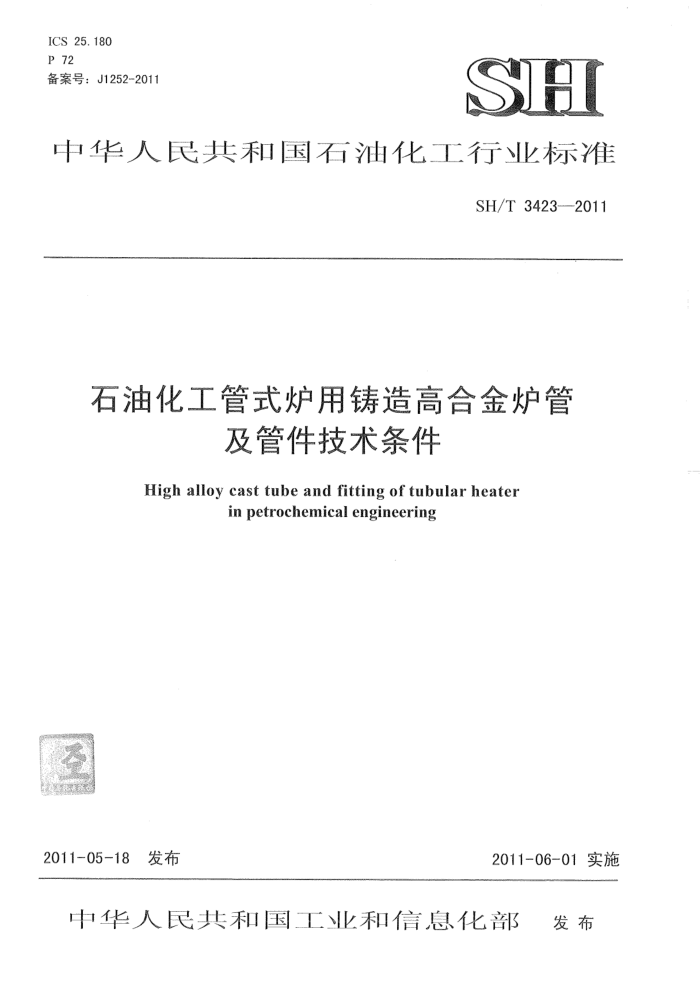
ICS 25.180 P 72 备案号:J1252-2011
SH
中华人民共和国石油化工行业标准
SH/T 3423-—2011
石油化工管式炉用铸造高合金炉管
及管件技术条件
High alloy cast tube and fitting of tubular heater
in petrochemical engineering
2011-05-18 发布
2011-06-01实施
中华人民共和国工业和信息化部 发布
SH/T 3423--2011
目 次
前言 1 范围· 2规范性引用文件· 3材料 3.1化学成分· "3.2力学性能 3.3低倍组织 4制造要求 4.1 制造· 4.2 交货状态 4. 3 尺寸极限偏差 4.4 粗糙度 4.5 焊接· 4.6 外观质量? 4.7 缺陷的修补 4.8热处理· 5 试验方法和检验规则 5. 1 化学成分分析· 5.2 力学性能试验· 5. 3 管段的金相酸蚀试验 5.4 复验· 5.5 外观和尺寸检查 5.6 无损检测 5.7 水压试验 5.8 证实性材料鉴定(PMI) 6 监造
标志、包装、运输和贮存· 7. 1 标志· 7.2 包装 7.3运输· 7.4贮存附录A(资料性附录)高温短时力学性能附录B(资料性附录)产品化学成分允许偏差用词说明附:条文说明·
7
....9
10
11 13 15
SH/T3423-2011
前言
根据国家发展和改革委员会办公厅《2007年行业标准修订、制定计划》(发改办工业[2007]1415 号)的要求,标准编制组经广泛调查研究,认真总结实践经验,参考有关国际标准和国外先进标准,并在广泛征求意见的基础上,制定本标准。
本标准共分7章和2个附录。 本标准的主要技术内容是:石油化工管式炉用铸造高合金炉管及管件的材料、制造、检验、标志
和包装等方面的要求。
本标准由中国石油化工集团公司负责管理,由中国石油化工集团公司设备设计技术中心站负责日常管理,由中国石化工程建设公司负责具体技术内容的解释。执行过程中如有意见和建议,请寄送日常管理单位和主编单位。
本标准日常管理单位:中国石油化工集团公司设备设计技术中心站
通讯地址:北京市朝阳区安慧北里安园21号邮政编码:100101 电话:010-84877587 传 真:010-84878856
本标准主编单位:中国石化工程建设公司
通讯地址:北京市朝阳区安慧北里安园21号邮政编码:100101
本标准主要起草人员:胡鸣 李文辉 孙向军 袁慕军艾国孙毅本标准主要审查人员:张海燕 钱峰学 韦有前 王洪军 王久征 夏毓芳端木传芳 程贵昌
李建中 何明胜 何纪海 向林
本标准为首次发布。
II
SH/T 3423-2011
石油化工管式炉用铸造高合金炉管及管件技术条件
1范围
本标准规定了石油化工管式炉用材料为25Cr-20Ni(HK40)及其以上级别高合金铸造炉管及管件的材料、制造、检验、标志、包装、运输和贮存等要求。
本标准适用于石油化工管式炉用合金含量在18Cr-10Ni-Nb及合金含量更高级别的离心铸造合金炉管和静态铸造合金管件。 2规范性引用文件
