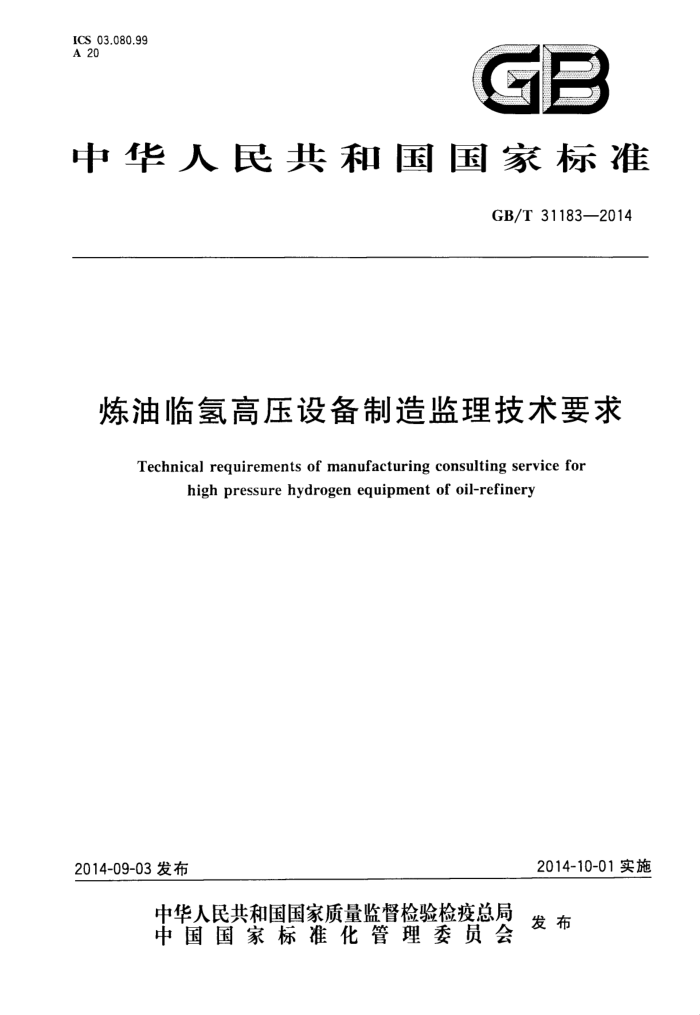
ICS 03.080.99 A 20
中华人民共和国国家标准
GB/T 31183—2014
炼油临氢高压设备制造监理技术要求
Technical requirements of manufacturing consulting service for
high pressure hydrogen equipment of oil-refinery
2014-10-01实施
2014-09-03发布
中华人民共和国国家质量监督检验检疫总局
中国国家标准化管理委员会 发布
GB/T 31183-—2014
前言
本标准按照GB/T1.1—2009给出的规则起草,本标准由全国设备监理工程咨询标准化技术委员会(SAC/TC 423)提出并归口。 本标准起草单位:上海众深石化设备科技有限公司。 本标准主要起草人:华伟、时晓峰、周逸林、刘斌、方寿奇、邵树伟
I
GB/T 31183--2014
炼油临氢高压设备制造监理技术要求
1范围
本标准规定了与炼油临氢高压设备热壁加氢反应器、加氢换热器等制造质量有关的设备监理的基本技术要求,
本标准适用于炼油临氢高压设备热壁加氢反应器、加氢换热器及化工、煤化工、化肥的临氢设备的制造监理。
2规范性引用文件
下列文件对于本文件的应用是必不可少的。凡是注日期的引用文件,仅注日期的版本适用于本文件。凡是不注日期的引用文件,其最新版本(包括所有的修改单)适用于本文件。
GB 150—2011 压力容器 GB/T8923.1一2011涂覆涂料前钢材表面处理表面清洁度的目视评定 三第1部分:未涂覆过
的钢材表面和全面清除原有涂层后的钢材表面的锈蚀等级和处理等级
GB/T26429—2010 设备工程监理规范 JB/T10175--2008热处理质量控制要求
3术语和定义
GB/T26429一2010中界定的以及下列术语和定义适用于本文件。
3.1
制造监理 manufacturing consulting service 设备监理单位接受委托人委托,按照合同约定,对设备制造过程进行专业化监督和管理的服务。
3.2
见证witness 设备监理人员对文件、记录、实体、过程等实物、活动进行观察、审查、记录、确认等的作证活动。 [GB/T 26429---2010,定义 3.13]
3.3
停止见证点 hold point H点由设备监理工程师见证并签认后才可转入下个过程、工序或节点而预先设定的监理控制点。 [GB/T 26429—2010,定义3.16]
3.4
现场见证点witness point W点由设备监理工程师对设备工程的过程、工序、节点或结果进行现场见证而预先设定的监理控制点。 [GB/T 26429--2010,定义3.15]
11
GB/T 31183--2014
3.5
文件见证点 record point R点由设备监理工程师对设备工程的有关文件、记录或报告等进行见证而预先设定的监理控制点。 [GB/T 26429-—2010,定义3.14
3.6
日常巡视检查 ordinary inspection 设备监理人员对设备工程进行的定期或不定期的现场监督活动。 [GB/T 26429-—2010,定义3.17]
3.7
临氢设备 equipment in hydrogen service 在高温高压及含氢组分工况下工作的设备。
3.8
改型钢 advanced steel 改进的 24Cr-1Mo,2/4Cr-1Mo-14V,3Cr-1 Mo-4 V 钢。
3.9
常规钢 conventional steel 标准的 24Cr-1Mo,3Cr-1Mo 钢。
3.10
回火脆性 E temper brittleness 淬火钢回火时在某温度区间内发生的脆化现象。
