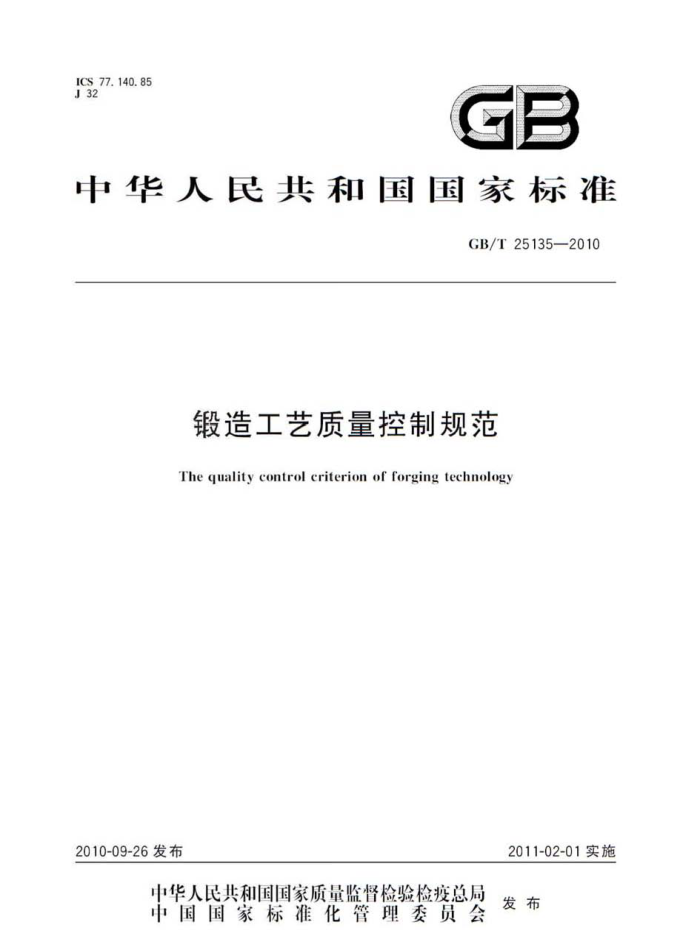
ICS 77.140.85 J32
GB
中华人民共和国国家标准
GB/T251352010
锻造工艺质量控制规范
The quality control criterion of forging technology
2011-02-01实施
2010-09-26发布
中华人民共和国国家质量监督检验检疫总局
中国国家标准化管理委员会 发布
GB/T25135—2010
前言
本标准由全国锻压标准化技术委员会(SAC/TC74)提出并归口本标准起草单位:一汽巴勒特锻造(长春)有限公司、北京机电研究所。 本标准主要起草人:徐长伟、陆东元、金红。
一
GB/T25135—2010
锻造工艺质量控制规范
1范围
本标准规定了模锻件的产品开发以及从原材料到产品交付的工艺过程中,通用的过程控制方法和要求。
本标准适用于锻造企业进行锻造工艺质量的控制。 2规范性引用文件
下列文件中的条款通过本标准的引用而成为本标准的条款,凡是注日期的引用文件,其随后所有的修改单(不包括勘误的内容)或修订版均不适用于本标准;然而,鼓励根据本标准达成协议的各方研究是否可使用这些文件的最新版本。凡是不注日期的引用文件,其最新版本适用于本标准,
GB/T12361 钢质模锻件:通用技术条件 GB/T12362 钢质模锻件公差及机械加工余量 GB/T12363 锻件功能分类 GB/T19000 质量管理体系基础和术语(GB/T19000—2008.ISO9000:2005.IDT) ISO14001环境管理体系要求及使用指南 BSOHSAS18001职业安全和安全管理系统 先要求
3术语和定义
GB/T19000确立的术语和定义适用于本标准。
4锻件分类
本标准质量控制所涉及的锻件分类按GB/T12363执行 5环境和安全的控制
锻造企业的工作环境和职业健康安全应按ISO14001、BSOHSAS18001要求和国家有关规定制定企业具体的实施要求, 6人力资源的控制
锻造企业应确保所有与质量、环境和安全有关的人员能胜任其岗位要求,同时应对人力资源管理的过程进行必要的策划、实施,控制和监督等活动。
-
6.1应针对每个岗位制定岗位规范或岗位描述·内容至少应包括工作内容、职责和权限、任职资格等。 6.2对于法律法规所规定的特殊岗位人员,以及检验员、设备维修维护人员、锻造操作人员、质量管理人员等,应进行必要的培训并获得上岗资格。 6.3应识别所有人员的工作能力,通过员工素质状态矩阵表等形式确定人员的技能状态,为人员的培训、顶岗以及人员的储备提供依据。 6.4新上岗人员要进行必要的岗位培训。 6.5锻造企业应识别关键岗位和核心人员,并通过必要的绩效考评和激励机制来有效配置人力资源。
1
GB/T25135—2010
7生产设备、检验与试验设备及工装的控制
7.1生产设备的控制 7.1.1企业应对设备进行系统管理,使设备始终处手完好状态,满足产品加工质量的要求和安全环保要求。对设备的选型、购置、安装、使用、保养、维修、改造、报废等设备管理全过程要进行控制 7.1.2所用设备应建立档案,其内容至少应包括:设备使用说明书、台时记录、故障记录、修理记录等。 7.1.3要针对设备建立必要的预防性维护和预见性维护体系,确保设备的保养和维护,使设备能力指数Cmk值达到1.33以上。 7.1.4应明确关键设备,并保证关键设备的状态,确保不因设备的状态而影响生产或影响产品的主要质量特性。 7.1.5锻造设备的精度除了应保证静态精度外,动态精度(工作状态下)也应保证。 