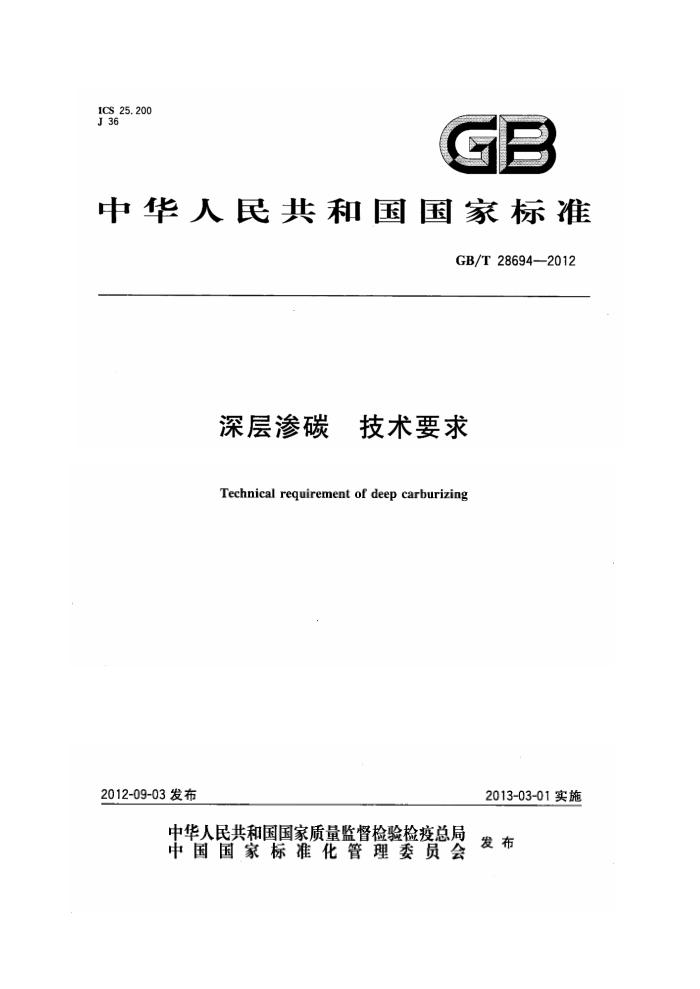
ICS 25.200 J 36
中华人民共和国国家标准
GB/T28694—2012
深层渗碳 技术要求
Technical requirement of deep carburizing
2012-09-03发布
2013-03-01实施
中华人民共和国国家质量监督检验检疫总局
中国国家标准化管理委员会 发布
GB/T 28694—2012
前 言
本标准按GB/T1.1—2009给出的规则起草。 本标准由全国热处理标准化委员会(SAC/TC75)提出并归口。 本标准负责起草单位:江苏丰东热技术股份有限公司、北京机电研究所、西安福莱特热处理有限
公司。
本标准参加起草单位:广东世创金属科技有限公司、上海市机械制造工艺研究所有限公司、南京高精齿轮集团有限公司热处理分厂、天龙科技炉业(无锡)有限公司、大连华锐股份有限公司重型热处理厂、南京高速齿轮箱制造有限公司、天津创真金属科技有限公司、爱协林热处理系统(北京)有限公司。
本标准主要起草人:向建华、邵周俊、杨鸿飞、张志鹏、张志冲、施剑峰、刘军。 本标准参加起草人:董小虹、任颂赞、蔡红、朱百智、湛宪宪、樊永君、汪正兵、刘臻、姜敬东、殷汉奇。
I
GB/T28694—2012
深层渗碳 技术要求
1范围
本标准规定了深层渗碳材料、深层渗碳设备要求、深层渗碳工艺、质量检验、安全卫生和节能要求。 本标准适用于工件的深层渗碳。
2规范性引用文件
下列文件对于本文件的应用是必不可少的。凡是注日期的引用文件,仅注日期的版本适用于本文件。凡是不注日期的引用文件,其最新版本(包括所有的修改单)适用于本文件。
GB/T224 钢的脱碳层深度测定方法 GB/T 230.1 金属材料洛氏硬度试验 第1部分:试验方法(A、B、C、D、E、FG、H、K、N、T标尺) GB/T683 化学试剂甲醇 GB/T 3864 工业氮 GB/T4340.1金属材料维氏硬度试验第1部分:试验方法 GB/T4341金属肖氏硬度试验方法 GB5959.1 电热装置的安全第1部分:通用要求 GB 5959.4 电热装置的安全第4部分:对电阻加热装置的特殊要求 GB6819 溶解乙炔 GB/T 7232 金属热处理工艺术语 GB/T 9450 钢件渗碳淬火硬化层深度的测定和校核 GB/T 9452 热处理炉有效加热区测定方法 GB/T10067.4电热装置基本技术条件第4部分:间接电阻炉 GB 15735 5金属热处理生产过程安全卫生要求 GB/T16923 钢件的正火与退火 GB/T16924 钢件的淬火与回火 GB/Z18718 热处理节能技术导则 GB/T25744—2010锅件渗碳淬火回火金相检验
3术语和定义
GB/T7232中所界定的以及下列术语和定义适用于本文件。
3. 1
心部组织corestructure 距表面3倍于渗碳淬火有效硬化层深度区域的组织。
3. 2
碳势均匀度carbonpotentialuniformity 在试验温度下热稳定状态时的碳势均匀程度。碳势均勾度表示为:在规定的各个测量点上所测的
最高和最低碳势的差。
1
GB/T28694—2012
4深层渗碳材料
4.1钢种的选择
