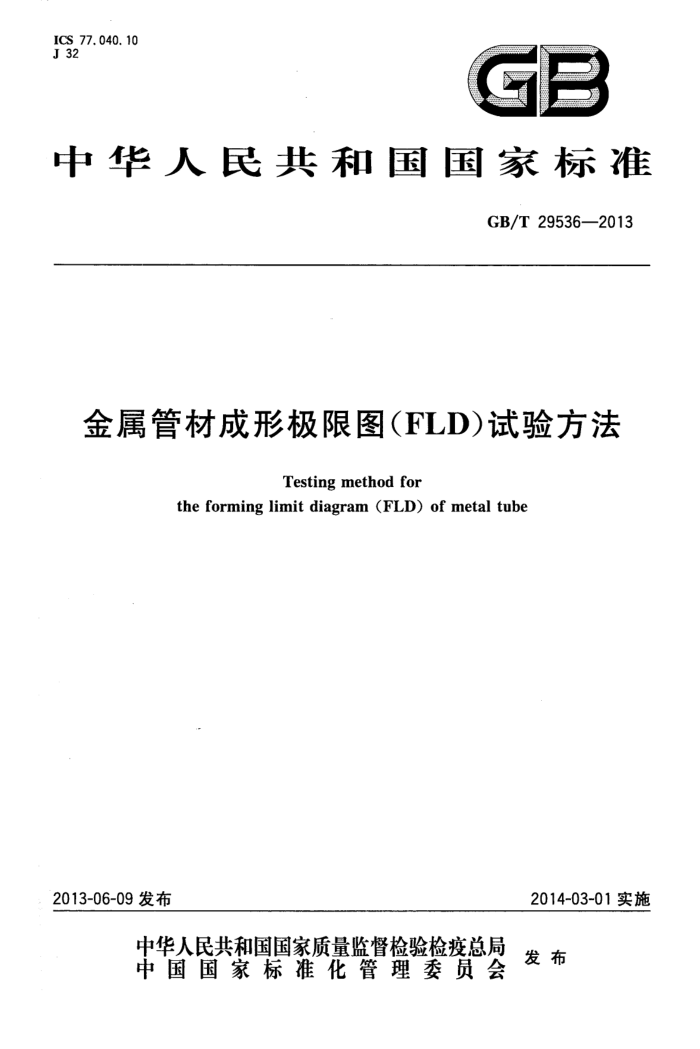
ICS 77.040.10 J32
GB
中华人民共和国国家标准
GB/T29536—2013
金属管材成形极限图(FLD)试验方法
Testing method for
the forming limit diagram (FLD) of metal tube
2014-03-01实施
2013-06-09发布
中华人民共和国国家质量监督检验检疫总局
中国国家标准化管理委员会 发布
GB/T29536—2013
前言
本标准按照GB/T1.1一2009给出的规则起草。 本标准由全国锻压标准化技术委员会(SAC/TC74)提出并归口。 本标准主要起草单位:宝山钢铁股份有限公司、上海交通大学。 本标准主要起草人:蒋浩民、陈新平、李淑慧、于忠奇。
GB/T29536—2013
金属管材成形极限图(FLD)试验方法
1范围
本标准规定了金属管材成形极限图(FormingLimitDiagram,缩写FLD)的试验方法。 本标准适用于截面壁厚0.20mm~4.00mm、外径20mm~120mm的圆形金属管材(包括无缝管
和焊管)。
2规范性引用文件
下列文件对于本文件的应用是必不可少的。凡是注日期的引用文件,仅注日期的版本适用于本文件。凡是不注日期的引用文件,其最新版本(包括所有的修改单)适用于本文件。
GB/T15825.2金属薄板成形性能与试验方法第2部分:通用试验规程 GB/T24171.2一2009金属材料薄板和薄带成形极限曲线的测定第2部分:实验室成形极
限曲线的测定
GB/T25134锻压制件及其模具三维几何量光学检测规范
3试验原理
3.1金属管材成形极限图的试验通常采用在管材内部充压的加载方式进行。 3.2将外表面印有网格的管材放置在下模内,将上模压下,完成合模;向管材内部充填低压介质(液体或气体),并采用端部冲头实现密封;向密封的管材内部充入高压的介质(液体或气体),使管材在模具型腔内产生变形;同时,通过对端部冲头位移的控制,实现不同的应变路径(见图1);当管材局部产生颈缩或破裂时,停止试验。
管材
中头
冲头
Lo 引导区
Le 引导区
Lr 变形区
图1 管材成形极限试验原理示意图
3.3测量试样表面产生变形后的网格尺寸,计算主、次应变,绘制成形极限图。
1
GB/T29536—2013
4符号、名称和单位
本标准所采用的符号、名称和单位见表1。
表1符号、名称和单位
符号 FLD FLC Do Ra pi to F F eive2 61,E2 Rm d. di d2 L: L Le
单位
名称
成形极限图成形极限曲线管材外径模具圆角半径内压力管材壁厚轴向进给力合模力表面工程主应变表面真实主应变抗拉强度网格圆初始直径变形后的网格圆长轴尺寸变形后的网格圆短轴尺寸变形区长度试样长度引导区长度
mm mm MPa mm N N %
MPa mm mm mm mm mm mm
试样准备
5
5.1 试样采用圆形管材。 5.2根据管材的壁厚和外径、试验模具的特点确定试样长度和数量。 5.2.1试样长度:由式(1)确定。
L=L+2L
(1)
式中: L.- 根据试验模具的尺寸确定。平面应变路径试验和拉-压变形路径试验时,L≥2D。;拉-拉变
形路径试验时,L:=(1~2)D。。
5.2.2试样数量:每组成形极限图试验的应变路径不少于5种,每种应变路径下的有效试验数量不少于3个。 5.3试样端部进行去毛刺处理;为了保证端部冲头的密封,端部不宜倒角。 5.4试样外表面印制网格。 5.4.1网格尺寸:根据管材的外径,可选择1mm~2.5mm尺寸的网格。
2
GB/T295362013
5.4.2网格印制方法:可采用电化学、照相、丝网印刷、网格转印、喷涂等技术印制。具体方法可参见附录A。 5.4.3网格类型:通常有方形、圆形、点阵、随机图案(散斑)等类型。网格的排列方式可参考图2的图案,也可以自行设计。随机图案(散斑)可按GB/T25134的规定。
000 000 000
