钢管管体外表面的空间坐标。 7.3.3试验钢管管体对应7.3.2中测量点位置的壁厚。 7.4试验温度 7.4.1试验过程中的环境温度变化宜不超过20℃,且应保证不低于管体及焊缝韧脆转变曲线的上平台温度。
3
SY/T7318.3—2017
7.4.2在试验过程中,试验钢管温度应保证稳定、均匀,变化应不超过土5℃。 7.5试验钢管定位 7.5.1试验钢管轴线应平行于试验装置的加载方向,并且与两侧力臂垂直。 7.5.2试验钢管应沿试验机的载荷轴线对中,以避免产生剪切和弯曲载荷。 7.6试验流程 7.6.1i 试验管加压 7.6.1.1试验钢管可施加至所需压力,如果需要采集加压过程中试验钢管的应变数据,可按1MPa的间隔进行升压操作,并在每增加1MPa后进行数据采集,直至所需的试验压力。 7.6.1.2试验钢管内压加压完成后,启动加载系统。 7.6.2加载 7.6.2.1 试验载荷可连续施加或分步长施加,试验加载速率应小于2mm/s。 7.6.2.2 载荷达到最大值后,如无特殊要求,下降至最大载荷90%时,可结束试验。 7.6.3测量 7.6.3.1 施加载荷之前,宜将位移、角度、应变等测量装置的读数置零。 7.6.3.2在连续施加载荷的模式下,数据测量也应按一定频率连续进行。 7.6.3.3分步长施加载荷的模式下,每步加载后应进行一次数据采集,记录载荷、位移、应变等数据,其中载荷数据应记录该步长加载过程中的最大载荷。 7.6.3.4试验结束后,可进行试验钢管外形、应变等数据的测量。
8数据处理及试验报告 8.1 数据处理 8.1.1 载荷位移曲线
载荷位移曲线为试验过程中施加的载荷值与特定位置(力臂或钢管末端)位移之间的关系。 8.1.2临界屈曲应变
可按图2定义临界屈曲应变,即达到最大载荷时,试验钢管弯曲内弧面上最大应变位置2倍外径长度范围内的压缩应变平均值。
2D
图22D长度平均应变示意图
4
SY/T7318.3—2017
8.2试验记录与试验报告 8.2.1 试验记录
试验记录可包含试验前和试验过程中的所有测试数据,试验数据记录参照附录A的规定填写。
8.2.2 试验报告
试验报告至少应包含(但不限于)以下内容: a)加载方式。 b)试验钢管信息(包括规格、钢级、管号等)。 c)试验钢管外形测量基本信息。 d)最大载荷(扭矩或力)。 e)载荷一位移曲线。 f)临界屈曲应变。 g)屈曲位置压缩应变。 表1为试验报告范例。
表1试验报告内容范例
试验钢管编号:原始测量结果: k
尺寸规格:测试参数:试验压力:
钢级:
长(mm)最大壁厚(mm)最小壁厚(mm)平均厚度(mm)厚度标准偏差(mm)
平均中部压缩应变计算参数:旋角测试结果:应变测试结果:
最大外径(mm)最小外径(mm)平均外径(mm)外径标准偏差(mm)
屈曲位置压缩应变计算参数:转角测试结果:应变测试结果:
弯曲测试结果:
最大椭圆度(%) 最小椭圆度(%) 平均椭圆度(%)
所在位置所在位置
最大加载扭矩(或推力):相关应变值:
kN·m(或kN)
中部平均压缩应变:一 _% 屈曲位置压缩应变: _%
5