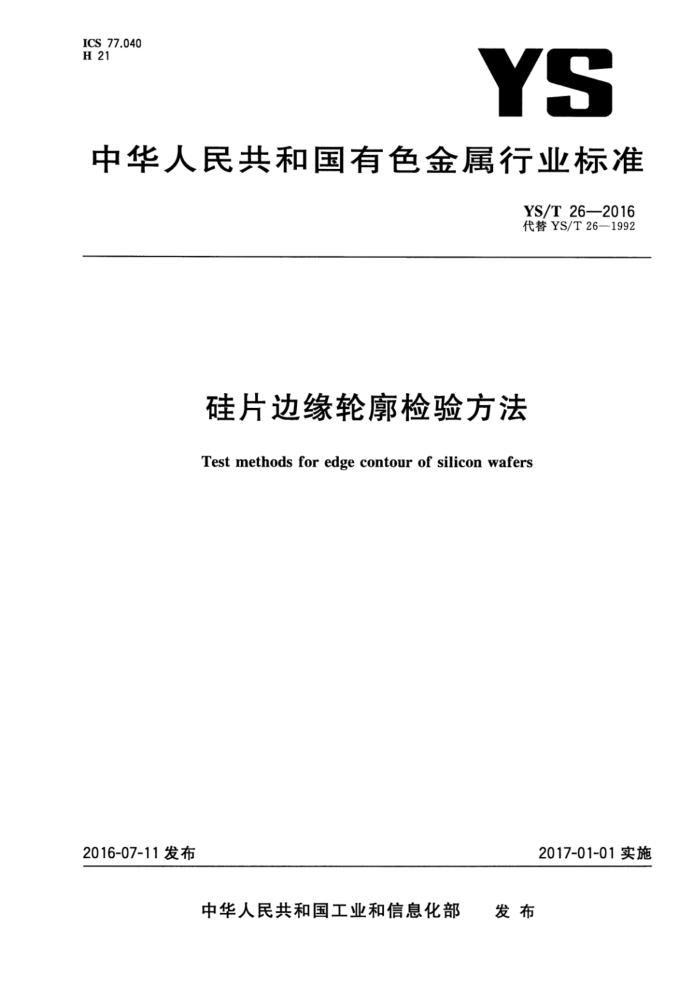
ICS 77.040 H 21
YS
中华人民共和国有色金属行业标准
YS/T26—2016 代替YS/T26—1992
硅片边缘轮廓检验方法
Test methods for edge contour of silicon wafers
2017-01-01实施
2016-07-11发布
发布
中华人民共和国工业和信息化部
YS/T26—2016
前言
本标准按照GB/T1.1一2009给出的规则起草。 本标准代替YS/T26--1992《硅片边缘轮廊检验方法》。与YS/T26—1992相比,本标准主要变动
如下:
-增加了规范性引用文件、术语和定义、干扰因素等; -增加了非破坏性检验方法B、方法C。
本标准由全国有色金属标准化技术委员会(SAC/TC243)提出并归口。 本标准起草单位:洛阳单晶硅集团有限责任公司、有研半导体材料有限公司、浙江金瑞泓科技股份
有限公司。
本标准主要起草人:田素霞、李战国、苗利刚、焦二强、安瑞阳、邵成波、王文卫。 本标准所代替标准的历次版本发布情况为:
YS/T26—1992。
I
YS/T 26—2016
硅片边缘轮检验方法
1范围
本标准规定了硅片边缘轮廊(包含切口)的检验方法。 本标准适用于检验倒角硅片的边缘轮廊(包含切口),砷化镓等其他材料晶片边缘轮廊的检验可参
照本标准执行。
2规范性引用文件
2
下列文件对于本文件的应用是必不可少的。凡是注日期的引用文件,仅注日期的版本适用于本文件。凡是不注日期的引用文件,其最新版本(包括所有的修改单)适用于本文件。
GB/T14264半导体材料术语
术语和定义
3
GB/T14264界定的术语和定义适用于本文件。
4方法提要
本标准规定了方法A、B、C三种测试方法,其测试原理分别如下: a)方法A:沿硅片径向划开形成剖面,借助光学比较仪或投影显微镜,形成一个硅片边缘区域的
剖面聚焦图形,将图形与边缘轮廊模板坐标图比较,确定边缘轮廊是否合格。本方法是破坏性的,限于圆周上离散点的检查,包括参考面,常用于直径不大于150mm硅片参考面倒角边缘轮廊的检测;
b)方法B:将硅片放置在平行光路下,硅片边缘投影到显示屏上,边缘轮廊的图像与边缘轮廊模
板坐标图比较,确定边缘轮廊是否合格。本方法是非破坏性的,可检查除了参考面和切口外硅片轮廊上所有的点,常用于直径不大于200mm硅片除参考面和切口外边缘轮廊的检测;
c)方法C:将硅片放置在光源下,光源照在硅片边缘,CCD相机将硅片边缘(不包括参考面)或切
口的轮廊形状的图像导人电脑,通过专用分析软件对检测图像进行分析,然后将轮廊形状的图像和测试结果显示在显示屏上,测试原理如图1所示。本方法是无接触、非破坏性的,可以测试硅片边缘和切口的轮廊形状,并能测量出轮廊尺寸。该方法操作简单便捷,可以直观的确定硅片边缘和切口是否合适,适用于各种尺寸、夹角和形状的硅片边缘轮廓的检测。本方法适用于日常过程监控,例如倒角机的调试、日常质量控制和进货、出厂检验等。
1
YS/T 26—2016
显示屏
主机(含画像处理装置)
主机(含画像处理装置)
显示屏
光源
硅片载物台
=
-
光源
CCD相机
载物台 硅片
CCD相机
a)检测边缘
b)检测切口
图1方法C测试原理示意图
5干扰因素