+++ 田田
D
O OC
a)
c)
d)
b)
e)
C
f)
g) 图2网格的排列图案
h)
i)
5.5网格的准确度:原始网格的尺寸偏差不大于其数值的2%。
6设备和模具
6.1试验设备应具备向试样内部提供内压力的装置及控制系统。所提供的内压力力应满足式(2):
2toRm
pi>D
·(2)
6.2试验设备应能提供足够的合模力。所提供的合模力F.应满足式(3):
F.≥1.1(D。-2to)Lpi
(3)
6.3试验设备应能够提供沿试验轴线方向的进给力。所提供的轴向进给力应满足式(4):
(D。= 2t0)" pi
F≥1.5元(
(4)
2
6.4试验设备的其他要求,可按GB/T15825.2的规定。 6.5试验模具应能保证试验原理和试验条件,对于试验模具的结构、形状、尺寸不作具体规定。
7试验程序和操作方法
7.1# 按第5章的规定准备试样。 7.2 根据试样直径选择安装合适的端部密封冲头。 7.3安装相应的试验模具(如适合进行平面应变、拉-压应变、拉-拉应变等变形方式的模具),连接所需要的管路。 7.4对模具、试验装置和试验设备进行适当的清洗、检查和润滑。 7.5不 在空载条件下检查端部密封冲头与模具的对中性。 7.6 将试样放置在下模内。 7.7 合模,施加合模力。
GB/T29536—2013
7.8当采用液体作为充压介质时,需先向试样内部充填低压介质,以排空试样内部的空气,然后使端部密封冲头与试样端部接触,直至实现密封。 7.9根据试样的材质、厚度和外径,制定各种应变路径下的加载曲线(包括内压力加载曲线和端部密封冲头加载曲线)。 7. 10 # 按制定的加载曲线加载,直至试样上发生局部破裂。 7.11卸压,开模,退回端部密封冲头,取出试样。 7.12 对模具型腔内的残留介质进行吹扫。 7.13重复进行7.6~7.12。 7.144 每种应变路径下至少进行3次有效重复试验。
8试验结果的测量和处理
8.1人工测量方法 8.1.1印制以圆形为主的网格图案[图2中a)~h)的试样成形后圆形变成椭圆形,可手工测量。 8.1.2在靠近裂纹任一侧,沿着变形前呈直线的主应变方向测量3个相邻网格变形后的标距长度。重复测量直到3个测量值之间的差别小于10%。将这3个测量值的平均值记为d1。 8.1.3测量这3个相邻网格的次应变方向变形后的标距长度,将其平均值记为d2。 8.1.4如果3个测量值的差别大于10%,需要重新取样进行试验后再测量。或者通过测量垂直于裂纹的最大应变位置的椭圆确定“钟形曲线”。“钟形曲线”的测量方法可按GB/T24171.2一2009中的第 5章和附录C的规定。 8.1.5根据式(5)计算工程(或真实)主、次应变:
dl= d × 100%
er= d。
dz-do × 100% = 1(2)
e2
do
....(5)
. =1(2)
8.1.6工程上常采用附录B的方法直接测量工程主、次应变。 8.2光学测量方法 8.2.1可使用计算机控制的数字化网格应变分析扫描系统检测临界网格圆,并自动计算其应变数值,但系统设置的计算方法和判定有效试验的依据也应分别符合8.1.2、8.1.3和8.1.4的规定。 8.2.2光学测量系统可按GB/T25134的规定。 8.2.3测量方法可按GB/T24171.2—2009的规定。 8.3成形极限图和成形极限曲线 8.3.1以次应变e2为横坐标、主应变e1为纵坐标,将试验测定的应变(e1,e2)标绘在此应变坐标系中,即为试验所获得的成形极限图(FLD)(见图3)。 8.3.2根据工程主应变ei和次应变e2的分布特征,将它们连成适当的曲线,即成形极限曲线(FLC) (见图4)。 8.3.3也可使用数学回归方法建立成形极限曲线,并要求在试验报告中说明回归方程和置信度。
4
GB/T295362013
e1
e1
100
o
100上
80
60
0
401° 20
20
40 20
20
0
40 6
20
40
0
20
40
图3 成形极限图(FLD)
图4成形极限曲线(FLC)
