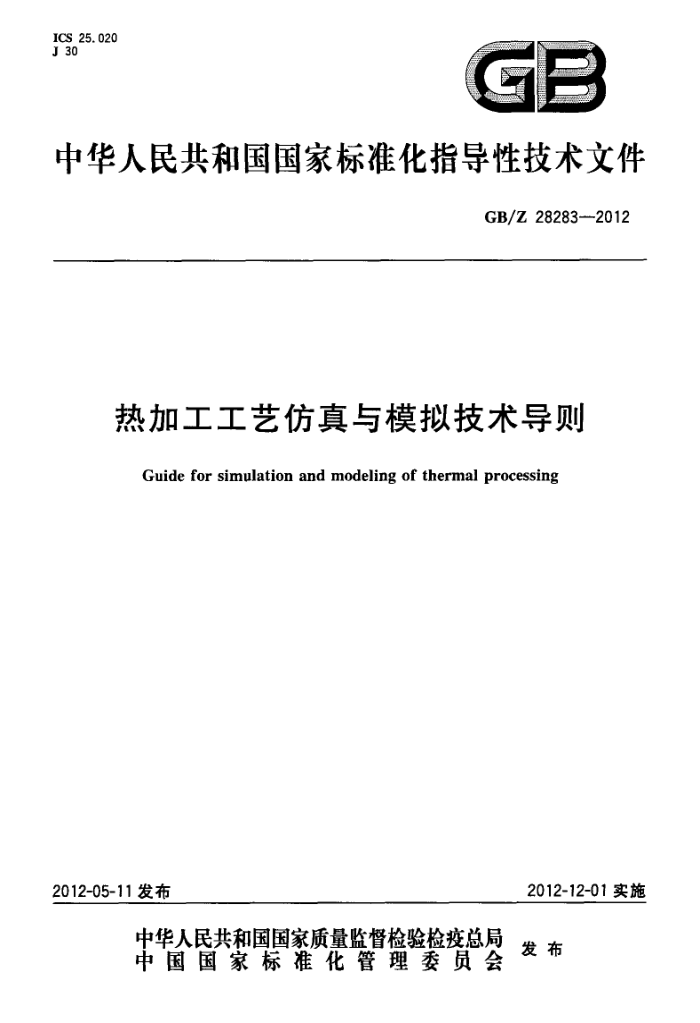
ICS 25. 020 J 30
中华人民共和国国家标准化指导性技术文件
GB/Z 28283--2012
热加工工艺仿真与模拟技术导则
Guide for simulation and modeling of thermal processing
2012-12-01实施
2012-05-11发布
中华人民共和国国家质量监督检验检疫总局中国国家标准化管理委员会
发布
中华人民共和国国家标准化指导性技术文件热加工工艺仿真与模拟技术导则
GB/Z 28283—2012
*
中国标准出版社出版发行北京市朝阳区和平里西街甲2号(100013) 北京市西城区三里河北街16号(100045)
网址 www. spc. net. cn
总编室:(010)64275323 发行中心:(010)51780235
读者服务部:(010)68523946 中国标准出版社秦皇岛印刷厂印尉
各地新华书店经销
*
并本 880×1230 1/16 印张 1 字数 25 于字 2012年8月第一版 2012 年 8 月第-次印刷
¥
书号:155066·1-45303定价 18.00元
如有印装差错 由本社发行中心调换
版权专有 有侵权必究举报电话:(010)68510107
GB/Z 28283-—2012
前言
本指导性技术文件按照GB/T1.1一2009给出的规则起草。 本指导性技术文件由中机生产力促进中心提出。 本指导性技术文件由全国技术产品文件标准化技术委员会(SAC/TC 146)归口。 本指导性技术文件的主要起草单位:中机生产力促进中心、先进成形技术与装备国家重点实验室
清华大学。
本指导性技术文件的主要起草人:丁红宇、金泉林、张艳妹、曾攀、林峰、张秀芬、刘伟。
H
GB/Z 28283—2012
热加工工艺仿真与模拟技术导则
1 范围
本指导性技术文件规定了热加工工艺仿真与模拟技术的含义、尺度划分原则、主要功能、主要内容,提出精度和速度、物理模拟及精确测试、集成方面的共性要求,并给出了铸造、锻压以及焊接工艺仿真与模拟的主要技术内容、主要步骤以及关键因素的说明。
本指导性技术文件适用于从事材料热加工工艺仿真与模拟技术的研发、应用与评估。
2热加工工艺仿其与模拟概述
热加工工艺仿真与模拟技术是指应用模拟仿真、试验测试等手段,针对金属材料铸造、锻压、焊接、 热处理及非金属材料注塑等热加工过程,在拟实的环境下模拟材料加工工艺过程,显示材料在加工过程中形状、尺寸、内部组织及缺陷的演变情况,预测其组织性能质量,达到优化工艺设计技术的总称。
它涉及的主要技术包括: a)热加工过程的数值模拟通过建立能准确描述某一热加工工艺过程的数理模型及对数理方程的简化求解,动态显示该过程
并预测其结果。
b)热加工过程的物理模拟是一种必要的验证方法。它是按照相似原理,采用相同或似的材料制成试样,在相似的条件下进
行试验,得出工艺过程的有关规律和数据、判据,并检验、校核数值模拟的结果。
c)专家系统把相关的专家知识按一定的逻辑结构表示成计算机能够利用的形式以优化工艺参数和设计。一般
包括知识库、逻辑推理判断系统及人机接口3个核心部分。由于热加工影响因素十分复杂,所以它也是数值模拟的一个有效补充。
d)热加工过程的基础理论及缺陷形成分析它是准确地建立过程数理模型,得到缺陷科学判据的技术基础。
3热加工工艺仿真与模拟的尺度划分
分为宏观(mm-m级)、微观(μm-mr级)、原子(nm-μm级)3个不同的模拟尺度:一宏观(mm-m级)一般以预测形状、尺寸等轮廓的宏观尺度为目的。
微观(μm-mm 级)一般以预测组织、结构、性能为目的。 一- 原子(nm-μm 级)一般以预测组织、结构、性能为目的。
4热加工工艺数值模拟的主要功能