下列文件中的条款通过本标准的引用而成为本标准的条款。凡是注日期的引用文件,其随后所有的修改单(不包括勘误的内容)或修订版均不适用于本标准,然而,鼓励根据本标准达成协议的各方研究是否可使用这些文件的最新版本。凡是不注日期的引用文件,其最新版适用于本标准。
GB/T223钢铁及合金化学分析方法 GB/T226 钢的低倍组织及缺陷酸蚀试验法 GB/T228 金属材料室温拉伸试验方法 GB/T1804-2000 一般公差未注公差的线性和角度尺寸的公差 GB/T2039 金属拉伸蠕变及持久试验方法 GB/T 4338 金属材料高温拉伸试验方法 GB/T 5677 铸钢件射线照相检测 GB/T6060.1 表面粗糙度比较样块·铸造表面 GB/T6060.2 表面粗糙度比较样块、磨、车、镗、铣、插及刨加工表面 GB/T 6414--1999 铸件尺寸公差与机械机加工余量 GB/T9443--2007 铸钢件渗透检测 SH/T3037--2002 炼油厂加热炉炉管壁厚计算 SH/T3417-—2007 石油化工管式炉高合金炉管焊接工程技术条件 JB/T4730.2--2005 承压设备无损检测第2部分:射线检测 JB/T4730.5--2005 承压设备无损检测第5部分:渗透检测 JB/T4730.6承压设备无损检测第6部分:涡流检测 ASME Boiler And Pressure Vessel Code II Part D-Properties Materials
3材料 3.1 化学成分
炉管和管件的化学成分应符合表1的规定。若买方对化学成分另有要求,则应符合买方的要求。
表11 化学成分
%(质量分数) Mo 其他
序 公称成分
c 0. 08 0.35~0.45 0.5~2.0 1. 5 23~27 19~22
Si 2.0 1. 5 18~21 9~12
Mn
Nb
Cr
Ni
P
号 1 2 3 20Cr-32NiNb 0. 08 ~ 0.16b 1. 5 1. 5 18~22 30~34 10.8~1.6b 0.03 0.030.5
S
0. 04 0.040.5 0. 04 0.040.5
18Cr-10Ni-Nb 25Cr-20Ni
SH/T3423—2011
表1(续) 化学成分 Si
%(质量分数)
序 公称成分
C
Mn
Nb
其他 d
Cr
Ni
P
Mo
号 3 5 35Cr-45Ni-Nb 0.420.6 11:002.0 11.01.5 33~ ~37 43~48+06~1 8 0. 03 0.03 30.5 d
0.35~0.45 2.0 1.0~1.5 23~27 34~ 87 0.81.5c 0. 03 0. 03 30.5
25Cr~35Ni~Nb
F
W: 4~6 C: 13~17
55 05~2.00.5~1.5 124- ~28 34~38
26Cr-36Ni-15Co-5W
0.03 0.030.5
A
6
注:表中除给出范润的值外均为最大值 a不少于8倍的含量,直不超过1% b Nb/C>8 制造商可根据其经验调整。
C
d
Ti、Z等微量壳素的含量由买卖双方协商确定
3.2力学性能 3.2.1 炉管和管件的常温力学性能应符合表2的规定
表2 常温力学性能抗拉强度R
S
伸长 ML4D
蒙用服强度R
序号
公称成分
MPa >485 425 440 440 440 ≥480
MPa 205 ¥240 17: ¥240 240 310
?