试验报告
9
9. 1 试验报告格式可自行设计。 9.2 试验报告需包括下述主要内容:
a) 试验方法:含本标准号及名称; b) 试样标识; c) 试样管坏材料的厚度、直径、牌号和状态; d) 网格圆的初始直径; e) 试验的测量计算结果:包括d、dz,(e1e2)或(ei,Ez); f) 成形极限图(FLD)和/或拟合的成形极限曲线(FLC); g) 试验日期。
9.3 试验报告还可包括下述内容:
a) 试样的化学成分; b) 试样的材料性能; c) 试验过程描述; d) 应变网格图案(局部)及网格圆直径的统计偏差; e) 试验中的其他说明。
O
GB/T29536—2013
附录A (资料性附录)网格印制方法
A.1冲孔标记一一使用冲孔标记是最简单的方法,它在主应变方向设置两个标距,在与主应变垂直的方向设置第三个标距。为了测量应变,需要测量变形前、后两个网格的长度,然后根据标距计算出在每个方向的应变。冲孔标记很浅,它可能会造成材料早期的成形失败。因此,冲孔标记只能应用于成形性能很好的材料中。 A.2正方形网格一一在使用板料拉伸分析应变的早期,正方形网格使用较多。为了能精确获得FLC,关键区域内的网格都应测量,其测量方法类同于冲孔标记的测量方法 A.3圆形网格—在测量小应变水平时经常使用金属圆规在需要测试应变的试样表面绘制网格。一般用1.25mm的网格测量5%以下的应变。与它类似的2.5mm的网格一般用来预测FLC。 A.4感光腐蚀一一金属表面感光腐蚀的方法是以网目底板为模板,进行曝光、显影后,未感光的部分被洗掉露出钢板表面,已感光的部分附着在钢板上,在钢板表面上留下网孔,再对感光后的板材进行腐蚀处理。这种方法可以获得线宽很好的网格。但是存在个问题,就是当应变较大时,网格可能会脱落从而导致错误的结果。 A.5丝印-一通过丝印可以印制圆形、方形各种符合要求的网格。在圆形网格早期的使用中,这种印制方法经常使用。但是存在一个问题,就是当网格标距小于25mm时,测量结果不太精确。 A.6电化学腐蚀一一这是丝印的一种升级方法,用于为金属零件印制标记和信息。在被浸蚀的薄板与浸有电解液的毡垫之间有带孔眼的蜡纸,板材与毡垫之间通以低压电流并紧压在蜡纸上。电流仅在蜡纸上有孔眼的地方通过,使带着电流的电解液流至薄钢板,与蜡纸同样的印痕就浸蚀到金属板上。 A.6.1印制网格的工具:
a)早期是使用一个很宽的压盘在化学溶液中印制,现在使用较多的毡垫是滚筒和压盘。 b)不同供应商的蜡纸需要使用不同的电压和腐蚀方法。各种不同形式的蜡纸可以用在各种不同
的材料上,以满足客户的需求。对于预测FLC,要求具备好的线宽的网格。 c)2 在不同的试样表面要使用不同的腐蚀剂,对于普通钢、不锈钢、铝、铜、锌等不同的材料需要使
用不同的腐蚀剂。
A.6.2 印制网格的步骤:
a) 让蜡纸上面浸有腐蚀剂,覆盖在需要腐蚀的材料上;
用浸有同种腐蚀剂的压盘压在蜡纸上;
b)
c) 打开开关,用滚筒在带有蜡纸的压盘上慢慢滚过; d) 当把压盘和蜡纸从试样表面拿开后,相同宽度和深度的网格线就会被印制在金属表面。
A.6.3印制网格时的注意事项:
a) 如果网格太浅,则需在压盘上浸上更多的腐蚀液;如果网格太深或者太宽,则需要调整电压。 b)在压盘上应有足够的腐蚀液,但是腐蚀液也不宜太多,建议压盘厚度为3mm左右。 c) 避免压盘来回滚动,否则因蜡纸移动而产生印制的网格发生重影。 d) 滚简和材料不能接触,否则可能会对操作者产生轻微的电击。只有在腐蚀过程中才能打开电
流,同时手应握住滚筒。
A.6.4在试验前,印制的网格应烘干,否则可能会使网格变浅,以至在试验时雄以测量。并且随机抽检网格尺寸,确定网格尺寸没有受蜡纸移动的影响, A.6.5由于腐蚀剂的腐蚀性,在腐蚀完毕后,需清洗干净或者用其他腐蚀液中和金属表面的腐蚀剂,但是暴露在空气中一段时间之后就会使板料生锈。可以通过减小压盘上多余腐蚀液的方法来尽量减少这种损失。有些腐蚀液是含有防锈剂的,另外在材料表面涂润滑油也可以防止生锈。
6