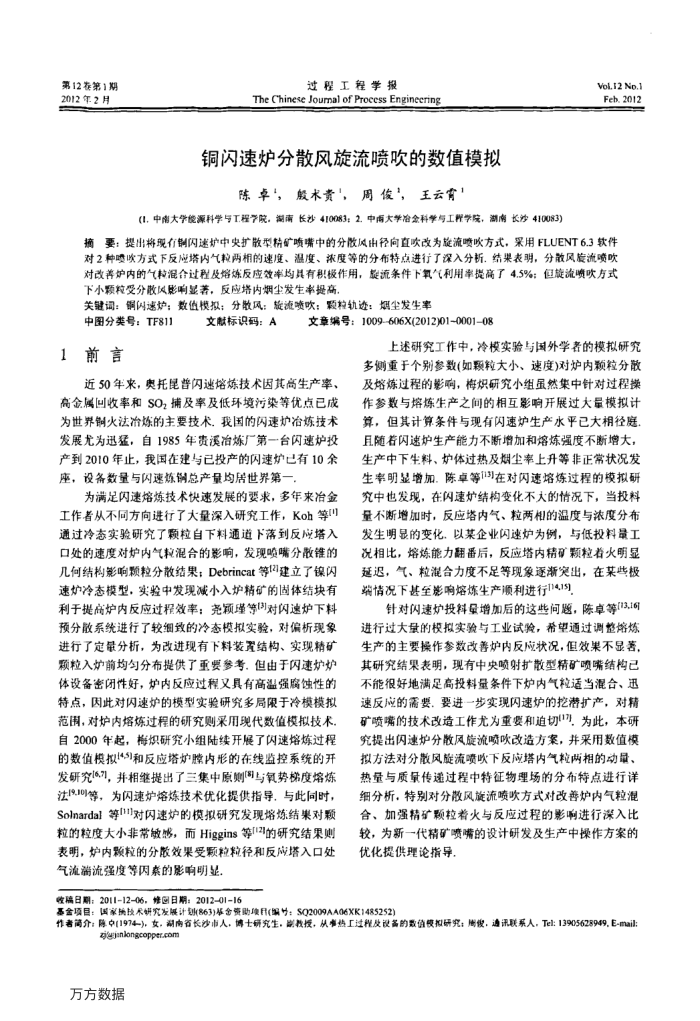
第12卷第1期 2012年2月
过程工程学报
The Chinese Jourmal of Process Engineering
铜闪速炉分散风旋流喷吹的数值模拟
陈卓,般术资,周俊,王云宵1
(1,中南大学能源科学与工程予院,潮南长沙410083;2.中南大学冶余科学与工程学院,湖南长沙410083)
Vol.12 No.1 Feb,2012
摘要:提出将现有钢闪速炉中央扩散型精矿喷嘴中的分散风由轻向直吹改为旋流喷吹方式,采用FLUENT6.3软件对2种喷吹方式下反应塔内气粒两相的速度、温度、浓度等的分布特点进行了深入分析.结果表明,分散风流喷吹对改善炉内的气粒混合过程及熔炼反应效率均具有积极作用,整流条件下氧气利用净率提高了4.5%:旋流喷吹方式下小颗粒受分散风影制显著,反应塔内烟尘发生率提高
关键调:铜闪速炉;数值模拟;分敏风:旋流喷吹:颗控轨迹:烟尘发生率
中图分类号:TF811 1前言
文献标识码:A
文章编号:1009-606X(2012)01-000108
上述研究工作中,冷模实验与国外学者的模拟研究
多侧重于个别参数(如颗粒大小、速度)对炉内颗粒分散
近50年来,奥托昆普闪速熔炼技术因其高生产率、高金属回收率和SO2捕及率及低环境污染等优点已成为世界铜火法冶炼的主要技术。我国的闪速炉冶炼技术发展尤为迅猛,自1985年贵溪冶炼厂第一台闪速炉投产到2010年止,我国在建与已投产的闪速炉已有10余座,设备数量与闪速炼钢总产量均居世界第一
为满足闪速熔炼技术快速发展的要求,多年来冶金工作者从不同方向进行了大量深入研究工作,Koh等川通过冷态实验研究了颗粒自下料通道下落到反成塔入口处的速度对炉内气粒混合的影响,发现喷嘴分散锥的几何结构影响颗粒分散结果;Debrincat等建立了镍闪速炉冷态模型,实验中发现减小入炉精矿的固体结块有利于提高炉内反应过程效率;尧预瑾等川对闪速炉下料预分散系统进行了较组致的冷态模拟实验,对偏析现象进行了定量分析,为改进现有下料装置结构、实现精矿颗粒入炉前均匀分布提供了重要参考。但由于闪速炉炉体设备密闭性好,炉内反应过程又具有高温强腐蚀性的特点,因此对闪速炉的模型实验研究多局限于冷模模拟范围,对炉内熔炼过程的研究则采用现代数值模拟技术自2000年起,梅炽研究小组陆续开展了闪速熔炼过程的数值模拟45和反应塔炉膜内形的在线监控系统的开发研究67],并相提出了三集中原则图与氧势梯度熔炼法9叫等,为闪速炉熔炼技术优化提供指导,与此同时, Solnardal等I对闪速炉的模拟研究发现熔炼结果对颗粒的粒度大小非常敏够,而Higgins等[12I的研究结果则表明,炉内颗粒的分散效果受颗粒粒径和反应塔入口处气流瑞流强度等内素的影响明显
及熔炼过程的影响,梅炽研究小组虽然集中针对过程操作参数与熔炼生产之间的相互影响开展过大量模拟计算,但其计算条件与现有闪速炉生产水平已大相径庭且随闪速炉生产能力不断增加和熔炼强度不断增大,生产中下生料、炉体过热及烟尘率上升等非正常状况发生率明显增加.陈卓等在对闪速熔炼过程的模拟研究中也发现,在闪速炉结构变化不大的情况下,当投料量不断增加时,反应塔内气、粒两相的温度与浓度分布发生明显的变化.以某企业闪速炉为例,与低投料量工况相比,熔炼能力翻番后,反应塔内精矿颗粒着火明显延迟,气、粒混合力度不足等现象逐渐突出,在某些极端情况下甚至影响熔炼生产顺利进行114,15],
针对闪速炉投料量增加后的这些问题,陈卓等(13,16) 进行过大量的模拟实验与工业试验,希望通过调整熔炼生产的主要操作参数改善炉内反应状况,值效果不显著,其研究结果表明,现有中央喷射扩散型精矿喷嘴结构已不能很好地满足高投料量条件下炉内气粒适当混合、迅速反应的需要要进一步实现闪速炉的挖潜扩产,对精矿喷嘴的技术改造工作尤为重要和追切17],为此,本研究提出闪速炉分散风旋流喷吹改造方案,并采用数值模拟方法对分散风旋流喷吹下反应塔内气粒两相的动量、热量与质量传递过程中特征物理场的分布特点进行详细分析,特别对分散风旋流喷吹方式对改善炉内气粒混合、加强精矿颗着火与反应过程的影响进行深入比较,为新一代精矿喷嘴的设计研发及生产中操作方案的优化提供理论指导,
收稿日期:2011-1206,修图日期:2012-01-16
基金项目:国家换股术拼究发展计谢(863)率金资助项月(编中:SQ2009AA06XK1485252)
作者简介:降中(1974-),女,内省长沙市人,博士研究生,影教,从有热工过程及设备的数值模拟研究:图俊,通讯联系人,Tel:13905628949,E-mail:
zj:jisnlongcopper.com 万方数据