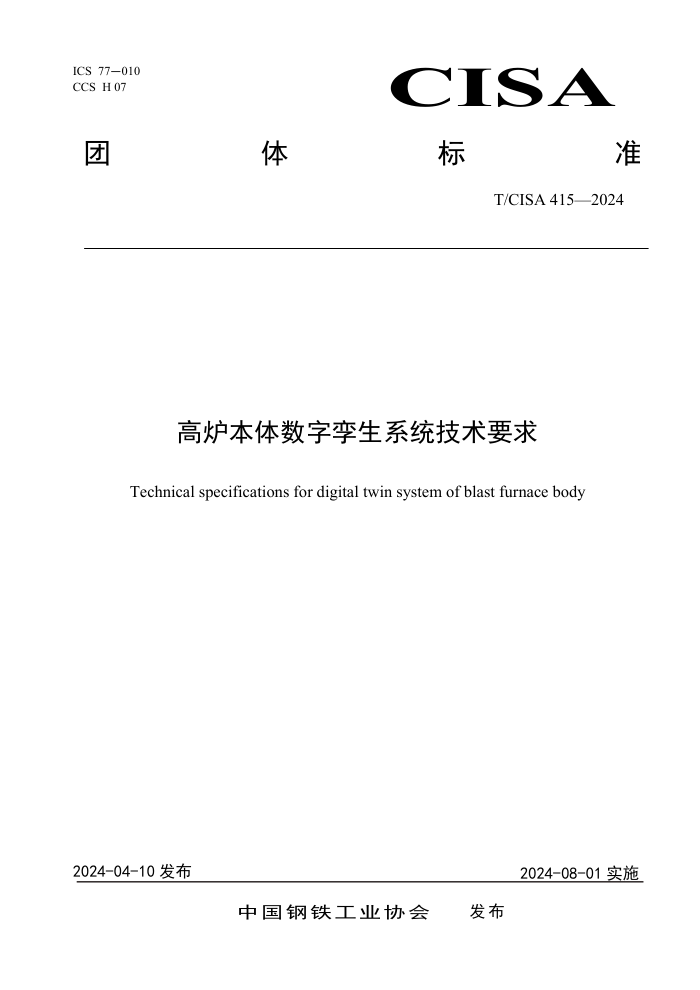
ICS 77—010
CCS H 07
团
体
CISA
标
准
T/CISA 415—2024
高炉本体数字孪生系统技术要求
Technical specifications for digital twin system of blast furnace body
2024-04-10 发布 2024-08-01 实施
中国钢铁工业协会 发 布
T/CISA 415—2024
前
言
本文件按照GB/T 1.1—2020《标准化工作导则 第1部分:标准化文件的结构和起草规则》的规定起
草。
请注意本文件的某些内容可能涉及专利。本文件的发布机构不承担识别专利的责任。
本文件由中国钢铁工业协会提出。
本文件由全国钢标准化技术委员会(SAC/TC183)归口。
本文件起草单位:北京智冶互联科技有限公司、建龙阿城钢铁有限公司、冶金工业信息标准研究院、
中冶南方工程技术有限公司、南京强思数字科技有限公司、中冶华天工程技术有限公司、中冶东方工程
技术有限公司、北京金恒博远科技股份有限公司、陕钢集团有限公司、中国钢铁工业协会、鞍钢集团自
动化有限公司、首钢集团有限公司、中国软件评测中心。
本文件主要起草人:葛小亮、续飞飞、赵晶晶、赵宏博、王博、严晗、丁宏翔、王来信、马志坚、
彭尊、杨建鹏、曹仲勇、王弢、毛明涛、王凤琴、李永杰、宋彩群、杨春建、周晟程、林子恒、周烽、
高心宇、陈百红、周春晖、李海涛、高大鹏、吴建、王淑娟。
II
T/CISA415—2024
高炉本体数字孪生系统技术要求
1 范围
本文件规定了高炉本体数字孪生系统的技术架构、数据层、模型层、应用场景等技术要求。
本文件适用于钢铁企业高炉本体数字孪生系统的开发与设计。
2 规范性引用文件
下列文件中的内容通过文中的规范性引用而构成本文件必不可少的条款。其中,注日期的引用文件,
仅该日期对应的版本适用于本文件;不注日期的引用文件,其最新版本(包括所有的修改单)适用于本
文件。
GB/T 38637.2—2020 物联网 感知控制设备接入 第 2 部分:数据管理要求
T/CISA 201—2022 钢铁行业 高炉智能感知及可视化系统技术要求
3 术语和定义
下列术语和定义适用于本文件。
3.1
高炉本体数字孪生系统 digital twin system of blast furnace body
应用新一代信息技术,使高炉本体具备泛在连接、虚实映射、模拟仿真、实时优化、科学决策、友
好体验等特征,实现高炉本体稳定、高效、经济运行的系统。
3.2
设备模型 equipment model
依据设备的几何结构、空间运动、几何关联等几何属性而建立的模型。
3.3
数据科学模型 data science model
利用数据科学技术对数据进行分析、特征提取而建立的模型。
3.4
知识模型 knowledge model
依据高炉操作者的学习、实践、探索所获取的认知、判断或技能而建立的模型。
3.5
机理模型 mechanism model
根据对象、生产过程的内部机制或者物质流的传递机理建立的精确数学模型。
4 技术架构
4.1 系统架构
1
T/CISA 415—2024
高炉本体数字孪生系统架构包括物理层、数据层、模型层、应用层,见图 1。