钢种应采用本质细晶粒钢。深层渗碳钢种按零件的性能要求选择,特殊要求的零件按需要选用特殊钢种。 4.2材料检验及确认 4.2.1在深层渗碳处理前,应对钢种进行确认,并提出材料成分分析报告。 4.2.2必要时对低高倍组织、非金属夹杂物、金属平均晶粒度、内部缺陷以及材料率透性和力学性能进行检测。
5深层渗碳设备要求
5.1般要求 5.1.1深层渗碳设备的设计、制造和安全性应符合GB5959.1、GB5959.4和GB/T10067.4中的有关规定。 5.1.2深层渗碳设备应为单台渗碳炉或渗碳热处理生产线(由渗碳炉、冷却装置、回火设备、清洗机、装卸料机构、备料台、气氛系统和控制系统等组成)。渗碳炉有井式炉、密封箱式炉、底装料立式炉和真空渗碳炉等。 5.1.3深层渗碳设备应具有良好的可靠性,以适应长时间连续生产的特点。采用计算机控制及管理系统的渗碳设备一般应具有设备故障报警和自诊断功能。 5.2渗碳炉 5.2.1温度控制 5.2.1.1渗碳炉的加热方式一般为电加热或燃料加热,最高使用温度一般为1050℃。 5.2.1.2 加热设备应满足有效加热区炉温均匀性和控温仪表精度等级的要求(见表1),有效加热区的炉温均匀性应按GB/T9452规定。
表1深层渗碳炉温均匀性和控温仪表精度等级要求(不大于)
工件级别重要件一般件
炉温均匀性 ±5℃ ±8℃
控温仪表精度等级
0.2级 0.5级
5.2.1.3 深层渗碳炉一般采用多区加热、设置循环风扇和导风装置,以保证炉温均匀性和气氛均匀性。 5.2.1.4 应按GB/T9452的规定对控温系统进行校准,以保证控温精度。 5.2.1.5深层渗碳炉应配有温度记录装置。 5.2.2气氛控制 5.2.2.1 渗碳气氛应是可控气氛,炉内碳势均匀度≤士0.05%。 5.2.2.2 渗碳气氛的主要化工原料应满足表2的要求。 2
GB/T28694—2012
表2化工原料技术要求
名称丙烷异丙醇溶解乙炔甲醇工业氮
标准
主要成分(体积分数)
纯度≥90%,总硫含量≤15mg/m 纯度>98.5%,水含量<0.3%
GB 6819 GB/T 683 GB/T 3864
纯度>98.0%
纯度≥99.5%,水含量<0.3% 纯度≥99.5%,氧含量≤0.5%
5.2.2.3深层渗碳炉应配有碳势控制系统,并配有定碳孔、试样孔和取气口,必要时可设置双路碳势检测系统,一路用于控制,另一路用于监控,必要时可切换控制。 5.2.2.4渗碳气氛控制可采用程序控制或专家系统在线控制的方式。 5.2.2.5渗碳炉应有良好的密封性,炉内气氛不得有泄漏现象,炉膛内压力应保持稳定正压。 5.3球化退火及火加热设备 5.3.1有效加热区内温度均匀性在设定温度处应不大于土10℃。 5.3.2率火加热炉应配备气氛供给和控制系统。 5.4冷却设备 5.4.1淬火冷却设备一般应配备淬火介质的加热和冷却装置,并具有导向搅拌系统和温度调节系统。 5.4.2淬火介质的使用温度范围应符合GB/T16924的规定。 5.4.3率火介质质量应符合相关标准的规定。 5.4.4深层渗碳缓冷坑或冷却设备应能通保护气氮或滴注有机液体。特殊要求的可以配备温度控制装置。 5.5回火设备
有效加热区内温度均匀性在设定温度处不大于士10℃, 5.6设备的维修、保养和检定
应制定定期维修、保养和检定制度,并严格执行,存有详细记录。