4.1动态模拟工艺过程
形象地显示各种工艺的实施过程及材料形状、轮廊、尺寸、缺陷、组织的演变情况。
1
GB/Z 28283--2012
4. 2预测工件的组织性能质量
预测在不同工艺条件下材料经成形改性制成零件后的组织性能质量,特别是能找出易发缺陷的成因及削除方法。 4.3优化工艺设计
通过在虚拟条件下调整不同的工艺参数,得出最优工艺方案。可将传统工艺设计时优化工艺的途径(修改模具或修改图样)改为在计算机上修改构思的处理方法。
5热加工工艺数值模拟的主要内容
热加工工艺数值模拟主要包括前处理、模拟分析计算和后处理三部分内容。 5.1数值模拟的前处理
前处理的任务是为数值模拟准备一个初始的计算环境及对象。主要包括三维造型和网格剖分。 5. 1. 1 三维造型
将模拟对象(铸件、锻件、焊接结构件等)的几何形状及尺寸以数字化方式输人,成为模拟软件可以识别的格式。由于目前已有商品化造型软件推出,除特殊情况外,一般可采用商品化软件,如Pro-E、 UG、AutoCAD、Solid edge、Solid works 等作为模拟的软件平台,进行前处理。 5.1.2网格剖分
按模拟功能的精确度,将实体造型分成一定形状、细度的单元。单元划分越小,模拟的精确度越接近微观。 5.2模拟分析计算 5.2.1概述
模拟分析计算是数值模拟的核心。按其功能,主要包括宏观模拟仿真、微观组织及缺陷的模拟仿真、多种物理场的耦合计算。 5.2.2宏观模拟仿真 5.2.2. 1概述
宏观模拟仿真是模拟热加工过程中材料形状、轮廊、尺寸及宏观缺陷(变形、缺肉、皱折、缩孔、气孔、 夹渣等)的演化过程及最终结果。为达到上述目的,需建立并求解以下一些物理场的数理方程。 5. 2. 2.2温度场
是进行热加工过程数值模拟最重要的物理场。可以直接预测铸件的凝固前沿及缩孔缩松的位置及大小,同时它也是其他所有物理场的计算基础。 5.2.2.3应力/应变场—位移场
是建立在弹塑性力学基础上的物理场。主要用于模拟金属的塑性成形过程及充不满(缺肉)、皱折、 孔洞等缺陷的产生,同时可预测铸件、焊接件的应力分布及变形、裂纹等缺陷。一般采用有限元法求解。
2
GB/Z 28283—2012
5.2.2.4流动场一一压力场、速度场
建立在流体力学基础上的流动场(压力场、速度场),是模拟铸件充型过程的重要模型,用于预测铸件的冷隔、卷气、夹渣,冲砂等缺陷,优化注系统,
5.2.3微观组织及缺陷的模拟仿真 5. 2. 3. 1 概述
微观组织及缺陷的模拟仿真是模拟热加工过程中材料微观组织(枝晶生长、共晶生长、粒状晶等轴
晶的转变、晶粒度大小、相转变等)及微观尺度的缺陷(混晶、偏析、氢致裂段等)的演变过程及结果。描述微观组织及缺陷演变的模型主要有随即统计模型、相场方法、相变场、特有缺陷预测模型 5.2.3.2随机统计模型
有 Monte Carlo法和 Cellar Automaton法,主要用于液→固转变时晶粒组织形成及生长的模拟。 5.2.3.3相场方法
通过微分方程反映液-固转变时扩散、有序化势及热力学驱动力的综合作用,可对金属液的凝固过程及组织的形成、生长进行真实的模拟。
5.2.3.4相变场
是模拟金属热处理中组织转变的数理模型。要综合考虑相变与温度(相变潜热)、应力(应力诱发相变,相变应力及相变塑性的发生)的相互关系及影响。 5.2.3.5特有缺陷预测模型
热塑性加工过程晶粒度演变的动态再结晶模型(预测大锻件的混晶)、焊接过程局部氢浓度集聚扩散模型(预测氢致裂纹)等。 5. 2. 4多种物理场的耦合计算