5.1光路上的外来物质、靠近已倒角硅片边缘的表面大颗粒、倒角边缘上的颗粒或其他异物都会给出错误的边缘轮廊,掩盖正确的轮廊形状。 5.2硅片上不同点的测量,可能带来测试数据的差异。 5.3对于方法C,设备的设置不同会带来测试数据的明显差异。
6仪器设备
6.1方法A测试所需的仪器设备如下:
a)光学比较仪或投影显微镜,放大倍数至少为100倍; b)用于固定待测硅片的夹具; c)硅片边缘轮廊模板坐标图,如图2所示,由一个确定硅片边缘轮廊合格的透明区域和一个半透
明的限制区域组成,其特征点坐标和基本尺寸应符合图3和表1的规定; d)量块或精密棒,与待测硅片厚度相同,可确定设备放大倍数; e)150mm长直尺,最小刻度为0.5mm或更小。
6.2 2方法B测试所需的仪器设备如下:
a)平行光源和可视系统,可视系统由投影仪、镜头和显示器组成。显示器应可以显示1mm
1mm的区域,可视系统提供给显示器的放大倍数至少为100倍; b) 用于固定待测硅片的夹具; c)硅片边缘轮廊模板坐标图,如图2所示,由一个确定硅片边缘轮廊合格的透明区域和一个半透
明的限制区域组成,其特征点坐标和基本尺寸应符合图3和表1的规定; d) 量块或精密棒,与待测硅片厚度相同,可确定设备放大倍数;
2
YS/T 26—2016
150mm长直尺,最小刻度为0.5mm或更小。
e)
正面
允许区域
背面
图2 硅片边缘轮廊模板坐标图
B
0
C
允许区域
图3 标准模板特征点坐标图
表1 标准模板特征点的坐标值
单位为微米
特征点 1 y
A 76 0
B 508 0
c 51
D 0 76
1/3硅片厚度
6.3方法C测试所需的仪器设备如下:
a) 边缘轮廊仪,包括光源、CCD相机、载物台; b) 控制单元,由计算机、显示器和打印机组成。
7试样
待测试片测试前应经倒角,且边缘清洁、干燥,而方法A需沿直径将硅片划开。
3
YS/T 262016
8测试准备
8.1确定放大倍数 8.1.1方法A:调节比较仪或显微镜至测试使用时的放大倍数。使用标准参数量块或精密棒,遵循比较仪或显微镜生产厂家的说明调节物像放大倍数至三位有效数字。 8.1.2方法B:在夹具上放置一个标准参数的量块,使用合适的尺子测试屏幕上垂直方向的尺寸。测量图像垂直尺寸精确至0.5mm,调节放大倍数至被测图像最清晰。重新放置量块或精密棒,测试显示屏上图像水平方向的尺寸,调节放大倍数至与垂直方向相同的放大倍数。 8.1.3方法C:放大倍数为边缘轮廊仪固有。 8.22 准备硅片边缘轮廓模板
硅片边缘轮廊模板(适用于方法A、B)按下列步骤准备: a)将标准模板坐标乘以放大倍数; b) 按放大后的模板尺寸,在透明材料上绘制或打印标准模板; c) 将模板固定在显示屏上,硅片表面的图像平行于相应模板的线。
9测试步骤
9.1方法A的测试步骤如下:
a) 将测试硅片放置在夹具上,硅片剖面对着物镜,垂直于观察方向; b) 调节比较仪的焦距,使硅片图像清晰地显示在显示屏上; c) 通过移动夹具调整硅片位置,使边缘轮廓图像与覆盖模板的前表面相切 d) 确定切线点之间的硅片边缘轮廊是否完全位于模板合格区域内; e) 重复9.1c)和9.1d),使边缘轮廊图像的另一面与模板在边缘和背面相切; f) 如果测试样品包括整个直径,倒转比较仪的夹具,使直径另一端的边缘轮廊显示在显示屏上,
