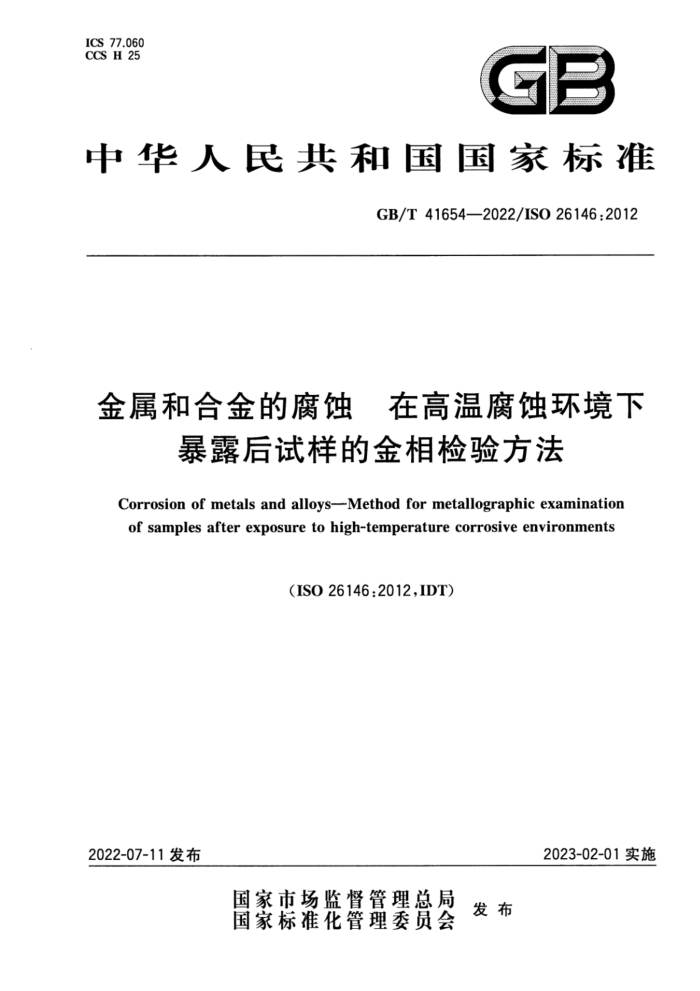
ICS 77.060 CCS H 25
C
中华人民共和国国家标准
GB/T41654—2022/ISO26146:2012
金属和合金的腐蚀 在高温腐蚀环境下
暴露后试样的金相检验方法
Corrosion of metals and alloys-Method for metallographic examination of samples after exposure to high-temperature corrosive environments
(ISO26146:2012,IDT)
2023-02-01实施
2022-07-11发布
国家市场监督管理总局
国家标准化管理委员会 发布
GB/T41654—2022/ISO26146:2012
前言
本文件按照GB/T1.1一2020《标准化工作导则 」第1部分:标准化文件的结构和起草规则》的规定起草。
本文件等同采用ISO26146:2012《金属和合金的腐蚀 出在高温腐蚀环境下暴露后试样的金相检验方法》。
请注意本文件的某些内容可能涉及专利。本文件的发布机构不承担识别专利的责任。 本文件由中国钢铁工业协会提出。 本文件由全国钢标准化技术委员会(SAC/TC183)归口。 本文件起草单位:中国航发北京航空材料研究院、冶金工业信息标准研究院。 本文件主要起草人:张欢欢、张晓云、侯捷、田子健、李倩。
1
GB/T41654—2022/ISO26146:2012
金属和合金的腐蚀在高温腐蚀环境下
暴露后试样的金相检验方法
1范围
本文件适用于在高温腐蚀环境下暴露后试样的金相检验。 本文件规定了在高温腐蚀环境下暴露后试样形成的腐蚀层的分类、识别和厚度测量方法。
2规范性引用文件
下列文件中的内容通过文中的规范性引用而构成本文件必不可少的条款。其中,注日期的引用文件,仅该日期对应的版本适用于本文件;不注日期的引用文件,其最新版本(包括所有的修改单)适用于本文件。
ISO3611产品几何技术规范(GPS)尺寸测量设备:外部测量用千分尺设计和计量特征[Ge0 metrical product specifications (GPS)—Dimensional measuring equipment:Micrometers for external measurements—Designandmetrologicalcharacteristics
ISO13385-1产品几何技术规范(GPS)尺寸测量设备第1部分:两脚规的设计和计量特征 [Geometrical product specifications(GPS)—Dimensional measuring equipment—Part1:Design and metrological characteristics of callipers
3术语和定义
下列术语和定义适用于本文件。 注:图1为暴露后的试样中各层的图示。
6
a) 无涂层
b)有涂层
标引序号说明:
基体;去合金化区域:
沉积物;
5
7.
