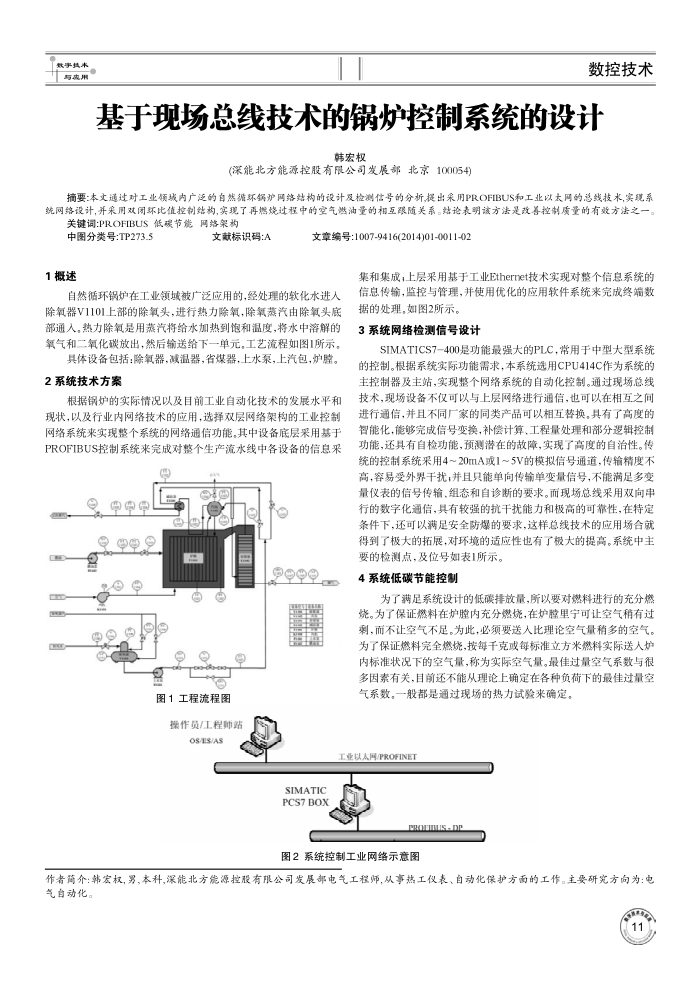
数事共本与表用
数控技术
基于现场总线技术的锅炉控制系统的设计
韩宏权
(深能北方能源控股有限公司发展部北京100054)
摘要:本文通过对工业领或内广泛的自然错环锅炉网络结构的设计及检测信号的分析,提出采用PROFIBUS和工业以太网的总线技术,实境系统网络设计,并采用阅环比值控制结构,实现了再燃烧过程中的空气燃油量的相互跟随关系。结论表明该方法是改善控制质量的有效方法之一
关键调:PROFIBUS低碳节能网络架构
中图分类号:TP273.5 1概述
文献标识码:A
文章编号:1007-9416(2014)01-0011-02
集和集成,上层采用基于工业Ethernet技术实现对整个信息系统的
自然循环铝炉在工业领域被广泛应用的,经处理的软化水进人除氧器V1101上部的除氟头,进行热力除氧,除氧蒸汽由除氧氟头底部通人,热力除氧是用蒸汽将给水加热到饱和温度,将水中溶解的氧气和二氧化碳放出,然后输送给下一单元。工艺流程如图1所示。
具体设备包括:除氧器,减温器,省煤器,上水泵,上汽包,炉腺。 2系统技术方案
根据锅炉的实际情况以及目前工业自动化技术的发展水平和现状,以及行业内网络技术的应用,选择双层网络架构的工业控制网络系统来实现整个系统的网络通信功能。其中设备底层采用基于 PROFIBUS控制系统来完成对整个生产流水线中各设备的信息采
@
66
0
C
图1工程流程图操作员工程师站
OS/ES/AS
信息传输,监控与管理,并使用优化的应用软件系统来完成终端数据的处理。如图2所示。
3系统网络检测信号设计
SIMATICS7-400是功能最强大的PLC,常用于中型大型系统的控制。根据系统实际功能需求,本系统选用CPU414C作为系统的主控制器及主站,实现整个网络系统的自动化控制。通过现场总线技术,现场设备不仅可以与上层网络进行通信,也可以在相互之间进行通信,并且不同厂家的同类产品可以相互替换,具有了高度的智能化,能够完成信号变换,补偿计算、工程量处理和部分逻辑控制功能,还具有自检功能,预测潜在的故障,实现了高度的自治性。传统的控制系统采用4~20mA或1~5V的模拟信号通道,传输精度不高,容易受外界干扰,并且只能单向传输单变量信号,不能满足多变量仪表的信号传输、组态和自诊断的要求。而现场总线采用双向申行的数字化通信,具有较强的抗干扰能力和极高的可靠性,在特定条件下,还可以满足安全防爆的要求,这样总线技术的应用场合就得到了极大的拓展,对环境的适应性也有了极大的提高。系统中主
要的检测点,及位号如表1所示。 4系统低碳节能控制
为了满足系统设计的低碳排放量,所以要对燃料进行的充分燃烧。为了保证燃料在炉膜内充分燃烧,在炉膜里宁可让空气稍有过测,而不让空气不足。为此,必须要送人比理论空气量稍多的空气。为了保证燃料完全燃烧,按每千克或每标准立方米燃料实际送人炉内标准状况下的空气量,称为实际空气量。最佳过量空气系数与很多因素有关,目前还不能从理论上确定在各种负荷下的最佳过量空气系数。一般都是通过现场的热力试验来确定。
工业以A网/PROFINET
SIMATIC PCS7BOX
PROEIRUS-D
图2系统控制工业网络示意图
作者简介:韩宏权,男,本科,深能北方能源控股有限公司发展部电气工程师,从事热工仪表、自动化保护方面的工作。主要研究方向为:电气自动化。