重复9.1b)~9.1e); g) 如果硅片上其他部分作为测试样品,每部分都重复9.1a)~9.1e); h) 测试的边缘轮廊完全落在允许区域内的硅片为合格。
9.2方法B的测试步骤如下:
a) 将硅片放置在夹具上; b) 调节设备焦距使硅片边缘轮廊图像清晰地显示在显示屏上; c) 适当地移动夹具,使边缘轮廊图像与模板在边缘和正面相切; d) 确定切线点之间的硅片边缘轮廊是否完全位于模板合格区域内; e) 旋转夹具上的硅片,连续观察轮廊; f) 重复9.2c)~9.2e),使边缘轮廊图像的另一面与模板在边缘和背面相切; g) 测试的边缘轮廊完全落在允许区域内的硅片为合格。
9.3方法C的测试步骤如下:
a) 打开测试菜单; b) 根据硅片尺寸和边缘轮廊形状选择合适的测试文件; 4
YS/T26—2016
c) 用标准片校准设备; d) 根据待测硅片的尺寸,将硅片放置在载物台上相应的位置;
开始测试。边缘轮廊形状和测试结果会显示在显示屏上,并根据需要可以打印。该方法可以测试R型(见图4)、T型(见图5)、切口(见图6)等的轮廊形状。
e)
41
An
说明: A,、Az、B,、B2 轮廊长度;
硅片厚度;边缘轮廊顶部圆弧半径;
2 R
Ang1,Ang2 -边缘轮席夹角。
图4Type-R型
说明: A1A,、B1、B -轮廊长度;
硅片厚度;边缘轮廊顶部两侧圆弧半径;边缘轮廊夹角。
t
RI、R2 Angl,Ang2
图5 Type-T型
YS/T 26—2016
3 mm (Pin)
说明: V. V. P2 RI、R2 切口与硅片轮廊交接圆弧半径; V.
切口宽度;切口曲率半径 3mm(Pin)顶部到切口底部距离;
切口深度;
AngV 切口角度; P,=P,V.
-
图6切口
f)根据测试结果判断硅片边缘和切口是否合格。
9.4 测试点的位置和数量由供需双方商定。 9.5边缘轮廊精确数据的测试建议使用方法C。
10精密度
10.1方法A和B:仪器放大倍数为(100士1)倍,其相应的标准模板尺寸精确至0.05mm。在此条件下,单个实验室检验重复性达100%。 10.2方法C:
选取10片直径125mm的R型边缘轮廊硅片,和7片直径200mm的切口硅片,在同实验室、同设备进行多次测试,确定重复性误差。同一硅片在三家不同实验室进行测试,对比测试结果。测试精度如下:
边缘轮廊:长度(如A,、A2、B,、B)的单个实验室二倍标准偏差不大于2.092um,多个实验室二倍标准偏差不大于9.907μm;半径(如R)的单个实验室二倍标准偏差不大于2.609μm,多个实验室二倍标准偏差不大于2.884μm;角度(如Ang1、Ang2)的单个实验室二倍标准偏差不大于0.136°,多个实验室二倍标准偏差不大于1.311°。
切口:切口的深度和宽度(如V、Vw、P1、P2)单个实验室二倍标准偏差不大于0.008mm,多个实验室二倍标准偏差不大于0.471mm;角度(如AngV)单个实验室二倍标准偏差不大于0.104°,多个实验室二倍标准偏差不大于0.674°;底部和顶部半径(如V.、R1、R等)单个实验室二倍标准偏差不大于 0.025mm,多个实验室二倍标准偏差不大于0.116mm。
11试验报告
试验报告应包含以下内容: a) 测试日期; b)测试人员姓名; 6