物理层包括高炉本体物理实体、分布式控制系统、可编程逻辑控制器、传感器等。
数据层包括数据采集、数据预处理、数据存储。系统通过数据层为模型层提供高效的数据服务。另
外,数据层也可以将模型层的结果下发至物理实体感知层,对高炉实体进行调整控制。
模型层包括工业建模、模型验证、模型融合。按照建模内容与方式,工业建模包括设备模型、知识
模型、机理模型、数据科学模型。系统通过模型验证提高模型的准确性与稳定性,通过不同类型工业模
型的融合实现高炉本体数字孪生系统的构建。
应用层包括可视化、设备故障诊断、工艺参数优化、生产过程控制、数字孪生实训等。
注:涉及物理层部分的技术内容不在本文件中进行规定;应用层仅列出数字孪生相关的应用服务场景,不对具体技
术内容进行规定。
注:虚框部分相关的技术要求不在本文件规定的范围内。
图 1 高炉本体数字孪生系统架构
4.2 虚实映射
数字虚体通过采集、存储生产过程中的控制器、传感器等数据,实现对高炉本体实体的在线动态感
知;通过工业建模分析及交互应用,将仿真优化结果下发至高炉本体实体,实现对高炉生产过程的优化,
其逻辑架构见图 2。
2
T/CISA415—2024
图 2 高炉本体数字孪生虚实映射逻辑架构
高炉本体数字孪生系统的虚实映射应包括但不限于以下功能:
a)
高炉本体实体与数字虚体之间应建立动态镜像关系,数字虚体应能实时动态反映高炉本体实体
的生产过程及状态;
b)
数字虚体应针对数字虚体与物理空间存在的差异进行重构或者更新;
c)
数字虚体可依据实际情况将模拟分析结果下发至高炉实体控制器,优化高炉实体生产状态。
5 数据层要求
5.1 数据采集
5.1.1 通用要求
数据采集通用要求应符合 GB/T 38637.2—2020 中 5.1 的规定。
5.1.2 数据源要求
5.1.2.1 原燃料质量数据
5.1.2.1.1 原燃料类型包括但不限于烧结矿、球团矿、块矿、熔剂、焦炭、喷吹物等;
5.1.2.1.2 质量数据类型包括但不限于化学成分数据(需包含有害元素)、粒度数据、物理性能数据、
冷热态强度数据、原料类的软熔性能数据、燃料类的灰分全分析数据;
5.1.2.1.3 化学成分、粒度数据、物理性能、冷热态强度数据频率频次不应低于 8 小时/次,软熔性能数
据频次频率不应低于 7 天/次,灰分全分析数据频率频次不应低于 1 天/次。
5.1.2.2 产品、副产品数据
包括但不限于铁水、炉渣产品的成分数据、铁水计量数据,炉顶煤气成分、重力灰、布袋灰等副产
品的检化验数据,其中铁水成分及温度数据宜按罐次化验,铁水计量数据应按罐次称量,炉渣成分应按
铁次化验,重力灰、布袋灰等副产品数据化验频次应不低于 1 天/次。
5.1.2.3 生产过程信号及状态数据
包括但不限于高炉生产送风参数、槽下排料信号及参数、炉顶布料信号参数、冷却壁热电偶温度监
测数据、水系统温度流量压力数据、炉身静压力监测数据、十字测温监测数据、炉缸炉底热电偶监测数
据。该类数据频次应在秒级以上。
5.1.2.4 炉前出铁数据
炉前出铁数据应包括但不限于铁口号、铁次号、出铁开始时间、出铁结束时间、见渣时间。该类数
3
T/CISA 415—2024
据应按照铁次采集。
5.1.2.5 风口更换记录数据
风口更换记录数据应包括但不限于风口号、风口直径、风口长度、开堵状态、喷煤状态等。该类数
据应按照风口更换的实际发生情况采集。
5.2 数据预处理