1
18Cr-10NiNb 25Cr-20Ni 20Cr-32Ni-Nb 25Cr35NiNb 5Cr-45Ni-Nb
2 3 N 5 6
25 8 梦5
26C -36Ni-15Co-5W
3.2.2 管的高温持久力学性能应符合表3的规定。不应采用热处理的方法来改善试样的抗变性能,但试样在试验前可以在试验温度下进行24h时效
O 1f00℃
表3 高温持久力学性能
最小 断裂时间 980.C
序
号 公斋 1 25Cr-2QNi 2 20Cr-32NiNb 3 25Cr35Ni-Nb 5 26Cr-36Ni-15Co-5W 注:带“*”符号者只针对如入微量危素以提高抗渗碳和抗端变性能材料(
950℃
870℃ 9000 69MPa JOMPa 40MPa35MPa/48MPa 41MPa30MPa25MPa 25MPa 20MPa 17MPa 16MPa 25
1000%
成分
1050℃
20
100*
95
95
35
35Cr-45NiNh
4
100°
55
1of
制造商应提供炉管材料的高温断裂许用应力曲线。25er2oNi材料的高温断裂应力应符合
3.2.3 SH/T3037-2002中附录E图E.19的要求。 3.2.418Cr-10Ni-Nb材料的最大许用应力值应按ASME第II卷D篇的有关规定选取。 3.2.5当买方对材料的高温短时力学性能有要求时,买方应规定试验温度,其指标应由买方和卖方协
2
SH/T3423--2011
商确定。如未规定温度,试验应在870℃(或800℃)温度下进行。不应采用热处理的方法来改善试样的热拉伸性能,但试样在试验前可以在试验温度下进行24小时时效。附录A中的数值可用作参考。 3.3低倍组织 3.3.1炉管的铸态外表面粗糙层厚度应不大于0.8mm。 3.3.2炉管断面的最小密实层厚度应符合买方要求。密实层厚度为铸造壁厚减去外表面粗糙层和内表面疏松层之后的厚度 3.3.3炉管断面最小密卖层低倍组织在任意情况下其结构基本上应是同心的, 买方对柱状晶的比例
。
应在订货合回中协商确定。
有特殊要求,
4制造要求 4.1制造 4.1.1 原材料的熔炼应采用电弧炉或感应炉。原材料宜为新料,不得采用使用过的废旧炉管和其他铸件。如果采用成分相当的回炉料,其比例应得到买方的书面同意。如果买方要求采用特殊台炼方法应
在订货合同中注期。
管段应用金属模离心铸造而成。管段冷、热两端应各切除至少100mm,再根据需要焊接成
4.1.2 炉管可根据卖方要求,以管段或组焊成炉管的形式交货。 4.1.3除另有规定外,组焊炉管的焊接接头数量应符合下面的规定
J O
a)炉管的全长小于等于10m时,最多3个: b)直焕管的全长大于10m时,最多4个。
4.14炉管中仅允许有一根长度小于2m的管段,且该管段的长度不得小于1.2m, 组焊位置应放在炉管的端部。 4.15庐管内、外壁机加工时,炉管内壁机加工的金属切削量不得小于1.2mm, 应确保表面上的疏