6深层渗碳工艺 6.1深层渗碳工艺方法 6.1.1工艺方法1:渗碳→缓冷-→球化退火→加热淬火→清洗→回火。 6.1.2工艺方法2:渗碳→淬火→清洗→球化退火→加热淬火-→清洗→+回火。 6.1.3工艺方法3:渗碳→淬火→+清洗→回火。 6.2处理前的准备工作 6.2.1按工件的质量要求,确定防渗部位的防渗措施,了解钢材的牌号(或化学成分)和预先热处理是否符合要求。 6.2.2应去除氧化皮及锈斑,并清洗、干燥;检查工件或试样是否有裂纹,必要时进行无损检测。
GB/T28694—2012
6.2.3结构设计和制造应不影响深层渗碳的质量。 6.2.4检查深层渗碳设备及测量控制设备是否正常。 6.2.5检查形成气的原料及形成气氛的装置是否正常。 6.2.6随炉试样,过程试样可参照GB/T25744一2010中第4章的要求执行。 6.3深层渗碳处理 6.3.1装炉
工件应装在有效加热区内,并装入随炉试样和过程试样。 注:随炉试样是作为检查深层渗碳淬火回火后质量的标准试样;过程试样是作为检查深层渗碳过程中不同时间渗
碳情况的标准试样。
6.3.2升温
控制升温速度,使零件各部分之间不产生明显的温差,必要时应分段升温。
6.3.3排气
工件从进炉后,应通氮气进行排气处理,通气量按炉子容积而定。当温度升到750℃时,通人载气,直到升至深层渗碳温度。 6.3.4渗碳
通富化气,调整气氛碳势到设定值,按工件技术要求确定深层渗碳保温时间。 6.3.5碳势测量及校准
碳势检测可按现场条件使用氧探头碳势测定仪、红外仪或热丝仪等,定期对碳势控制系统实施
校准。 6.3.6 5过程试样的检验并记录
定时取出过程试样,检验深层渗碳情况,并作记录。 6.3.7冷却
对要求降温直接淬火的工件,率火前应注意均温。非直接淬火的工件缓冷时应采取防止或减少氧化脱碳的措施。必要时用保护气氛或滴注有机液体方法进行保护。缓冷时应采取措施,以减少畸变和防止开裂。 6.4渗碳后火与回火 6.4.1淬火加热、冷却及回火设备应符合5.3、5.4、5.5的规定。 6.4.2必要时可在淬火前进行球化退火,球化退火应符合GB/T16923的规定。 6.4.3淬火回火加热温度和保温时间参照GB/T16924规定,并应符合工件材料的要求。 6.4.4淬火加热时应采取防止氧化脱碳措施,工件淬火后应及时回火。 6.4.5 大件深层渗碳时应保证工件各部位的温度均匀性、对工件采取合理的加热和冷却方法。 6.4.6淬火介质应满足5.4.2、5.4.3的规定。 6.4.7 淬火加热及冷却时,应采取措施减少工件畸变、防止工件开裂。
4
GB/T28694—2012
6.5后续工序 6.5.1清除工件上残留的淬火介质和其他残留物。 6.5.2测量工件畸变情况并作记录,必要时进行校直。 6.5.3.分析随炉试样深层渗碳淬火回火质量,并作记录。 6.5.4对工件进行防锈处理。 6.5.5整理处理过程中所有记录(温度、碳势、过程检查和最终检查情况及其他必要的事项)。 7质量检验 7.1硬度 7.1.1表面硬度
表面硬度应在最终处理后的工件上测量,测量部位按工件技术要求确定,若有特别协议可在随炉试样表面测量。测量应符合GB/T230.1、GB/T4340.1和GB/T4341的规定。深层渗碳表面硬度不均匀度允许偏差应符合表3的规定。
表3表面硬度不均匀度允许偏差
工件类型重要件一般件
硬度不均匀度允许偏差”
HV1 ≤75 ≤102
HRC <3 ≤4
HS 5 6
局部深层渗碳硬度测量位置不应在渗碳与未碳交界处。 口重要件是指对质量有特殊要求的零件。
7.1.2心部硬度