5.2.1 数据转换和抽取
数据的转换和抽取应符合 GB/T 38637.2—2020 中 6.1.1 和 6.1.2 的规定。
5.2.2 数据清洗
数据的清洗应符合 GB/T 38637.2—2020 中 6.1.3 的规定。清洗的数据应包括但不限于以下内容:
a)
高炉换炉时期的风量、风压数据;
b)
炉顶煤气分析仪吹扫期间的炉顶 CO、CO2、H2、N2 成分数据;
c)
炉身静压测量装置反吹期间的炉身静压数据。
5.2.3 数据逻辑关联
在建立高炉本体数字孪生体统时,应根据高炉炼铁工艺业务流程对不同节点数据进行一致性匹配,
包括但不限于以下内容:
a)
含铁炉料成分与高炉变料在时间、空间上的匹配,应考虑含铁炉料的取样位置、槽存量、消耗
速度预估其成分到达炉顶的时间;
b)
高炉上部焦炭负荷与下部喷吹物数据的匹配,应考虑下部喷吹调剂与上部调整负荷的匹配时机,
将焦炭负荷与喷吹物数据进行匹配;
c)
应考虑风温、风量、喷吹物、富氧、焦比等与炉温的匹配。
5.3 数据存储
5.3.1 存储空间
物理存储空间应满足高炉一代炉役以上的数据量存储。
5.3.2 存储工具
包括但不限于结构化数据库、非结构化数据库、时序数据库。
5.3.3 存储备份
应符合 GB/T 38637.2—2020 中 6.2.5 的规定。
6 模型层要求
6.1 工业模型
6.1.1 设备模型
高炉本体数字孪生的设备建模内容应包括设备对象的几何结构、运动及过程渲染、连接件的数字化
复刻。设备模型应包括但不限于:
a)
本体结构设备:高炉炉壳、冷却壁、填料、砖衬、炉缸炭砖、炉缸陶瓷杯垫;
b)
送风装置设备:风口小套、中套、大套、直吹管;
4
T/CISA415—2024
c)
炉顶装料设备:探尺、溜槽、上料罐、下料罐、上下阀体、炉顶齿轮箱;
d)
喷吹装置设备:喷吹枪。
6.1.2 知识模型
6.1.2.1 基于专家知识库的诊断模型
该模型应满足以下功能要求:
a)
知识库中滑料、渣皮脱落、渣皮生长、管道、炉墙热负荷、气流分布变化、炉缸状态分析、高
炉状态变化、高炉压损变化、下部活跃性、漏水诊断、悬料、塌料诊断功能应满足 T/CISA
201—2022 中 9.2.2 的规定;
b)
炉热趋势判断:应根据近期料速、风量、透气性、煤气利用率、顶温、当前高炉物理热水平,
对高炉未来热状态趋势进行判断,并按照上述参数波动程度给出炉热发展趋势级别;
c)
诊断过程追溯:应能对异常诊断结果的诊断过程进行逐级追溯原因;
d)
知识库自学习:诊断知识库应能根据高炉炉役演变过程自适应、自学习升级。
6.1.2.2 高炉顺行体检模型
该模型应满足以下功能要求:
a)
应从炉体安全、原燃料质量、生产组织、能耗、环保、工艺参数、关键设备运行状态七个维度
对高炉运行状态进行综合评价;
b)
可每天对高炉顺行状态进行总体评价,并自动生成高炉顺行体检报告,对异常项目进行标记;
c)
指标范围及评价规则应满足现场实际生产。
6.1.3 机理模型
6.1.3.1 高炉炉顶在线布料仿真模型
高炉炉顶在线布料仿真模型是基于单颗粒受力分析计算,对高炉炉顶布料的料流轨迹、内部料面形
状、料面下移过程进行模拟,得到高炉径向矿焦比、矿焦层厚度分布曲线,用于判断料面形状是否合理,
指导高炉现场布料制度调整。该模型应满足以下功能要求:
a)自动模拟计算每一批炉料布料过程中的料流落点及布料后料面形状;
b)计算每一批炉料沿高炉半径方向的矿焦比分布及显示矿焦比分布曲线;
c)根据高炉布料矩阵自动计算高炉内的边缘负荷、中心负荷、矿石环带宽度等参数。
6.1.3.2 高炉块状带仿真模型
高炉块状带仿真模型是依据高炉设计炉型、炉料物理性能,自动计算并模拟炉料入炉后在下降过程
中的料面形状及料层厚度变化。该模型应满足以下功能要求:
a) 根据高炉各部位压缩率、炉料堆比、重量,模拟炉料在炉内各部位平均厚度;
b)模拟预测当前冶炼条件下,炉料到达风口的时间;
c) 自动计算高炉冶炼周期,实时判断每批料在块状带的位置变化;
d)自动或手动标记异常炉料,自动跟踪炉料在炉内冶炼进程。
6.1.3.3 高炉操作炉型及挂渣厚度仿真模型
高炉操作炉型及挂渣厚度仿真模型是依据高炉冷却壁冷却数据、设计数据,进行冷却壁温度场模拟
计算,实现对高炉炉腹炉腰炉身下部冷却壁炉墙的砖衬厚度、挂渣厚度、操作炉型等在线监测和图像重
建,用于指导现场进行炉型判断。该模型应满足以下功能要求:
a) 模拟计算不同横截面、纵切面的渣皮厚度,绘制操作炉型及渣皮形状;
b) 模拟计算每块冷却壁的砖衬厚度和渣皮厚度;
c) 统计炉墙渣皮脱落频率、裸露时间;
d) 对不同段位和不同方位的区域内渣皮脱落次数进行统计和预警。
5
T/CISA 415—2024
6.1.3.4 高炉炉缸炉底炭砖侵蚀残厚仿真模型
高炉炉缸炉底炭砖侵蚀残厚仿真模型是依据高炉炉缸炉底设计尺寸、炭砖材质、热电偶温度,进行
炉缸炉底三维、非稳态温度场模拟,实现对高炉炉缸炉底侵蚀残厚的图像重建。该模型应满足以下功能
要求:
a) 模拟计算炉底炉缸等温线、温度场、残衬厚度、渣铁壳厚度;
b) 按照纵剖面、横剖面两种方式绘制炉底炉缸侵蚀内型和渣铁壳形状、温度场;
c) 在高炉采取护炉措施时,自动计算并显示炉底炉缸渣铁壳的生成位置、厚度、形状;
d) 应具有炉底气隙、环裂等炉缸异常诊断知识库。
6.1.3.5 高炉出铁平衡模型
高炉出铁平衡模型是根据理论计算的实时产铁量以及现场轨道衡/车载秤的实时出铁、出渣数据进
行盈亏铁量计算。应能实时模拟高炉内部的渣铁液面高度,对出铁时机进行自动预判。
6.1.3.6 送风制度模型
高炉送风制度模型是以伯努利定律、热平衡理论为基础,实时模拟风口回旋区状态,用于判断高炉
初始气流状态。该模型应满足以下功能要求:
a)
根据送风参数、风口长度、风口直径自动计算每个风口的鼓风动能及回旋区长度;
b)
能人工修改风口直径、风口长度、工作风口个数等参数,并模拟不同送风参数下的初始气流状
态。
6.1.3.7 高炉炉渣粘度模型
高炉炉渣粘度模型是依据炉渣离子理论,结合炉渣成分计算得到炉渣粘度,用于指导高炉现场进行
炉渣流动性判断与调整。该模型应满足以下功能要求:
a)
自动计算炉渣对应的炉渣粘度;
b)
自动计算炉渣在低温区域的液相占比;
c)
自动计算炉渣的粘度与温度关系曲线。
6.1.3.8 有害元素模型
有害元素模型以元素平衡为机理,对炉内有害元素带入、支出、蓄积状态进行计算、监控和跟踪。
该模型应满足以下功能要求:
a)
自动统计分析高炉内部有害元素的负荷、收入、支出、蓄积情况;
b)
对高炉内部有害元素过量蓄积的状态进行预判预报。
6.1.3.9 高炉热平衡模型
高炉热平衡模型依据物理热、化学反应热、高炉内部热状态规律等基础理论,计算高炉内部物理化