松房被切掉:外壁机加工的金属切削量不得小手0.8mm 4.16 季件应采用树脂砂或失蜡法静态铸造 4.17(除男有规定外,管件的铸造障厚可根据铸造工艺要求在设计最小铸造壁厚(MCW 的基础上增厚 但增厚量不得大于MCW的25%。 4.1.8 管件内部通道剖面为变截面者应逐渐平滑过渡
m
因铸造工艺技术的限制而要求对管件设计做改动时,应经买方书面同意后方可制造管件内外表面应清理十净,不得有粘砂、夹清、裂纹及机械伤痕等缺陷。着上逐缺陷存在时,
4.1.9 4.1.10
允许修磨 修磨处与未修磨部位应平滑过渡,且修磨后的壁厚应不小手设计要求的最小壁厚,否则应予补焊。
除图样男有规定外,炉管及管件的焊接坡口及附近25mm区域内应进行内外表面机械加工。
4.1.11 相焊件坡口处的内壁错边量应符合SH/T3417-2007的有关规定。机加工表面与铸态表面应光滑过渡,锥度不宜超过1:4
4.1.12炉管和管件在制造、加工、试验、检验等过程中,均应进行标记移髓, 标记移植所用的墨水成分不得含Sn、pb、 nS.CI等对炉管和管件有害的元素。 4.2交货状态 4.2.1根据买方要求,炉管可以有下三种交货状态:
SSE
内、外壁均经机械加真: b) 外壁为铸态,内壁经机械加工; c). 内、外壁均为铸态。
a)
4.2.2 管件坡口处应机械加工,除另有规定外,管件均以铸态交货。 4.2.3 如果买方对交货状态有其他要求时,应在订货合同中注明。
3
SH/T3423-—2011
4.3 尺寸极限偏差 4.3.1 管段内外表面均进行机械加工的公差应符合以下规定:
外径极限偏差:+1mm; b) 内径极限偏差:-1.0mm; c) 同截面上壁厚极限偏差:最小壁厚的10%或1.0mm(取最大值)。
a)
0
4.3.2 管段外表面为铸态,内表面进行机械加工的公差应符合以下规定:
a) 外径极限偏差应不大于表4中的规定值; b) 内径极限偏差:-1.0mm;
c) 同截面上壁厚极限偏差:+1.0 0mm(外径≥100mm);
-0.8
8mm(外径<100mm)。
单位:mm
表4铸态外径极限偏差
炉管外径 50~100 >100~300 >300~600
外径的正偏差
1.6 2. 0 3. 0
4.3.3 管段内外表面均不进行机械加工,以铸态交货的公差
铸态壁厚为密实层厚度加上为了保证最小密实层壁厚(设计要求值)的内径裕量和外表面粗糙层厚度,且铸态壁厚偏差应满足表5的规定,不允许有负偏差。
单位:mm
表5铸态壁厚极限偏差
炉管外径 50~100 >100~300 >300~600
铸态壁厚的正偏差
2. 0 2. 5 3. 3
4.3.4 管段的其他要求应按以下规定:
a) 机加工管段圆度偏差为壁厚的5%: b) 直线度为任意1m长度内不大于1.0mm。
4.3.5 炉管的直线度为任意1m长度内不大于1.0mm,且炉管的长度不超过6m时,全长直线度应不大于4.0mm;长度大于6m小于10m时,全长直线度应不大于6.0mm;长度超过10m时,全长直线度应不大于8.0mm。 4.3.6炉管的长度极限偏差应符合表6。
表6炉管的长度极限偏差
炉管总长L,m
长度极限偏差,mm
3° +6. 0 +10. 0
L<6
6≤L<10
0
L≥10
0
