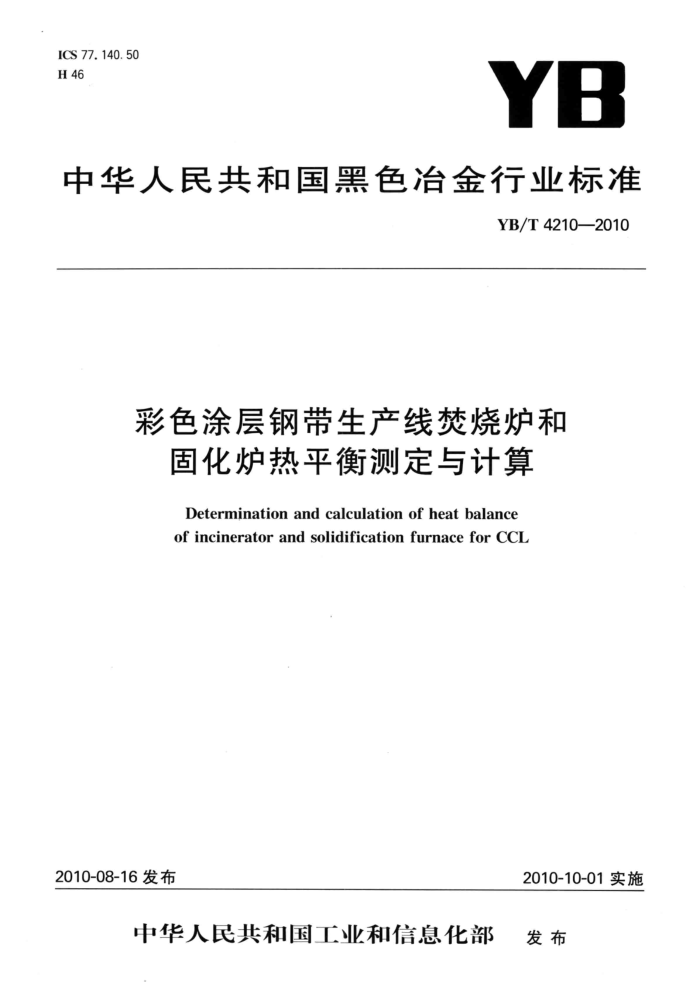
ICS 77.140. 50 H 46
YB
中华人民共和国黑色冶金行业标准
YB/T4210—2010
彩色涂层钢带生产线楚烧炉和
固化炉热平衡测定与计算 Determination and calculation of heat balance of incinerator and solidificationfurnace for CCl
2010-08-16发布
2010-10-01实施
中华人民共和国工业和信息化部 发布
YB/T4210—2010
前 言
本标准的附录A、附录B是资料性附录。 本标准由中国钢铁工业协会提出。 本标准由全国钢标准化技术委员会归口。 本标准起草单位:浙江华东钢业集团有限公司、冶金工业信息标准研究院、北京星和众工设备技术股
份有限公司、苏州博恒浩科技有限公司。
本标准主要起草人:何长化、仇金辉、汪为健、许秀飞、沈伟根、戴强、赵宝玉、史宝和、温婧。
44
YB/T4210—2010
彩色涂层钢带生产线焚烧炉和固化炉热平衡测定与计算
1范围
本标准规定了彩色涂层钢带生产线焚烧炉和固化炉热平衡测定与计算基准、测定条件、测定项目及
测定计算方法。
本标准适用于彩色涂层钢带生产中以气体燃料和电力等为供给能的焚烧炉和固化炉的热平衡测定与计算。 2规范性引用文件
下列文件中的条款通过本标准的引用而成为本标准的条款。凡是注日期的引用文件,其随后所有的修改单(不包括勘误的内容)或修订版均不适用于本标准,然而,鼓励根据本标准达成协议的各方研究是否可使用这些文件的最新版本。凡是不注日期的引用文件,其最新版本适用于本标准。
GB/T2588设备热效率计算通则 3热平衡测定与计算基准 3.1基准温度采用标准环境温度。 3.2基准压力采用标准大气压。 3.3燃料的发热量按应用低位发热量计算。 3.4焚烧炉热平衡测定与计算体系取整个焚烧炉、废气热交换器、热空气热交换器以及管道等附属设施为体系。 3.5固化炉热平衡测定与计算体系取整个固化炉以及炉气循环系统、二次供热系统等附属设施为体系,以热空气进口、燃料管道进口、废气出口为分界线。 4设备状况 4.1写明设备的新旧程度、特点及存在的问题,建成投产或上次大修后投产的日期。 4.2设备及生产概况记录表见附录A。 5热平衡测定条件 5.1被测设备和工艺
楚烧炉和固化炉热平衡测定,应在设备稳定运行期内进行,测定时期生产工艺应稳定正常,产品的规格以保证生产线达到额定生产能力确定,涂层为聚酯或固化温度相似的其他种类,固化温度为225℃~ 235℃,膜厚为20μm士1μm。 5.2频次
各项数据的测定应至少测定2次,每次间隔不少于1h。 5.3测定用仪器仪表计量器具
测定用仪器仪表计量器具要求应在检定周期之内。 6测定项目和方法
楚烧炉和固化炉测定项目和方法见表1。
45
YB/T4210—2010
表1 焚烧炉和固化炉测定项目和方法
符号 单位 测定位置 测定仪表
区分
项目
取值原则
测定频率
与方法流量计按燃料成分进行计算温度计干湿球温度计
1小时1次 算术平均值
燃料量
m/h 燃料管道上
B
燃料 燃料发热值 Qiw kJ/m
1小时1次 算术平均值
燃料温度烟气含湿量
℃ 燃料管道上 %
tr gy V, m°/h 排烟管道上 流量计 1小时1次 算术平均值 W
烟气 烟气流量
焚烧炉
数字式温度计
烟气温度助燃空气流量 Vk m/h
℃
流量计
空气 助燃空气温度 tk
℃ 空气管道上 数字式温度计 1小时1次 算术平均值
干湿球温度计红外测温仪对应区域
助燃空气湿度 gk %
炉体 表面温度
℃ m?