3.11
回火脆性敏感系数brittleness sensitive coefficient J系数、X系数预测材料或焊缝金属脆化敏感性的系数。 注:采用金属的化学成分进行预测。
3.12
脆性转变温度 brittleness transition temperature 金属材料由韧性状态转变为脆性状态的温度区域。 注:在脆性转变温度区域以上,金属材料处于韧性状态,断裂形式主要为韧性断裂;在脆性转变温度区域以下,材料
处于脆性状态,断裂形式主要为脆性断裂(如解理)。
3.13
最终焊后热处理 post weld heat treatment; PWHT 设备制造完成后投人运行前,所进行的最后一次焊后热处理。
3.14
最大焊后热处理 maximum PWHT 对试样进行的特定的热处理,用以模拟所有制造过程中的热处理包括奥氏体化和回火处理,所有高
于482℃的中间热处理,最终焊后热处理以及至少一次的业主将来可能进行的最小的附加焊后热处理。 3.15
最小焊后热处理 minimum PWHT 对试样进行的特定的热处理,用以模拟最小的热处理,包括奥氏体化和回火处理,以及高于482℃
的中间热处理和最终焊后热处理。
2
GB/T 31183—2014
3.16
步冷试验(回火脆性倾向性评定)step cooling tests 模拟和加速试件脆化的特定的热处理,用于评估高温下服役的合金钢的回火脆化敏感性。
3.17
氢剥离试验 hydrogen dissection test 在一定压力、温度和氢分压下,评价堆焊层的氢剥离的敏感性试验方法。
3.18
铁素体数ferritic number;FN 以铁素体数为单位的奥氏体不锈钢焊缝熔敷金属的铁素体含量。
3.19
超声衍射时差法 time of flight diffraction ; TOFD 采用一发一收探头对工作模式、主要利用缺陷端点的衍射波信号探测和测定缺陷尺寸的一种超声
检测方法。
4 总则
4.1应对设备制造质量监理所需过程进行识别与控制,确定监理控制点和监理方式,报请委托人确认后,在监理实施前告知被监理单位。临氢高压设备制造质量监理控制点和监理方式的确定,应符合附录 A和附录B的要求。根据临氢高压设备的特点及被监理单位的实际情况,对制造车间及工序进行日常巡视检查。临氢高压设备的主要种类参见附录C。
注:对临氢高压设备制造质量监理所需过程的识别与控制,一般包括但不限于5.1~5.7。与临氢高压设备制造质量
有关的具体监理服务内容由合同确定。
4.2应检查被监理单位的相关资质、检查质量管理体系运行状况。 4.3应作好监理记录,向委托人及时报告见证等监理工作,按约定提交监理报告。 4.4如发现不符合,应要求被监理单位及时处置并采取纠正措施,并对处置结果及纠正措施进行验证;若被监理单位拒绝整改或延误时,应及时向委托人报告。
5与制造质量有关的监理过程
5.1原材料 5.1.1应审查主要承压件的材料质量证明文件,包括化学成分、回火脆性敏感系数、常温机械性能、高温机械性能、夏比冲击试验、晶粒度及非金属夹杂物(指锻件)、金相组织、硬度、回火脆化倾向性评定、无损检验等。核查材料与设计文件的符合性及标记。
注:主要承压件钢种为耐热高强钢1XCr-Mo,24Cr-1Mo,2XCr-1Mo-XV,3Cr-1Mo 和 3Cr-1Mo-以V。 5.1.2应审查基体及焊接材料的采购和复验符合设计和业主的要求。 5.1.3采用适当的方式见证锻焊设备主要承压件的冶炼、脱气、锻制、正火十回火热处理、粗加工、 试样。 5.1.4检查主要承压件及焊缝金属的回火脆性敏感系数系数和X系数满足设计或业主的要求。J系数和X系数的计算参见附录 D。 5.1.5应审查表1中模拟热处理试件的试验报告。