-
6- -互扩散区;
2
涂层。
o - 内腐蚀产物;
7- -
外部腐蚀层;
图1腐蚀后试样中需测量的各层的示意图
-
GB/T41654—2022/ISO26146:2012
3.1
金属初始表面originalmetalsurface 涂覆涂层或暴露于腐蚀环境前金属试样的表面。
3.2
涂层初始表面originalcoatingsurface 最终处理后,暴露于腐蚀环境前的涂层表面。
3.3
互扩散区 区interdiffusionzone 在涂层和基体初始界面附近的区域,在暴露过程中,该区域涂层和基体的化学成分因扩散发生
变化。 3.4
沉积物deposit 在暴露前和/或暴露过程中与试样表面接触或沉积在试样表面的化学活性液体或固体物质。 示例:盐、飞尘、焦化物和熔融金属。
3.5
沉积物厚度depositthickness 垂直于试样表面的法线方向腐蚀产物外表面和沉积物层表面之间的距离。
3.6
涂层coating 用于金属材料表面的起防护作用的一层材料。
3.7
涂层厚度coatingthickness 垂直于试样表面的法线方向上金属初始表面和涂层表面之间的距离。
3.8
向外生长的腐蚀层 outwardgrowingcorrosionscale 从金属或涂层初始表面向外生长的腐蚀层。
3.9
向内生长的腐蚀层 inwardgrowingcorrosionscale 从金属或涂层初始表面向内生长的腐蚀层。
3.10
外部腐蚀层 externalscale 向内生长和向外生长的连续腐蚀层的总称。
3.11
内腐蚀产物 internal corrosion 在外部腐蚀层以下形成的腐蚀产物。 注:一般显示为不连续颗粒物。
3.12
晶界腐蚀 grainboundarycorrosion 腐蚀产物沿金属晶界生长,是内腐蚀的一种特殊形式。
3.13
去合金化区域 de-alloyedzone 在腐蚀层以下的,形成腐蚀层的合金元素浓度降低的区域。 注:可能表现为显微组织中原有沉淀物的溶解。 2
GB/T41654—2022/ISO26146:2012
3.14
金属损失metalloss 试样初始表面和试样中合金不受影响区域的边界之间的距离。
3.15
剩余完好金属 remaining soundmetal 金属中未受腐蚀影响的部分。
4 符号和缩略语
4.1 符号
下列符号适用于本文件:
每一层的厚度;
t 金属材料厚度。 4.2 2用于脚注的缩略语
每一层的标识采用如下脚注: 0
初始;
og 外腐蚀层向外生长的部分;
外腐蚀层向内生长的部分;
ig tot 外腐蚀层总厚度(tot=工十); in 内腐蚀; gb 晶界腐蚀;
沉积物;涂层;去合金化;
d c da ml 与初始尺寸相比的金属损失; rm 剩余完好金属。
5要求
5.1 测试精度的最低要求是达到95%置信度时,被测材料损失不超过士5μm或5%。而该不确定度是对校准、不重合度(在垂直和水平两个方向上)和测量等误差要求的最小值。 5.2测试采用的光学显微镜应具有能在X-Y轴方向移动的载物台或具有计数线、十字交叉线。测试系统的精度应达到士1μm。 5.3测试系统至少每12个月校验一次,校验应包含正交性与规定长度标准的符合性。系统在每次系列测试前和测试后按二级标准检查。
6测试方法
6.1试样 6.1.1试样的尺寸和形状宜根据从各供应商处获得的材料的类型和形状确定。例如,锻造产品(棒材、 板材、带材)或铸造产品(不同形状的棒材)。
3
GB/T416542022/ISO26146:2012
6.1.2为便于测量和减少误差,推荐采用棒状、盘状或块状三种基本形状的试样。 6.1.3机加工公差一般宜不低于士0.05mm,但对于大尺寸试样,机加工公差的要求可以适当放宽。 6.1.4实验室暴露试验用试样一般不作基准标识,但对于特殊情况或其他暴露试验,如工厂用试样等,试样可具有足以保证暴露试验前后在测试平面内确定特定点位置的基准位置。基准标识作为基准点,用于确保在试样的相同位置进行重复测试,可以通过采用基准标识和基准槽来实现。基准标识和基准精根据试样的几何尺寸变化。块状试样的基准标识和基准槽见图2,其他几何尺寸的试样可采用类似的标识和槽。