tb A B m°/h 燃料管道上
炉体表面
1小时1次 算术平均值 1小时1次 算术平均值
表面面积燃料量
流量计按燃料成分进行计算
燃料 燃料发热值 Qiw kJ/m3
燃料温度进入固化炉温度 tw 离开固化炉温度 t 涂料废气含湿量 gfn % 涂料废气流量 Vta m/h 涂料废气温度 tfq ℃
燃料管道上 数字式温度计 1小时1次 算术平均值
℃ ℃ ℃ 炉出口内部 红外测温仪
tr
炉外
红外测温仪
1小时1次 算术平均值
钢带
固化炉
干湿球温度计流量计 1小时1次 算术平均值数字式温度计红外测温仪
涂料废气管道人口
涂料废气
表面温度表面面积
℃ m? c %
tb A th gh
炉体
算术平均值
炉体表面
对应区域
温度相对湿度
系统环境 数字式温度计 1小时1次 算术平均值位置 干混球温度计 1小时1次 算术平均值
环境
7 热平衡计算 7.1 热量的总体收入项目
(a) 燃气燃烧的化学热(Q"); (b) 燃气带入的物理热(Q); (c) 助燃干空气带入的物理热(Q); (d) 助燃空气中水分带人的物理热(Q); (e) 钢带带人的物理热(Qw); (f) 电气发热元件发出的热量(Qa); (g) 涂料废气燃烧的化学热(Qn)。
46
YB/T4210—2010
Q=0.000124gkVk(cgtk—Cgoto)
(6)
式中: Q 助燃空气中水分带入的物理热,kJ/h(t);
0℃至入炉温度间水蒸气的平均比热容,kJ/(m3:℃); 0℃至基准温度间水蒸气的平均比热容,kJ/(m3,℃)。
Cg Cgo
7.3.5 钢带带入的物理热(Qw)计算按下式:
Qw=mw(cwtw-Cwoto)
(7)
式中: Qw 钢带带人的物理热,kJ/h(t); mw 人炉钢带的质量,kg/h; Cw 0℃至入炉温度间钢带的平均比热容,kJ/(m3。℃);
0℃至基准温度间钢带的平均比热容,kJ/(m3:℃)。
Cwo
7.3.6电气发热元件发出的热量(Qa)计算按下式:
Q=AXN
(8)
式中: Qa—电气发热元件发出的热量,kJ/h(t); A 换算系数,11839.6; N—电热元件的实测有效功率,kW。 注:由于电力是一种二次能源,所以不能简单地与一次能源相比较,本标准采用了通过标准煤来折算的办法,即1度
电折算成0.404kg标准煤,应发出11839.6kJ热量。 7.3.7废气中有机物燃烧的化学热(Q)计算按下式:
Q = VQd
(9)
式中: Qh 废气中有机物燃烧的化学热,kJ/h(t); Vr- 一废气中有机物排放量,可根据每小时(吨钢)消耗的涂料和固体含量比例计算,kg/h(t); Qa—涂料废气的综合低位发热值,kJ/kg
7.4热量支出项目的计算 7. 4. 1 钢带带出的物理热(Q)计算按下式:
Qw = mw(cwt"-Cwoto)
(10)
式中: Qw 钢带带出的物理热,kJ/h(t);
0℃至出炉温度间钢带的平均比热容,kJ/(kg·℃); 0℃至基准温度间钢带的平均比热容,kJ/(kg·℃);
Cw Cwo tw 钢带离开本炉区的出炉温度,℃。
7.4.2 干烟气带出的物理热(Q,)计算按下式:
Q,=V,(1-0.000124gy)(cyty-Coto)
(11)
式中: Q, 干烟气带出的物理热,kJ/h(t); Vy 烟气流量,m/h或m/t; gy 烟气的含水量,g/m; Cy 0℃至排出温度间烟气的平均比热容,kJ/(kg·℃);
48
YB/T4210—2010
20.43e([0. 01(273+tb)]*[0. 01(273+to))
(17)
Qr =
tbto
式中: E一炉体或管道表面的黑度。
7.5热平衡表
热平衡表见附录B 7.6热平衡允许误差
热平衡允许相对误差为±5%,即1△Q/ZQI×100%≤5%。 8热平衡分析 8.1热利用效率(ml)
热利用效率表现了焚烧和固化系统所消耗的热能被钢带所吸收带出的比例,它是系统的综合参数。 根据GB/T2588的规定,计算时不考虑钢带带入的能量,以便直接考察能源有效利用程度。
Qw-Q
n1=Qm+Qw+Qa+Qm
X100%
(18)
8.2热能利用系统的总热能利用效率(m)
为了鼓励将焚烧和固化系统排出的废气所含的热量利用到其他工序,还必须计算系统所消耗的热能中被钢带所吸收以及被其他工序利用的比例。
Q-Qw+Q
h= Q+Qrw+Qd+Qm ×100%
(19)
式中: Q一—系统排出的废气所含的热量利用到其他工序利用部分的总和,kJ/h(t)。
9吨钢耗热指标(Q*)
通过热平衡计算后计算出吨钢耗热指标,包括总体消耗和各个项目的耗热,单位为MJ/t。
50