7.1.6加热设备的温度及测点布置应正确反应加热区炉温及炉温均勾性。 7.2检验设备的控制 7.2.1企业为确保检验设备(包括用手示值的仪器仪表)处手有效的受控状态,应对检验设备的选型、 采购、使用、检定、校准、保养等管理过程实施控制 7.2.2企业应根据产品的质量特性、制造工艺过程要求配备必要的检验设备。检验设备的精度应满足被检测特性精度的要求。 7.2.3各类检验设备应建立台账,内容至少应包括设备使用说明书、制造商、测量范围和精度、编号、使用单位或使用者、检定或校准的部门及周期等。 7.2.4所有的检验设备应有标识,以明确其是否处于可以正常使用的状态。可以用标签来标明其“合格(应包含使用的有效期)”、“封存”、“报废”、“停用”等状态。 7.2.5所有在用的检验设备应保持完好,应有明确的操作规程、检定或校准制度、检定证书或合格证。 7.2.6根据企业的实际情况以及产品的特性要求,必要时应进行测量系统分析(MSA)。 7.3工装的控制 7.3.1企业应确保工装(主要是模具)的技术性能符合要求。应对工装的采购、制造、修复或翻新、库存管理、使用维护、寿命或定额和工装的更改等过程进行管理和控制,以确保工装的质量,使工装满足产品质量的要求 7.3.2企业应对工装的供应商进行系统的、有计划的评审或评价,并实施有效的管理, 7.3.3对新模具应进行必要的检验和测量,确保达到设计、制造要求后方可投人生产。对新模具的首件必须进行全尺寸检验。 7.3.4每套模具应建立必要的档案,内容至少应包括模具号、模具名称、模具的材质、使用单位及设备、 制造的零件号、发出时间、当次生产数量、制造最后一件的锻件质量状态、翻新或修复次数、对模具的处理结论等。 7.3.5根据产品的质量要求和模具的特性.应规定模具的寿命、翻新或修复的次数,必要时应规定强制换模的要求, 8新产品开发的控制 8.1企业应用多方论证的方法来进行新产品的开发工作,成立各相关部门协同工作的项目小组,促使早期识别质量问题而采取预防措施,避免后期更改造成的损失。
锻造企业为确保新产品的开发得以实施,对开发的策划过程、锻件图的设计、工艺过程的设计、试生产、持续改进等过程应进行管理和控制,引导必要的资源实现新产品开发的质量目标,确保早期解决影 2
GB/T25135—2010
响产品质量的因素,使新产品满足顾客要求,达到以低成本及时提供合格产品的目的 8.2通过来自顾客、市场、同行业、经验和有关规定的信息,如:产品图、产品的功能要求、技术协议、标准、特殊要求、合同意向、批量、潜在市场、行业水平、企业内部资源状况等,明确顾客需求
拟定新产品的质量特性、工艺过程和持续改进步骤,通过可行性分析初步确定开发期的质量目标、 量产的质量目标,并以此形成新产品的价格估算。在此基础上确定新产品项目的启动,并制定相应开发进度、质量目标、质量成本和价格等新产品开发计划。 8.3锻件图和工艺过程设计应充分满足产品的质量特性。 8.3.1设计锻件图,锻件图应满足顾客的要求和有关规定的要求,并要得到顾客的签字认可。 8.3.2根据件的质量特性,完善并配备相应的生产设备、检测设备、工装、其他设施和人员 8.3.3根据锻件的特性制定锻件制造的工艺过程.形成流程图。锻件的所有质量特性应在流程中得以实现。整体的工艺流程中包含许多子过程,其中一个子过程或儿个子过程形成一个或儿个产品的质量特性。 8.3.4为确保一个质量特性满足预期的设计要求,就必须对其中的一个或几个子过程进行控制,形成控制计划或质量计划。
a)为了得到满足要求的质量特性,通过对子过程的分析,找出过程中可能出现的变差、不合格倾