3
GB/T 31183—2014
表1试件的模拟热处理表
焊缝金属和焊评的
基体金属和焊评的
基体金属、焊缝金属和焊评的
钢种常规改型
拉伸试验最小和最大 PWHT 最小和最大PWHT
冲击试验最小PWHT 最小PWHT
步冷试验
最小PWHT 最小PWHT
1i
5.1.6应审查主要承压件和焊缝熔敷金属的回火脆性倾向性评定报告符合设计或业主的要求。回火脆性倾向性评定试验过程参见附录D。 5.1.7制造过程中如改变了材料的供货热处理状态,应审查恢复材料供货状态的热处理报告和力学性能等报告。 5.2焊接 5.2.1应在产品施焊前,审查焊接工艺评定报告和产品焊接工艺规程。
注1:焊接工艺评定一般包括基体焊接工艺评定、堆焊工艺评定、异种钢焊接工艺评定、管子与管板焊接工艺评定和
返修焊补工艺评定五大类。
注2:基体焊接工艺评定,包括焊缝和热影响区的回火脆性评定试验。 5.2.2应检查焊接作业人员资格。 5.2.3抽查铬钼钢的焊接、热切割、气刨前的预热温度,检查焊后消除应力热处理。
注:对预热和焊后中间热处理的温度和及时性的检查是控制耐热高强钢在焊缝中出现冷裂纹的重要手段。 5.2.4基体材料焊后消应力如果采用消氢处理,应审查被监理单位有关控制氢的信息和措施,包括检查焊接材料的采购和储藏,消氢处理后焊缝和热影响区的氢含量以及焊接接头超声检测的灵敏度,并应征得业主的书面同意。 5.2.5应检查焊接接头及堆焊层外观、尺寸。 5.2.6应检查所有的焊接接头全焊透及接管与容器连接焊缝的圆滑过渡。 5.2.7应审查承压焊缝熔敷金属的化学成分(Cr、Ni、Mo、Mn、Cu、Si和V元素)和 X系数报告。 5.2.8见证焊缝硬度测试部位及测试点数,审核最终热处理后的承压焊缝和热影响区母材侧维氏硬度测试报告。 5.2.9按设计或业主要求审查堆焊层的氢剥离试验报告。
注:氢剥离试验的试验标准、评定方法和验收指标由被监理单位和业主商量,试验条件、试验参数(氢分压,温度和
冷却速度等)模拟实际操作工况。试验条件可参见ASTMG146相关内容。
5.2.10应审查采用化学分析方法的产品不锈钢堆焊层化学成分检验报告。 5.2.11见证产品不锈钢堆焊层取样及采用仪器测试的部位及测试点数,审核仪器测试和化学分析计算的不锈钢堆焊层的铁素体数检验报告。
注:用奥氏体不锈钢焊缝金属的化学成分计算铁素体数,参见ASMEⅡ PartC SFA-5.22图A2WRC的不锈钢焊
缝金属WRC-1992(FN)图。
5.3热处理 5.3.1按GB150一2011及JB/T10175—2008的要求,检查热处理设备及热工仪表的适用性、有效性。 5.3.2应审查热处理工艺文件,核实热处理执行与工艺文件的一致性。 5.3.3应审查以下热处理报告(包括曲线):
a)筒体热成型、封头热冲压及弯管热成形后的性能热处理(正火加回火或调质); b)中间消应力热处理; 4
GB/T 31183—2014
c)最终热处理; d)高压换热器分程箱不锈钢焊接件稳定化热处理。
5.3.4检查设备最终焊后热处理,包括检查内外壁热电偶的数量及布置。对于分段最终焊后热处理,还应检查热处理的装备和保温措施。 5.3.5抽查 U形管弯管段含 150 mm 直管段的固溶热处理。 5.3.6应查看超过下临界相变温度的铬钼钢热成型和热加工及重新正火处理的过程。不得采用热成型和热加工代替正火处理,并检查正火试件。 5.3.7应审查产品试件(焊接试件、母材热处理试件)力学性能检验报告。 5.4无损检测
5.4.1 应检查无损检测人员资格及无损检测设备的有效性 5.4.2 2审查被监理单位的无损检测报告。对射线检测,逐张对底片进行确认。重要部位的表面无损检测和超声检测,应到现场检查。 5.4.2.1审查以下材料无损检测报告:
a) 母材钢板的超声检测; b) 壳体、接管和法兰等锻件的超声检测; c) 直径大于 50mm的棒料的超声检测; d)换热管的超声或涡流检测; e) 锻件加工表面、焊接坡口的磁粉或渗透检测; f) 待堆焊表面的磁粉检测; g) 靠近管板中心的3排U形管试压后弯制部分(至少包括150 mm长直管)的渗透检测。
5.4.2.2 审查最终焊后热处理前的无损检测报告:
a) 所有承压对接焊缝及容器与裙座的连接焊缝的射线检测; b) 堆焊层的磁粉或渗透检测、超声检测; c) 所有受压焊缝包括清根的磁粉检测; d) 本体临时附件去除后的磁粉或渗透检测; e) 临氢换热器管头焊缝的渗透检测; f) 法兰密封面加工后的渗透检测; g)八角垫机加工后的渗透检测; h) 焊缝和再热裂纹的 TOFD检测。 注:采用衍射时差法超声检测(TOFD)代替射线检测根据设计文件规定。焊缝TOFD的操作、探伤方法、探伤要
求、验收级别参见NB/T47013.10—2010《承压设备无损检测第10部分:衍射时差法超声检测》。
5.4.2.3 审查最终焊后热处理后的无损检测报告:
a)J 所有承压焊缝包括接管焊缝的超声检测; b) 所有可实施的焊缝的磁粉检测;注:采用交流磁扼法防止电弧击打。在磁粉检测难以实施时,采用渗透检测代替磁粉检测。 c)所有奥氏体不锈钢堆焊层和焊接到堆焊层的焊缝的渗透检测; d) 奥氏体不锈钢堆焊层(包括支持凸台上下200mm高度内)及裙座与壳体连接焊缝的超声
检测。
5.5零部件、尺寸和预组装 5.5.1采用适当方式检查试验过程及外观质量,对主要尺寸、几何形状复测。审核以下检验试验记录:
a)筒体机加工后或校圆后的几何形状;
5
GB/T 31183—2014
b) 封头冲压及弯管成形后的几何形状; c) 承压件及不锈钢堆焊层厚度; d) 管束弯管拉伸侧壁厚及弯管段的圆度; e) 分配盘、冷氢盘的充水试验; f)U形管束弯制后的单管压力试验; g) 热电偶开口及套管致密性试验; h) 法兰和盖密封面硬度及两者硬度差; i)八角垫机加工后硬度; i)装配尺寸、总体尺寸、管口方位。
5.5.2确认与大气接触的螺栓和螺母采用了磷化处理,检查螺栓螺纹采用滚制的方法加工。
注:滚制方法可以保证金属流线的连续性。 5.5.3应检查所有内构件(如分配盘、冷氢盘、催化剂支持盘等)在模拟件内进行的预组装、组装标记及内件装配图。 5.5.4检查临氢换热器管头与管板连接形式为强度焊加贴胀,宜采用先焊后胀的顺序。检查管头伸出管板长度,见证管头第一层焊缝的气密性试验。 5.5.5分台交货的重叠式换热器,预装时应检查相连接管的对准及相配的接管法兰平行度。 5.5.6临氢设备分段交货,出厂前应检查预组对,现场合拢组焊前还应检查工件外观、施工装备、施工条件等。 5.6水压试验、气密性试验 5.6.1现场见证试验过程,审核水压试验和气密性试验报告。 5.6.2水压试验,应检查下列内容:
a)计量器具; b)容器壁温; c) 升压和降压速率; d)i 试验压力、保压时间; e) 奥氏体不锈钢材料试验用水氯离子含量; f) 按压差设计的换热器管程和壳程水压差试验方案及程序; g) 渗漏或泄漏、变形或响声。
5.6.3气密性试验,应检查以下内容:
a) 计量器具; b)i 试验介质; c) 升压和降压速率; d)i 试验压力、保压时间; e) 渗漏检查。
5.7油漆和包装 5.7.1 检查设备外表面喷砂除锈、表面处理应达到GB/T8923.1-2011中的Sa2.5级。 5.7.2设备发运前,检查设备内部清理、试验液体的排干、有无异物。 5.7.3检查油漆质量。 5.7.4检查焊接坡口的防护及密封面的保护及主螺栓螺纹防高温咬合的保护。 5.7.5检查设备充氮保护。
6