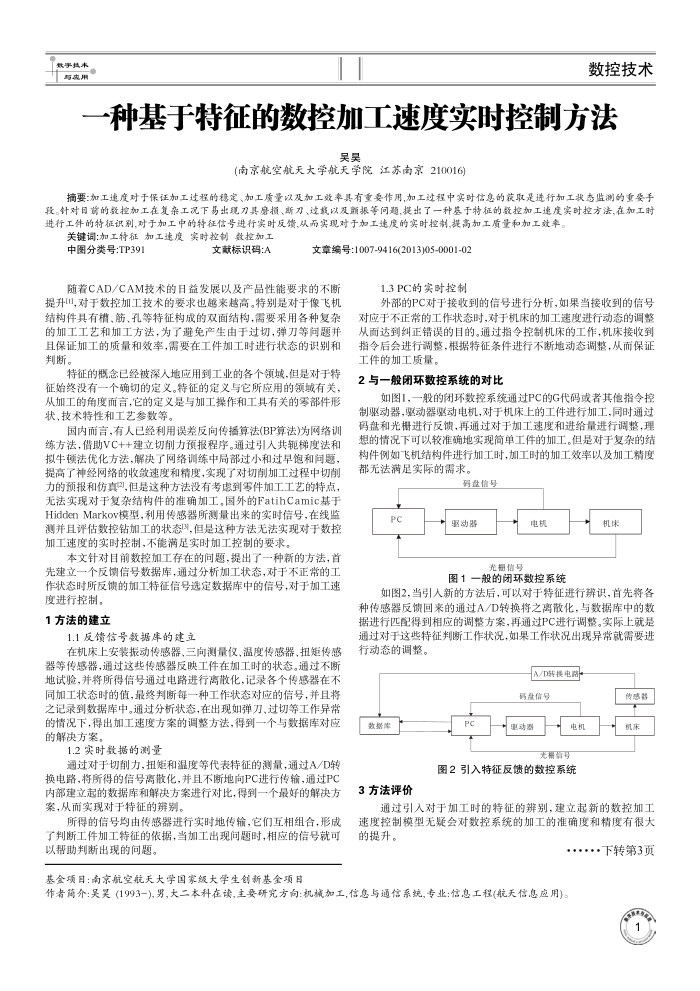
数字热本与变用
数控技术
一种基于特征的数控加工速度实时控制方法
吴吴
(南京航空航天大学航天学院江苏南京210016)
摘要:加工速度对于保证加工过程的稳定、加工质量以及加工效率具有重要作用,加工过程中实时信息的获取是进行加工状态监测的重要手段。针对日前的数控加工在复杂工况下易出现刀具旁损、断刀、过载以及颤振等问题,提出了一种基于特征的数控加工速度实时控方法,在加工时进行工件的特征识别,对于加工中的特征信号进行实时反馈,从而实现对于加工违度的实时控制,提高加工质量和加工效率。
关键调:加工特征加工速度实时控制数控加工
文献标识码:A
中图分类号TP391
文章编号:1007-9416(2013)05-0001-02
随着CAD/CAM技术的日益发展以及产品性能要求的不断提升,对于数控加工技术的要求也越来越高。特别是对于像飞机结构件具有槽、筋、孔等特征构成的双面结构,需要采用各种复杂的加工工艺和加工方法,为了避免产生由于过切,弹刀等问题并且保证加工的质量和效率,需要在工件加工时进行状态的识别和判断。
特征的概念已经被深人地应用到工业的各个领域,但是对于特征始终没有一个确切的定义。特征的定义与它所应用的领域有关,从加工的角度而言,它的定义是与加工操作和工具有关的零部件形状,技术特性和工艺参数等。
国内而言,有人已经利用误差反向间传播算法(BP算法)为网络训练方法,借助VC++建立切削力预报程序。通过引人共轭梯度法和拟牛顿法优化方法,解决了网络训练中局部过小和过早饱和问题,提高了神经网络的收敛速度和精度,实现了对切削加工过程中切削力的预报和仿真,但是这种方法没有考到零件加工工艺的特点无法实现对于复杂结构件的准确加工。国外的FatihCamic基于 HiddenMarkov模型,利用传感器所测量出来的实时信号,在线监测并且评估数控钻加工的状态3,但是这种方法无法实现对于数控加工速度的实时控制,不能满足实时加工控制的要求。
本文针对目前数控加工存在的问题,提出了一种新的方法,首先建立一个反馈信号数据库,通过分析加工状态,对于不正常的工作状态时所反馈的加工特征信号选定数据库中的信号,对于加工速
度进行控制, 1方法的建立
1.1反馈信号数据库的建立
在机床上安装振动传感器、三向测量仪、温度传感器、扭矩传感器等传感器,通过这些传感器反映工件在加工时的状态。通过不断地试验,并将所得信号通过电路进行离散化,记录各个传感器在不同加工状态时的值,最终判断每一种工作状态对应的信号,并且将之记录到数据库中。通过分析状态,在出现如弹刀,过切等工作异常的情况下,得出加工速度方案的调整方法,得到一个与数据库对应的解决方案。
1.2实时数据的测量
通过对于切削力,扭矩和湿度等代表特征的测量,通过A/D转换电路,将所得的信号离散化,并且不断地向PC进行传输,通过PC 内部建立起的数据库和解决方案进行对比,得到一个最好的解决方案,从而实现对于特征的辨别。
所得的信号均由传感器进行实时地传输,它们互相组合,形成了判断工件加工特征的依据,当加工出现间题时,相应的信号就可以帮助判断出现的问题。
基金项目:南京航空航天大学国家级大学生创新基金项目
1.3PC的实时控制
外部的PC对于接收到的信号进行分析,如果当接收到的信号对应于不正常的工作状态时,对于机床的加工速度进行动态的调整从面达到纠正错误的目的。通过指令控制机床的工作,机床接收到指令后会进行调整,根据特征条件进行不断地动态调整,从而保证工件的加工质量。
2与一般闭环数控系统的对比
如图1,一般的闭环数控系统通过PC的G代码或者其他指令控制驱动器,驱动器驱动电机,对于机床上的工件进行加工,同时通过码盘和光栅进行反馈,再通过对于加工速度和进给量进行调整,理想的情况下可以较准确地实现简单工件的加工。但是对于复杂的结构件例如飞机结构件进行加工时,加工时的加工效率以及加工精度都无法满足实际的需求。
码盘信号
PC
驱动器
光栅信号
电机
图1一般的闭环数控系统
机床
如图2,当引人新的方法后,可以对于特征进行辨识,首先将备种传感器反馈回来的通过A/D转换将之离散化,与数据库中的数据进行匹配得到相应的调整方案,再通过PC进行调整。实际上就是通过对于这些特征判断工作状况,如果工作状况出现异常就需要进行动态的调整。
A/D转换电器
码盘信号
数据率 3方法评价
重动器
电机
无栅薪号
图2引入特征反馈的数控系统
传感器机床
通过引入对于加工时的特征的辨别,建立起新的数控加工速度控制模型无疑会对数控系统的加工的准确度和精度有很大的提升。
.下转第3页
作者简介:吴昊(1993一),男,大二本科在读,主要研究方向:机械加工,信息与通信系统,专业:信息工程(航天信息应用)。