向或者使过程不能正常进行的潜在失效模式。 b)通过对这些变差、倾向或潜在失效模式的分析,找出降低、减少或杜绝其风险的措施:这些措
施包据括:必要的检验和试验、监视、测量、统计技术、操作流程、特殊的设备、检测设备或装置、 应急计划、包装和防护等
c) 把这此控制措施编制在流程中.形成控制计划文件 d)必要时,控制计划要得到顾客的批准,
8.3.5根据控制计划编制相应的作业文件、检验文件,设计相应的模具图、其他工艺装备,以及提出相应的要求或需求。 8.3.6根据完成的锻件图、工艺过程和相应的技术文件,规定制造过程所能达到的生产率、过程能力、 成本目标和质量目标。 8.3.7必要时,在锻件图和工艺过程的设计中应采用防错技术、潜在失效模式分析(FMEA)、统计过程控制(SPC)和测量系统分析(MSA)等手段。 8.3.8根据设计的工艺流程生产样件并对样件进行全尺寸检验和功能试验:合格的样件交付给顾客,由顾客进行必要的检验和试验、加工等,以确认开发的产品是否符合预期的质量要求。所有验证过程发现的质量信息应及时反馈到项目小组,以便于对开发过程进行改进, 8.4样件合格后,经过对工艺过程、控制计划适当的改进,并进行小批量生产验证生产能力和综合保证能力。小批量样件和首批批量件应向顾客交付必要的检验报告。顾客要求时应按照生产件批准程序 (PPAP)进行操作。 8.5对于开始大批量生产的产品,要收集大量的质量信息,通过持续改进完善产品和工艺过程,使产品和交付过程达到顾客满意 9原材料的控制 9.1锻件用原材料应有供方提供的"质量保证书”,并符合工艺文件规定的材料牌号、尺寸规格、性能等要求。 9.2原材料进厂后需经材料检验部门复检。复检的项目或内容、数量和频次,根据顾客要求、原材料的特点、批量以及供方的质量信誉状态等综合决定,
3
GB/T25135—2010
9.3合格料、待检料、不合格料及待处理料应有明显的标识。 9.4合格料的入库、出库必须有严格的管理制度和复检制度,同时应遵循“先进先出”的原则。 9.5原材料的存放应严格按照原材料冶治炼炉批次号进行隔离存放,以避免相同材料的不同炉批号原材料、相同尺寸规格的不同原材料的混滑而产生的混料事敌
10文件与记录的控制
10.1工艺技术文件
锻件的生产过程应有锻件图、流程图、工装图、技术标准、设备/仪器操作规程、作业指导书、工艺规
程、控制计划、检验指导书等技术文件。 10.2技术文件要求 10.2.1技术文件内容的表达要准确、简明、通俗易懂且有逻辑性,并应符合标准化的要求,各种技术文件必须统一、完整,并维持其有效性。 10.2.2编制的所有技术文件必须确保其可操作性。 10.2.3所有的技术文件均应按规定的程序审批签字后,方能生效一技术文件如有更改,其审批程序与
原文件的审批程序相同, 低 10.2.4所有技术文件均应分类存档,并有严格的发放制度,确保每个岗位获得必要的、有效版本的技术文件。失效或已被更新的技术文件或资料应销毁或作出明确的标识,以避免这些文件的非预期性使用。
C
WWDZTXK
10.3记录 10.3.1 过程数据、工艺参数和检测报告等原始记录都应做为质量记录而归档备查,并为有追潮性的场合提供证据。 10.3.2质量记录保存期视顾客的要求和锻件的重要程度而定。应确保质量记录的保存环境。 10.3.3应确保质量记录的有效性、完整性和可检索性。