深层渗碳心部硬度一般在随炉试样上测量,若有特殊要求,则可解剖工件进行测量。心部硬度应符合相关标准或技术协议要求。 7.2有效硬化层深度 7.2.1般应在最终热处理后随炉试样的横截面上进行测量,若有特别协议时,可在工件横截面上进行测量。 7.2.2硬化层深度测量方法应符合GB/T9450的规定。硬化层不均匀度允许偏差小于10%。 7.3表面碳浓度
表面碳浓度可按剥层法或光谱法检测,一般为0.75%wt~1.1%wt。当要求韧度较好时,取下限;当要求耐磨性较好时,取上限。 7.4金相组织 7.4.1金相组织可按GB/T25744中有关的规定进行检验并评级。 7.4.2渗碳件经过淬火、回火后,金相组织应符合表4的要求。
5
GB/T 28694—2012
表4深层渗碳淬火回火后金相组织的要求
晶界内氧化 非马氏体组
金相组织级别级
工件类型重要件一般件
织层深要求
层深要求
马氏体 残留奥氏体 碳化物 《3级
心部组织 3级 A4级
μm ≤30 N60
μn 《30 <60
≤2级 3级
≤4级 ≤4级
≤4级
7.5心部力学性能
一般工件可不作心部力学性能检查,有特殊要求时,可用同一材料制成直径与被测部位相同长 200mm的试样,做防渗处理后,与工件进行同样热处理,制成标准力学性能试样,按常规测定试样抗拉强度、屈服强度、伸长率、断面收缩率和冲击韧度。 7.6深层渗碳缺陷检查 7.6.1畸变
深层渗碳、球化处理、淬火回火后可用特定量具测量工件畸变情况,测量内容可根据工件技术要求确定。畸变量(可为校直后畸变量)应在技术要求范围内。 7.6.2裂纹
7.6.3表面脱碳
按GB/T224的规定的方法测定表面脱碳。
8安全卫生和节能要求
安全卫生要求应符合GB/T15735的规定,节能要求应符合GB/Z18718的规定。
ICS 25.200 J 36
中华人民共和国国家标准
GB/T28694—2012
深层渗碳 技术要求
Technical requirement of deep carburizing
2012-09-03发布
2013-03-01实施
中华人民共和国国家质量监督检验检疫总局
中国国家标准化管理委员会 发布
GB/T 28694—2012
前 言
本标准按GB/T1.1—2009给出的规则起草。 本标准由全国热处理标准化委员会(SAC/TC75)提出并归口。 本标准负责起草单位:江苏丰东热技术股份有限公司、北京机电研究所、西安福莱特热处理有限
公司。
本标准参加起草单位:广东世创金属科技有限公司、上海市机械制造工艺研究所有限公司、南京高精齿轮集团有限公司热处理分厂、天龙科技炉业(无锡)有限公司、大连华锐股份有限公司重型热处理厂、南京高速齿轮箱制造有限公司、天津创真金属科技有限公司、爱协林热处理系统(北京)有限公司。
本标准主要起草人:向建华、邵周俊、杨鸿飞、张志鹏、张志冲、施剑峰、刘军。 本标准参加起草人:董小虹、任颂赞、蔡红、朱百智、湛宪宪、樊永君、汪正兵、刘臻、姜敬东、殷汉奇。
I
GB/T28694—2012
深层渗碳 技术要求
1范围
本标准规定了深层渗碳材料、深层渗碳设备要求、深层渗碳工艺、质量检验、安全卫生和节能要求。 本标准适用于工件的深层渗碳。
2规范性引用文件
下列文件对于本文件的应用是必不可少的。凡是注日期的引用文件,仅注日期的版本适用于本文件。凡是不注日期的引用文件,其最新版本(包括所有的修改单)适用于本文件。