-
2
标引序号说明: 1-—基准标识; 2——基准槽。
图2块状试样基准标识示例
6.2试验过程 6.2.1暴露试验前的检查
在暴露试验前,应采用符合ISO3611和ISO13385-1规定,且测量精度为士0.02mm的测量仪器测量未腐蚀试样的尺寸。在暴露试验后待测量的区域内宜选择不少于8个等距离的位置进行尺寸测量。
尺寸测量结果是金属初始表面特征表征的基础。 6.2.2横截面金相试样的制备
应制备横截面金相试样确定暴露试验后试样的尺寸变化。制备横截面金相试样时宜非常小心,确
保沿着平行于待测量的横截面进行镶样和抛光,且保留所有腐蚀产物和沉积物。推荐横截面金相试样的制备方法如下。
应采用合适的涂层对试样进行保护,以确保能保留试样上的腐蚀产物和沉积物。根据测试的试样体系,可采用沉积法制备的金属涂层或热塑性树脂。
镶样模具中可能会需要试样支撑物,以确保截面保持一个平面。 试样在镶样前后切割均可。棒状和管状试样宜沿着垂直于主轴线方向切割成环形横截面;盘状试
样宜平行于主轴线方向切割;块体试样宜沿平行于最长面的方向切割。切割的细节要求详见图3。
若要求露出与基准标识表面有关的特定平面的横截面,宜在距离该表面足够远的平面进行切割,以便为研磨和抛光留有足够的去除量(见图3)。
镶样时宜使用一个或多个已知尺寸的人工样品作基准,以证明试样被沿着平行于预期横截面的方向进行镶样和抛光。扁平试样(盘状和方形结构)可以一起镶样,采用厚度恒定并已知(土1μm)的金属薄片沿着平行于试样的方向固定紧。棒状试样可采用一个类似的、厚度已知的、被弯曲成已知角度(推
4
GB/T41654—2022/ISO26146:2012
荐90°)的金属薄片,将试样放在金属薄片弯曲角处。也可以在镶样时采用在试样周围放置多个球状物的替代方法。使用基准人工样品检查抛光时的对准情况的示意图见图4。
标引序号说明:
截面切割线;基准槽。
1
2
图3 有基准标识的试样的截面切割步骤
a) 合格的试样制备
b) 偏离的试样制备(大于人工样品的尺寸×和y)
c)球状人工样品,合格的试样制备(所有人工样品抛光后尺寸相同)
d)球状人工样品,偏离的试样制备
(人工样品抛光后尺寸不相同)
图4运用基准人工样品确定抛光过程中试样是否对准的示意图
宜选择低收缩率的镶样物质,试样宜稳固地垂直于镶样模具表面。多孔氧化层材料的镶样推荐使用真空注人常温固化树脂的方式。
研磨和抛光步骤根据试样有所不同,但是要特别注意宜采用合适的润滑剂,以防止溶解掉腐蚀产物
5
GB/T41654—2022/ISO26146:2012
或沉积物中的化学成分。例如,碱性硫酸盐或卤化物溶于水,所以应采用非水基润滑剂。 6.2.3腐蚀层的分类
暴露试验后的试样可能存在以下层:
表面沉积物;
-
向外生长的腐蚀层;向内生长的腐蚀层;
内腐蚀产物层;晶界侵蚀区;去合金化区域;残留涂层;
-
-
一互扩散区;未被影响合金(剩余完好金属)。 这些层的定义详见第3章。
6.2.4腐蚀层的识别 6.2.4.1推荐在一系列标准放大倍数下(如100倍、400倍和1000倍)拍摄腐蚀产物和沉积物的光学图片,标准放大倍数宜根据试样破坏程度确定。选择的放大倍数能够在一张图片中清楚地显示总的破坏程度,以便于能够看到整个外部腐蚀层的厚度。光学显微镜中宜配有微米尺。 6.2.4.2可采用诸如化学刻蚀或干涉膜等多种技术增强不同层之间的对比度。 6.2.4.3根据具体检验要求,也可通过扫描电镜(SEM)、X射线衍射(XRD)等进行更多的表征。 6.2.5 针对金属材料损失评价的腐蚀层厚度测试 6.2.5.1应将试样划分为8个尺寸大致相同的部分。 6.2.5.2应在低的放大倍数下观察每一部分,找到剩余金属厚度最小的区域,测试将在该选定区域进行。 6.2.5.3在高的放大倍数下测试选定区域,在单一视场内显示100μm长的表面。 6.2.5.4应测试图5所示和定义的位置c和d。此外,为获取不同腐蚀层的补充信息,也可测试位置a、 f、b和e。 6.2.5.5最小剩余金属厚度(tm)是c和d之间的距离。金属损失厚度(tml)按tml=(t。一tm)/2计算, t和tml应写人试验报告。
6