11生产过程的控制 11.1下料 11.1.1下料前应根据工艺规程、操作文件核实材料牌号、规格、数量、熔炼炉(批)号。并检查表面质量,有要求时,还应检查头部标记, 11.1.2下料必须接照锻件号、材料牌号、熔炼炉(批)号分批进行,并在流转卡上注明下料数量。如遇材料代用,必须严格按材料代用制度的规定办理代用手续后,方可下料 11.1.3下料时.应严格执行“三检制度”(自检、互检和专检)。检验合格并作出明显标记后方可投入生产。 11. 1, 4 环料的重量、尺寸公差、表面及端面质量,应符合工艺要求 11.1.5 5下料过程中,如发现坏料有肉眼可见的缺陷时,应隔离并报告相关人员处理。 11.1.6 6下料场地应保持整洁。应按材料牌号、熔炼炉(批)号、规格尺寸分别放置,下好的坏料应装箱)架管理,复检合格并做好标识,不得混料。 11.1.7剩余原材料应标明材料牌号和熔炼炉(批)号,并及时退给原材料库,由原材料库严格分类管理。 11.2加热 11.2.1坏料加热前应检查材料牌号、熔炼炉(批)号、规格尺寸是否与工艺要求相符 11.2.2坏料装炉前必须清除炉膛内的杂物。在电炉中加热的坏料表面不得沾染油污。
GB/T25135—2010
11.2.3坏料人炉时,应放在工作区内,为保证坏料加热均匀,大型坏料应加垫块,坏料之间应有一定的间距,必要时,应有序排放。 11.2.4火焰炉加热时,不允许火焰直接喷射在坏料表面。 11.2.5电炉加热时,坏料应与发热元件保持一定距离,或采取屏蔽措施防止坏料过烧。 11.2.6对于精锻件坏料的加热,应采用无氧化或少氧化加热方法 11.2.7坏料加热温度、加热时间及重复加热的次数应按相应锻件的工艺规程要求进行。 11.2.8坏料加热时,氧化皮的厚度、脱碳层深度应符合锻件工艺要求,坏料加热不允许产生过热、过烧和内部裂纹等现象,坏料因故不能按时锻造,可采取降温或出炉等方法处理,但必须符合工艺规程的要求。 11.2.9 相同加热规范的不同坏料同炉加热时,在炉内必须分区放置,严禁混料。 11.2.10不同加热规范的材料不得同炉加热, 11.2.11对于采用余热正火、余热退火或余热率火工艺的,应有严格的加热控制措施,必要时加热设备应有闭环的温控装置或手段 11.2.12加热不同类型合金的注意事项
a)加热过铜合金的设备,应先进行除铜清理后,方可对钢坏及其他合金进行加热: b) 加热铝合金坏料时,炉内气氛不充许含硫和含水蒸气: e) 加热钛合金坏料时,炉内不充许有还原性气氛。
11.3锻造 11.3.1 根据锻件的材料、形状、尺寸及工艺要求选择相应的锻造设备。锻件必须在工艺文件指定的设备上进行锻造。 11.3.2锻造前操作人员应熟悉指导锻造操作的各类工艺文件。 11.3.3 锻造前所用模具或设备等必须采用正确的方法预热至规定的温度。 11.3.4 根据锻件复杂程度、材料和工艺要求,选用合适的润滑剂。 11.3.5 坏料在锻造前及锻造过程中应注意去除氧化皮 11.3.6 锻造时,必须严格控制始锻温度、终锻温度。必要时对始锻温度、终锻温度采用温控设施 11.3.7 锻造操作过程中·必须严格按照工艺规程和操作文件进行。并随时注意坏料变形是否正常,如发现折叠、充不满、裂纹等缺陷,必须采用适当方法加以清除,在不影响锻件质量情况下方可维继续锻造。 11.3.8锻件的切边、冲孔、校正温度应根据锻件工艺规程的有关规定进行。 11.3.9锻件的冷却,应按锻件工艺规程规定的冷却方法进行。对于采用余热淬火的锻件应严格控制进入淬火介质前的温度 11.3.10工、Ⅱ类锻件,必要时应提出专用工艺说明书,并应进行初始生产工艺、工装的试验,验证合格后方可投入生产,I、Ⅱ类锻件应按锻件图号,建立质量档案。 11.3.11为保证产品的可追溯性,应在锻件上生成永久性标识。 11.4锻件的热处理 11.4.1锻件的热处理通常采用率火、正火、退火、回火等热处理方式 11.4.2热处理设备应确保加热温度的准确,同时应确保炉温的均匀性,必要时应有自动控温系统。应严格控制热处理的加热温度和时间避免超过工艺要求的氧化脱碳 11.4.3热处理过程中至少应控制温度、盘/炉装量、推料/加热周期、冷却介质的温度和运动状态等工艺参数。 11.4.4应严格按照工艺要求进行热处理过程和热处理后的检验和试验,