学过程的各项热量收入支出,用于判断高炉能量利用情况以及内部热状态。该模型应满足以下功能要求:
a) 自动计算高炉能量利用水平及热效率;
b) 自动计算当前高炉状态下的炉热状态及热指数。
6.1.3.10 高炉物料平衡模型
高炉物料平衡模型依据元素平衡理论,结合炉内物理化学过程,计算并量化高炉物料收入和支出情
况。该模型应满足以下功能要求:
a) 根据槽下排料信号,自动统计每批料的重量、料种、批次信息;
b) 自动计算每批料的批铁、焦比、煤比、碱度等指标;
c) 按照小时、天、月不同频率统计高炉的物料消耗与支出。
6.1.3.11 高炉配料控制模型
6
T/CISA415—2024
高炉配料控制模型是根据元素平衡定律,对高炉的物料配方进行计算,并与控制系统联动,实现高
炉配料过程的自动计算与自动执行。该模型应满足以下功能要求:
a)
根据料种信息、设定的目标[Si]含量和碱度(R2/R3/R4),自动计算满足设定条件的吨铁炉料
配比;
b) 自动绘制不同配比炉渣成分对应的炉渣粘度-温度曲线;
c) 按照配料方案自动对槽下料仓排料方案进行分配与执行。
6.1.3.12 碱度调整控制模型
碱度调整控制模型是以高炉物料平衡为理论基础,通过监控原燃料成分、炉渣和铁水成分,自动对
高炉碱度进行调整。该模型应满足以下功能要求:
a)
实时监控原燃料成分波动。若原燃料成分出现波动,自动进行碱度校核计算;
b)
实时监控炉渣和铁水成分。若有新的炉渣和铁水成分时,自动进行碱度校核计算;
c)
根据现场操作要求,定期对碱度进行自动校核;
d)
对碱度进行校验后,应根据目标碱度、料仓存储情况等因素重新计算配料方案,并将校核后的
配料方案自动下发到槽下料仓排料执行。
6.1.3.13
高炉喷吹燃料控制模型
高炉喷吹燃料控制模型是以高炉物料平衡、热平衡原理为基础,计算出当前高炉状态下合理的燃料
比,并实现喷吹燃料的自动控制。该模型应满足以下功能要求:
a)
根据历史数据自动计算当前高炉状态下合理的操作燃料比;
b)
计算当前高炉料速与风量的匹配关系,进行塌料预测;
c)
根据高炉煤气利用率波动、炉墙热负荷波动、料速波动、原燃料成分波动情况计算当前高炉状
态下合理的喷吹燃料量;
d) 将计算的喷吹燃料量自动下发到控制系统执行。
6.1.3.14 能源分析模型
能源分析模型通过对高炉生产过程能源介质消耗进行监控,分析重点耗能节点,并给出节能优化方
向。该模型应满足以下功能要求:
a)
自动对本体冷却系统、炉顶上料系统、出铁场渣铁排放等能耗节点的能源消耗情况进行在线监
控;
b)
自动分析重点能耗节点,并对节能降耗方向提供建议。
6.1.4 数据科学模型
6.1.4.1 多维变量工况预警模型
多维变量工况预警模型从数据关联性层面实现高炉异常工况的提前预警,同时提供导致异常工况的
影响因素贡献率。该模型应满足以下功能要求:
a)
对异常工况数据进行自动预警;
b)
对引起异常工况的数据进行追溯分析。
6.1.4.2 铁水温度预测模型
铁水温度预测模型是以预测类算法为基础,通过分析影响高炉铁水温度的因子,对高炉铁水温度进
行预测。该模型应满足以下功能要求:
a)
对各类影响铁水温度的因子自动进行主次筛选,并自动分析各因子与铁水温度之间在时间上的
先后关系;
b)
在线实时计算并预测铁水温度。
6.2 模型验证