GB/T224 钢的脱碳层深度测定方法 GB/T 230.1 金属材料洛氏硬度试验 第1部分:试验方法(A、B、C、D、E、FG、H、K、N、T标尺) GB/T683 化学试剂甲醇 GB/T 3864 工业氮 GB/T4340.1金属材料维氏硬度试验第1部分:试验方法 GB/T4341金属肖氏硬度试验方法 GB5959.1 电热装置的安全第1部分:通用要求 GB 5959.4 电热装置的安全第4部分:对电阻加热装置的特殊要求 GB6819 溶解乙炔 GB/T 7232 金属热处理工艺术语 GB/T 9450 钢件渗碳淬火硬化层深度的测定和校核 GB/T 9452 热处理炉有效加热区测定方法 GB/T10067.4电热装置基本技术条件第4部分:间接电阻炉 GB 15735 5金属热处理生产过程安全卫生要求 GB/T16923 钢件的正火与退火 GB/T16924 钢件的淬火与回火 GB/Z18718 热处理节能技术导则 GB/T25744—2010锅件渗碳淬火回火金相检验
3术语和定义
GB/T7232中所界定的以及下列术语和定义适用于本文件。
3. 1
心部组织corestructure 距表面3倍于渗碳淬火有效硬化层深度区域的组织。
3. 2
碳势均匀度carbonpotentialuniformity 在试验温度下热稳定状态时的碳势均匀程度。碳势均勾度表示为:在规定的各个测量点上所测的
最高和最低碳势的差。
1
GB/T28694—2012
4深层渗碳材料
4.1钢种的选择
钢种应采用本质细晶粒钢。深层渗碳钢种按零件的性能要求选择,特殊要求的零件按需要选用特殊钢种。 4.2材料检验及确认 4.2.1在深层渗碳处理前,应对钢种进行确认,并提出材料成分分析报告。 4.2.2必要时对低高倍组织、非金属夹杂物、金属平均晶粒度、内部缺陷以及材料率透性和力学性能进行检测。
5深层渗碳设备要求
5.1般要求 5.1.1深层渗碳设备的设计、制造和安全性应符合GB5959.1、GB5959.4和GB/T10067.4中的有关规定。 5.1.2深层渗碳设备应为单台渗碳炉或渗碳热处理生产线(由渗碳炉、冷却装置、回火设备、清洗机、装卸料机构、备料台、气氛系统和控制系统等组成)。渗碳炉有井式炉、密封箱式炉、底装料立式炉和真空渗碳炉等。 5.1.3深层渗碳设备应具有良好的可靠性,以适应长时间连续生产的特点。采用计算机控制及管理系统的渗碳设备一般应具有设备故障报警和自诊断功能。 5.2渗碳炉 5.2.1温度控制 5.2.1.1渗碳炉的加热方式一般为电加热或燃料加热,最高使用温度一般为1050℃。 5.2.1.2 加热设备应满足有效加热区炉温均匀性和控温仪表精度等级的要求(见表1),有效加热区的炉温均匀性应按GB/T9452规定。
表1深层渗碳炉温均匀性和控温仪表精度等级要求(不大于)
工件级别重要件一般件
炉温均匀性 ±5℃ ±8℃
控温仪表精度等级
0.2级 0.5级
5.2.1.3 深层渗碳炉一般采用多区加热、设置循环风扇和导风装置,以保证炉温均匀性和气氛均匀性。 5.2.1.4 应按GB/T9452的规定对控温系统进行校准,以保证控温精度。 5.2.1.5深层渗碳炉应配有温度记录装置。 5.2.2气氛控制 5.2.2.1 渗碳气氛应是可控气氛,炉内碳势均匀度≤士0.05%。 5.2.2.2 渗碳气氛的主要化工原料应满足表2的要求。 2
GB/T28694—2012
表2化工原料技术要求