5
GB/T25135—2010
11.4.5热处理前应检验锻件的质量状态,发现锻件有缺陷要及时处理。 11.4.6未热处理、已经热处理待检、热处理后合格和热处理不合格件应严格分区存放。 11.5锻件后序处理 11.5.1清理 11.5.1.1锻件表面应按工艺要求进行清理。清理后的锻件表面质量应符合技术文件要求。 11.5.1.2锻件表面缺陷允许清理打磨,通常加工表面的打磨深度不允许超过加工余量的1/2;非加工表面的打磨深度不允许超过锻件的表面缺陷深度,且打磨的宽度要在深度的6倍以上。 11.5.1.3有些锻件需要进行冷校正。冷校正过程应避免局部变形过大及过大的冷作硬化,冷校正后的锻件应采用适当的热处理来消除内部应力。 11.6锻件检验 11.6.1锻造的首件必须进行检验,且应有单独的人员或班组对锻造的首件进行全尺寸检验。必要时要进行功能试验。 11.6.2在生产过程中,应按照工艺文件要求对锻件的相关的质量特性进行检验。必要时生产过程应配置专业的检验人员。 11.6.3根据产品和工艺过程的实际情况,必要时在生产过程中应特殊配置磁粉探伤、超声探伤等检验手段。 11.6.4号 锻件(或坏料)在转序前要进行必要的质量确认,并留下相应的记录, 11.6.5锻件终检应按检验文件、锻件图、GB/T12361、GB/T12362等有关规定进行。 11.6.6所有产品都应做出相应检验状态标识·并按检验状态分区存放。通常检验状态分四种:待检品、合格品、不合格品和待处理品,无法确认检验状态的产品或可疑产品应归为不合格品。 11.6.7企业应对不合格品进行控制和管理,以防正不合格品的非预期使用。应制定不合格品控制文件以使于不合格品的处理。经确认为不合格的锻件,应做出明确的标识隔离存放,并交检验人员或工艺人员处理 11.6.8生产过程中,发现质量问题,应立即停止生产并及时组织分析,找出根本原因并实施纠正和预防措施,并经生产验证确认产品合格后方可恢复生产。 11.6.9通常情况下,企业的检验方式应遵循“双三检制(专检、自检、互检相结合,首件检验、序间巡检、最后检验相结合,两种检验方式交叉进行)。检验后应保留必要的检验记录。 11.6.10锻造企业应该配置有一定检验和试验范围的试验室,其检验能力应包括原材料检验、化学成分、硬度、金相、金属的力学性能等。 11.6.11对于尺寸检验,可采用传统的划线检验方法,也可采用三座标测量机、轮廊仪、测高仪等专用的测量仪器。 11.7统计技术
生产过程中对于工艺过程数据、相关/重要/特殊的质量特性应进行必要的监控和记录,对相关数据要进行统计和分析(统计过程控制SPC),以便于过程异常能被及时发现并调整,持续改进产品和过程。 11.8合格证
经检验合格的锻件应由检验人员签发合格证,合格证应与锻件一起交付给顾客,必要时应向顾客提供相关原始检验记录或其他约定的证明文件, 11.9产品的交付 11.9.1企业应按照与顾客的约定,按时把产品交付给顾客。产品交付前要进行必要的审核,内容应包括核对品种和数量、产品的表面状态、产品是否存在失效、包装和防护的要求等。 11.9.2锻件的交付应本着“先进先出”的原则。 6