7
T/CISA 415—2024
6.2.1 概述
模型验证指基于现有条件,通过模型运行效果、客观检测数据、经验性的知识对模型的准确性进行
验证,下述模型宜按照文中所述方式进行验证,并满足以下精度要求。
6.2.2 高炉炉顶在线布料仿真模型
宜在高炉休风期间使用 3D 扫面仪对料面形状进行实际扫面,并将扫面结果与模拟料面形状进行比
对。中心区域凸凹特性及边缘区域形貌特性的模拟结果应与实际扫面结果一致。
在高炉生产过程中,如果现场配置了线料面测量装置监测,模型计算结果应该与在线测料面装置监
测结果一致。
6.2.3 高炉块状带仿真模型
模型计算的结果指标冶炼周期应与现场操作人员的经验判断一致。
6.2.4 高炉炉缸炉底炭砖侵蚀残厚仿真模型
宜在高炉大修期间对炉缸破损情况进行调研,并选定 4 个以上的剖面位置进行测量。剖面测量结果
与模型计算结果的偏差应小于 10%。
6.2.5 高炉喷吹燃料控制模型
模型建议喷吹燃料量应比实际操作喷吹燃料量更合理,可按照以下方式进行评价:
a)
以班组为统计单位,计算这两种喷吹燃料量分别对应的铁水[Si]均值;
b)
模型喷吹燃料量对应的铁水[Si],应按照燃料比与铁水[Si]的经验关系进行折算;
c)
模型建议喷吹燃料量对应的铁水[Si]应更符合现场铁水目标[Si]设定范围。
6.2.6 多维变量工况预警模型
模型预警结果与高炉操作人员经验判断结果的一致率应大于 85%。
6.2.7 铁水温度预测模型
模型预测结果与铁水温度实测值的差值小于 15℃的比例应大于 80%。
6.2.8 高炉诊断推理机模型
对于塌料、滑料、悬料、管道、结瘤、渣皮脱落等现象类诊断,模型诊断结果与高炉操作人员经验
判断结果的一致率应大于 85%。
6.3 模型融合
高炉数字虚体的构建需要对多类模型进行融合。对高炉进行工业建模时,需系统考虑模型间的耦合
性,应至少包括以下内容:
a)
高炉块状带仿真模型的料层分布应与高炉炉顶在线布料模型中的料层分布一致;
b)
高炉块状带仿真模型的炉料下移过程应考虑高炉操作炉型及挂渣厚度仿真模型的炉型变化;
c)
炉缸出铁平衡模型所依据的炉缸尺寸应根据炉缸侵蚀模型计算的内型进行动态修正。
7 应用场景
7.1 可视化
将高炉实时生产数据、工业视频等信息与虚拟场景中的设备进行点位绑定,对高炉生产过程进行多
视角、多场景、全方位实时、透明、可视化监控,使操作人员、技术人员与管理人员能实时、直观、高
8
T/CISA415—2024
效掌握高炉生产运行状态。可视化的内容应满足 T/CISA 201—2022 中 9.5 的规定。
7.2 设备故障诊断
对高炉及相关设备进行故障诊断,可分析高炉冷却壁、风口等设备的损坏机理,完善设备故障诊断
机制,进行设备的预测性维护。
7.3 工艺参数优化
在高炉数字虚体中模拟计算不同高炉操作输入参数下对应的高炉生产效率、产量、燃料消耗、铁水
质量等指标,降低高炉工艺调优过程中的试错成本。工艺参数的优化应满足 T/CISA 201—2022 中 9.3
的规定。
7.4 生产过程控制
可实时监控高炉内部的物理化学过程变化,对其发展趋势进行预判,提前进行针对性调整,并下发
至控制器,实现对高炉生产过程控制、提高高炉状态稳定性。
7.5 数字孪生实训
通过模拟高炉操作环境,为现场工程师提供高炉操作培训,以提升其技术能力和实际操作技能。
9