对各种物理场及方法进行局部或系统耦合。首先是宏观模拟层次中各种物理场的耦合,其中温度场是建立其他各种物理场的基础,常见的耦合有:温度场→应力/应变场、温度场一→流动场。再次是把描述热加工过程宏观现象的连续方程(温度场、应力/应变场、速度场等)与描述微观组织演变的模型进行耦合,如:温度场-→相变场、应力/应变场→相变场、温度场→统计模型、温度场→相场、温度场--→应力/应变场微观缺陷预测模型等多种宏、微观模型之间耦合。 5.3数值模拟的后处理
后处理的任务是将数值模拟的结果、输出具有工程含义、用于指导工艺分析的图形图像和三维过程动画,即动态可视化。其中包含了制造中所需的工装设计基本有效模型
6热加工工艺数值模拟的精度和速度
数值模拟的精度和速度是影响数值模拟的重要因素,在选择和应用热加工工艺数值模拟时需考患精度和速度是否能够满足要求。
3
GB/Z 28283—2012
7热加工工艺物理模拟及测试
物理模拟是揭示工艺过程本质,得到临界判据,检验、校核数值模拟结果的有力手段。在进行物理模拟时,应遵循以下要求:
a)应设计、开发或选用适用的物理模拟实验方法及装置; b)应正确、合理处理数值模拟与物理模拟(含实验验证)之间的关系;
应根据模拟对象,合理确定两者的应用比例; d) 应注重基础数据的测试,包括工件及模具(或铸型、介质、填充材料等)材料的热物性参数、高温
力性参数、几何参数、本构参数、接触、摩擦、界面间隙、气体析出、结晶潜热等各种初始条件、边界条件的数据;
e)应对预知和非预知风险做出分析。
8热加工工艺仿真与模拟技术的集成
在热加工工艺仿真与模拟技术的应用中,应注重与其他系统的集成。集成一般包括以下3个方面的集成:
a)与产品、模具CAD/CAE/CAM系统集成: b)与零件加工制造系统集成; c)与零件的安全可靠性能预测集成。
4
GB/Z 28283--2012
附录A (资料性附录)
铸造工艺仿真与模拟技术总则
A.1铸造工艺仿真与模拟技术主要内容
铸造工艺仿真与模拟技术主要包括铸件凝固过程的数值模拟、铸件充型过程的数值模拟、铸件热应力的数值模拟、铸件微观组织数值模拟等。 A. 1. 1铸件凝固过程的数值模拟
铸件凝固过程的数值模拟是通过计算温度场的温度梯度、固相率凝固时间等,用一系列准则来预测铸件在凝固过程中产生缩孔缩松的部位及大小、产生的时间等。通过这种预测可对所制定的铸造工艺方案进行修改,再通过数值模拟进行验证。同时,利用凝固数值模拟的方法可确定获得键全铸件时内口与铸件的关系。 A.1.2铸件充型过程的数值模拟
铸件充型过程的数值模拟是通过计算金属液充型过程中的流体流动得出的。充型过程的数值模拟可以分析在给定工艺条件下,金属液在浇注系统中以及在型内的流动情况。包括:流量的分布、流速的分布以及由此而导致的铸件温度场。
这种模拟可以为后来的凝固分析提供正确的初始条件。 A.1.3铸件热应力的数值模拟
铸件热应力的数值模拟是通过对铸件凝固过程中热应力场的计算、冷却过程中残余热应力的计算来预测热裂纹敏感区和热裂纹的。铸件应力的形成不仅影响铸件最终的质量和使用效果(裂纹变形等),而且影响工艺设计的质量(收缩量的准确给定等)。铸件在给定工艺下的应力分布模拟有助于通过修改工艺,将铸件产生应力的可能降低到最低限度,从而保证铸件的质量。 A. 1. 4铸件微观组织数值模拟
铸件微观组织数值模拟是计算铸件凝固过程中的成核、生长等,以及凝固后铸件的微观组织和可能具备的性能。在微观组织模拟中,用宏观传热、传质与微观形核、生长相统一的数学模型,来描述微观组织形成的动态过程。包括:自发或非自发成核、晶粒长大、枝晶生长、二相质点的分布等。
A.2铸造工艺仿真与模拟技术的主要步骤
铸造工艺仿真与模拟技术应用时的主要步骤可分为以下3个阶段。 A.2.1 前直处理
根据实际物体的结构和形状建立实体模型,并自动剖分为多面体单元。一般来讲,对于形状简单的铸件,通常采用二维的方法近似地进行数值模拟就可得到较为精确的结果。而对于结构复杂的铸件,则需三维模拟计算才能满足精度的要求。
5