4.3.7管件的形状和尺寸应符合设计文件的规定。如无特殊要求,管件的尺寸公差应符合GB/T6414 1999的规定。 4.3.8除另有规定外,管件不加工表面的尺寸公差应符合GB/T6414一1999中的CT10级精度规定。 4
SH/T3423-2011
4.3.9机加工表面的加工余量由制造商根据加工精度和粗糙度的要求确定。 4.3.10管件机加工未注明的尺寸公差应符合GB/T1804--2000中公差等级为中等m级的规定。 4.4粗糙度 4.4.1炉管内壁机加工表面粗糙度应不低于R.3.2um。 4.4.2除另有规定外,焊接坡口处机加工表面粗糙度应不低于R.6.3um 4.4.3管件不加工表面粗糙度应不低于R,12.5um。 4.5焊接 4.5.1炉管和管件的焊接工艺评定、焊材选用、焊接质量、检查和验收等要求应符合SH/T3417的规定。 4.5.2焊接时不得使用衬环等衬垫。 4.6外观质量 4.6.12 炉管和管件不加工的外表面应进行喷石英砂或喷不锈钢丸处理,不得采用喷铁丸或用碳钢丝清理。 4.6.2对外表面不加工的炉管,其外表面应呈现均匀分布的杨梅粒子状态。 4.6.3 炉管表面不得有气孔、缩孔、砂眼、裂纹等缺陷。 4.6.4管件内外表面应光洁,不得有裂纹、冷隔、夹砂和夹渣等铸造缺陷。 4.6.5管件的浇冒口切割应平整,无裂纹。经表面处理后,不得有多肉、飞边、粘砂等影响外观质量的缺陷。缺肉深度不得深入到规定的最小壁厚。 4.6.6焊接接头的表面质量应符合SH/T3417--2007中6.3条的规定。 4.7缺陷的修补 4.7.1管段的铸造缺陷不得焊补。 4.7.2管段水压试验时发现的渗漏缺陷不得焊补。 4.7.3除4.7.8条规定的缺陷外,管件上的其他缺陷允许焊补,焊补金属应与铸件相同或相近。 4.7.4大面积焊补应征得买方书面同意。焊补缺陷的挖槽深度大于壁厚的20%,或挖槽面积大于65cm 时均属大面积焊补。 4.7.5管件焊补前,应把缺陷清除干净,经铲凿、打磨或其他机加工方法露出密实金属表面,要焊补的边缘和靠近边缘的部位应彻底清除掉所有的污物,如油、涂料、低熔点金属、氧化物、水分等。 4.7.6管件同一部位的焊补次数不得超过两次。 4.7.7 管件焊补后应将焊补部位打磨,使其与本体平滑过渡,并经渗透检测合格。 4.7.8 管件有下列情况之--时,不得进行焊补:
a)成品试压渗漏的缺陷; b)成片疏松或密集气孔; c) 设计文件规定不允许焊补的缺陷。
4.7.9 存在超标缺陷的焊接接头应进行修补。焊接接头修补应符合SH/T34172007中6.4条的规定。 4.7.10 焊接接头同一位置的修补次数不得超过两次。 4.8热处理
18Cr-10Ni-Nb材质的管件应进行固溶处理(最低温度为1065℃)。管件补焊后应再次进行固溶处理。除另有规定外,其他材质的管段、炉管、焊接接头和管件均不需要进行热处理。 5试验方法和检验规则 5.1化学成分分析 5.1.1每炉钢水浇注前,应从钢包中取样。当两炉或两炉以上的钢液合在--个钢包浇注时视为一炉,允许在成品上取样。 5.1.2化学成分分析采用定量光谱仪进行分析。
5