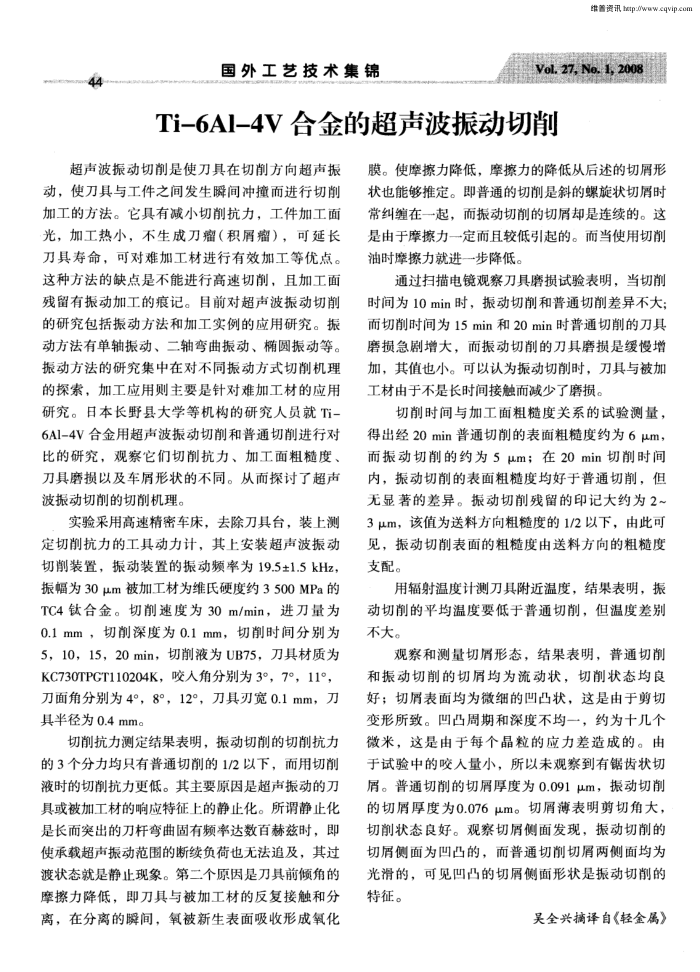
44
国外工艺技术集锦
维警资讯thetp:/wew.cqvip.cor
Vol.27,No.1,2008
Ti-6AI-4V合金的超声波振动切削
超声波振动切削是使刀具在切削方向超声振动,使刀具与工件之间发生瞬间冲撞而进行切削加工的方法。它具有减小切削抗力,工件加工面光,加工热小,不生成刀瘤(积屑瘤),可延长刀具寿命,可对难加工材进行有效加工等优点。这种方法的缺点是不能进行高速切削,且加工面残留有振动加工的痕记。目前对超声波振动切削的研究包括振动方法和加工实例的应用研究。振动方法有单轴振动、二轴弯曲振动、椭圆振动等。振动方法的研究集中在对不同振动方式切削机理的探索,加工应用则主要是针对难加工材的应用研究。日本长野县大学等机构的研究人员就Ti-6A1-4V合金用超声波振动切削和普通切削进行对比的研究,观察它们切削抗力、加工面粗糙度、刀具磨损以及车屑形状的不同。从而探讨了超声波振动切削的切削机理。
实验采用高速精密车床,去除刀具台,装上测
定切前抗力的工具动力计,其上安装超声波振动切削装置,振动装置的振动频率为19.5±1.5kHz,振幅为30μm被加工材为维氏硬度约3500MPa的 TC4钛合金。切削速度为30m/min,进刀量为 0.1mm,切削深度为0.1mm,切削时间分别为 5,10,15,20min,切削液为UB75,刀具材质为 KC730TPGT110204K,咬人角分别为3°,7°,11°,刀面角分别为4°,8°,12°,刀具刃宽0.1mm,刀具半径为0.4mm
切前抗力测定结果表明,振动切削的切前抗力
的3个分力均只有普通切削的1/2以下,而用切削液时的切前抗力更低。其主要原因是超声振动的力具或被加工材的响应特征上的静止化。所谓静止化是长而突出的刀杆弯曲固有频率达数百赫兹时,即使承载超声振动范围的断续负荷也无法追及,其过渡状态就是静止现象。第二个原因是刀具前倾角的摩擦力降低,即刀具与被加工材的反复接触和分离,在分离的瞬间,氧被新生表面吸收形成氧化
膜。使摩擦力降低,摩擦力的降低从后述的切屑形状也能够推定。即普通的切前是斜的螺旋状切的常纠缠在一起,而振动切削的切屑却是连续的。这是由于摩擦力一定而且较低引起的。而当使用切削油时摩擦力就进一步降低。
通过扫描电镜观察刀具磨损试验表明,当切削时间为10min时,振动切削和普通切削差异不大:而切削时间为15min和20min时普通切削的刀具磨损急剧增大,而振动切削的刀具磨损是缓慢增加,其值也小。可以认为振动切削时,刀具与被加工材由于不是长时间接触而减少了磨损。
切削时间与加工面粗糙度关系的试验测量,得出经20min普通切削的表面粗糙度约为6μm,而振动切削的约为5μm;在20min切削时间内,振动切削的表面粗精度均好于普通切削,但无显著的差异。振动切削残留的印记大约为2~ 3μm,该值为送料方向粗槛度的1/2以下,由此可见,振动切削表面的粗糙度由送料方向的粗糙度支配。
用辐射温度计测刀具附近温度,结果表明,振动切削的平均温度要低于普通切削,但温度差别不大。
观系和测量切屑形态,结果表明,普通切削和振动切削的切屑均为流动状,切前削状态均良好;切屑表面均为微细的凹凸状,这是由于剪切变形所致。凹凸周期和深度不均一,约为十几个微米,这是由于每个晶粒的应力差造成的。由于试验中的咬入量小,所以未观察到有锯齿状切屑。普通切削的切屑厚度为0.091μm,振动切削的切屑厚度为0.076μm。切屑薄表明剪切角大,切前状态良好。观察切屑侧面发现,振动切削的切屑侧面为回凸的,而普通切切消两侧面均为光滑的,可见凹凸的切屑侧面形状是振动切削的特征。
吴全兴摘译自《轻金属》