名称丙烷异丙醇溶解乙炔甲醇工业氮
标准
主要成分(体积分数)
纯度≥90%,总硫含量≤15mg/m 纯度>98.5%,水含量<0.3%
GB 6819 GB/T 683 GB/T 3864
纯度>98.0%
纯度≥99.5%,水含量<0.3% 纯度≥99.5%,氧含量≤0.5%
5.2.2.3深层渗碳炉应配有碳势控制系统,并配有定碳孔、试样孔和取气口,必要时可设置双路碳势检测系统,一路用于控制,另一路用于监控,必要时可切换控制。 5.2.2.4渗碳气氛控制可采用程序控制或专家系统在线控制的方式。 5.2.2.5渗碳炉应有良好的密封性,炉内气氛不得有泄漏现象,炉膛内压力应保持稳定正压。 5.3球化退火及火加热设备 5.3.1有效加热区内温度均匀性在设定温度处应不大于土10℃。 5.3.2率火加热炉应配备气氛供给和控制系统。 5.4冷却设备 5.4.1淬火冷却设备一般应配备淬火介质的加热和冷却装置,并具有导向搅拌系统和温度调节系统。 5.4.2淬火介质的使用温度范围应符合GB/T16924的规定。 5.4.3率火介质质量应符合相关标准的规定。 5.4.4深层渗碳缓冷坑或冷却设备应能通保护气氮或滴注有机液体。特殊要求的可以配备温度控制装置。 5.5回火设备
有效加热区内温度均匀性在设定温度处不大于士10℃, 5.6设备的维修、保养和检定
应制定定期维修、保养和检定制度,并严格执行,存有详细记录。
6深层渗碳工艺 6.1深层渗碳工艺方法 6.1.1工艺方法1:渗碳→缓冷-→球化退火→加热淬火→清洗→回火。 6.1.2工艺方法2:渗碳→淬火→清洗→球化退火→加热淬火-→清洗→+回火。 6.1.3工艺方法3:渗碳→淬火→+清洗→回火。 6.2处理前的准备工作 6.2.1按工件的质量要求,确定防渗部位的防渗措施,了解钢材的牌号(或化学成分)和预先热处理是否符合要求。 6.2.2应去除氧化皮及锈斑,并清洗、干燥;检查工件或试样是否有裂纹,必要时进行无损检测。
GB/T28694—2012
6.2.3结构设计和制造应不影响深层渗碳的质量。 6.2.4检查深层渗碳设备及测量控制设备是否正常。 6.2.5检查形成气的原料及形成气氛的装置是否正常。 6.2.6随炉试样,过程试样可参照GB/T25744一2010中第4章的要求执行。 6.3深层渗碳处理 6.3.1装炉
工件应装在有效加热区内,并装入随炉试样和过程试样。 注:随炉试样是作为检查深层渗碳淬火回火后质量的标准试样;过程试样是作为检查深层渗碳过程中不同时间渗
碳情况的标准试样。
6.3.2升温
控制升温速度,使零件各部分之间不产生明显的温差,必要时应分段升温。
6.3.3排气
工件从进炉后,应通氮气进行排气处理,通气量按炉子容积而定。当温度升到750℃时,通人载气,直到升至深层渗碳温度。 6.3.4渗碳
通富化气,调整气氛碳势到设定值,按工件技术要求确定深层渗碳保温时间。 6.3.5碳势测量及校准
碳势检测可按现场条件使用氧探头碳势测定仪、红外仪或热丝仪等,定期对碳势控制系统实施
校准。 6.3.6 5过程试样的检验并记录
定时取出过程试样,检验深层渗碳情况,并作记录。 6.3.7冷却
对要求降温直接淬火的工件,率火前应注意均温。非直接淬火的工件缓冷时应采取防止或减少氧化脱碳的措施。必要时用保护气氛或滴注有机液体方法进行保护。缓冷时应采取措施,以减少畸变和防止开裂。 6.4渗碳后火与回火 6.4.1淬火加热、冷却及回火设备应符合5.3、5.4、5.5的规定。 6.4.2必要时可在淬火前进行球化退火,球化退火应符合GB/T16923的规定。 6.4.3淬火回火加热温度和保温时间参照GB/T16924规定,并应符合工件材料的要求。 6.4.4淬火加热时应采取防止氧化脱碳措施,工件淬火后应及时回火。 6.4.5 大件深层渗碳时应保证工件各部位的温度均匀性、对工件采取合理的加热和冷却方法。 6.4.6淬火介质应满足5.4.2、5.4.3的规定。 6.4.7 淬火加热及冷却时,应采取措施减少工件畸变、防止工件开裂。
4
GB/T28694—2012
6.5后续工序 6.5.1清除工件上残留的淬火介质和其他残留物。 6.5.2测量工件畸变情况并作记录,必要时进行校直。 6.5.3.分析随炉试样深层渗碳淬火回火质量,并作记录。 6.5.4对工件进行防锈处理。 6.5.5整理处理过程中所有记录(温度、碳势、过程检查和最终检查情况及其他必要的事项)。 7质量检验 7.1硬度 7.1.1表面硬度
表面硬度应在最终处理后的工件上测量,测量部位按工件技术要求确定,若有特别协议可在随炉试样表面测量。测量应符合GB/T230.1、GB/T4340.1和GB/T4341的规定。深层渗碳表面硬度不均匀度允许偏差应符合表3的规定。
表3表面硬度不均匀度允许偏差
工件类型重要件一般件
硬度不均匀度允许偏差”
HV1 ≤75 ≤102
HRC <3 ≤4
HS 5 6
局部深层渗碳硬度测量位置不应在渗碳与未碳交界处。 口重要件是指对质量有特殊要求的零件。
7.1.2心部硬度
深层渗碳心部硬度一般在随炉试样上测量,若有特殊要求,则可解剖工件进行测量。心部硬度应符合相关标准或技术协议要求。 7.2有效硬化层深度 7.2.1般应在最终热处理后随炉试样的横截面上进行测量,若有特别协议时,可在工件横截面上进行测量。 7.2.2硬化层深度测量方法应符合GB/T9450的规定。硬化层不均匀度允许偏差小于10%。 7.3表面碳浓度
表面碳浓度可按剥层法或光谱法检测,一般为0.75%wt~1.1%wt。当要求韧度较好时,取下限;当要求耐磨性较好时,取上限。 7.4金相组织 7.4.1金相组织可按GB/T25744中有关的规定进行检验并评级。 7.4.2渗碳件经过淬火、回火后,金相组织应符合表4的要求。
5
GB/T 28694—2012
表4深层渗碳淬火回火后金相组织的要求
晶界内氧化 非马氏体组
金相组织级别级
工件类型重要件一般件
织层深要求
层深要求
马氏体 残留奥氏体 碳化物 《3级
心部组织 3级 A4级
μm ≤30 N60
μn 《30 <60
≤2级 3级
≤4级 ≤4级
≤4级
7.5心部力学性能
一般工件可不作心部力学性能检查,有特殊要求时,可用同一材料制成直径与被测部位相同长 200mm的试样,做防渗处理后,与工件进行同样热处理,制成标准力学性能试样,按常规测定试样抗拉强度、屈服强度、伸长率、断面收缩率和冲击韧度。 7.6深层渗碳缺陷检查 7.6.1畸变
深层渗碳、球化处理、淬火回火后可用特定量具测量工件畸变情况,测量内容可根据工件技术要求确定。畸变量(可为校直后畸变量)应在技术要求范围内。 7.6.2裂纹
7.6.3表面脱碳
按GB/T224的规定的方法测定表面脱碳。
8安全卫生和节能要求
安全卫生要求应符合GB/T15735的规定,节能要求应符合GB/Z18718的规定。